-
- 015Н18К13М5ТЮ
- 015Н18М4ТЮ
- 015Х14Н19С6Б
- 015Х18М2Б
- 015Х18Н15Р09
- 015Х18Н15Р13
- 015Х18Н15Р17
- 015Х18Н15Р22
- 015Х18Н15Р30
- 015Х20Н25Г2Б
- 01Н18К9М5Т
- 01Х18
- 01Х18М2Т
- 01Х18Н40М5ГБ
- 01Х18Н40М5ГБР
- 01Х19Ю3БЧ
- 01Х25М2Т
- 01Х25Т
- 01Х25ТБЮ
- 02Н15К10М5Ф5
- 02Н18М3К3Т
- 02Х17Н14М3
- 02Х18Н11
- 02Х21Н25М5ДБ
- 02Х25Н22АМ2
- 02Х8Н22С6
- 03Н10Х12Д2Т
- 03Н14Х5М3Т
- 03Н14Х5М3ТЮ
- 03Н15К10М5Ф5
- 03Н17К10В10МТ
- 03Н18К1М3ТЮ
- 03Н18К8М3ТЮ
- 03Н18К9М5Т
- 03Н18К9М5ТЮ
- 03Н18М3ТЮ
- 03Н18М4ТЮ
- 03Х11Н10М2Т
- 03Х11Н10М2Т1
- 03Х11Н10М2Т2
- 03Х11Н8М2Ф
- 03Х12Н10МТР
- 03Х12Н8К5М2ТЮ
- 03Х12Н8МТЮ
- 03Х13АГ19
- 03Х13Н5М5К9
- 03Х13Н8Д2ТМ
- 03Х16Н15М3Б
- 03Х17АН9
- 03Х17Н14М2
- 03Х17Н14М3
- 03Х17Н8Г5МФАБ
- 03Х18Н10Т
- 03Х18Н11
- 03Х18Н12
- 03Х18Н12Т
- 03Х18Н15М
- 03Х19Н15Г6М2АВ2
- 03Х20Н45М4БРЦ
- 03Х20Н45М4БЧ
- 03Х20Н45М5Б
- 03Х20Ю3НТБ
- 03Х21Н21М4ГБ
- 03Х21Н25М5ДБ
- 03Х21Н32М3Б
- 03Х22Н6М2
- 03Х23Н6
- 03Х24Н6АМ3
- 03Х9К14Н6М3Д
- 03ХН28МДТ
- 04Х11Н9М2Д2
- 04Х13Н4АГ20
- 04Х14К13Н4М3ТВ
- 04Х15Н11С3МТ
- 04Х15СТ
- 04Х16Н11М3Т
- 04Х17Т
- 04Х18Н10
- 04Х19МАФТ
- 04Х25Н5М2
- 05Х12Н2К3М2АФ
- 05Х12Н2М
- 05Х12Н5К14М5ТВ
- 05Х12Н9М2С3
- 05Х15Н9Г6АМ
- 05Х18Н10Т
- 05Х20Н15АГ6
- 05Х20Н32Т
- 05Х21Н12Г2БРЧ
- 05ХГБ
- 05ХН46МВБЧ
- 06Х13Н4ДМ
- 06Х13Н7Д2
- 06Х14Н5МФ
- 06Х14Н6Д2МБТ
- 06Х15Н4ДМ
- 06Х15Н6МВФБ
- 06Х16Н15М2Г2ТФР
- 06Х16Н15М3Б
- 06Х16Н15М3БР
- 06Х16Н2К5ФМБ
- 06Х18Г9Н5АБ
- 06Х18Н10Т
- 06Х18Н11
- 06Х20Н14С2
- 06ХН28МДТ
- 06ХН28МТ
- 07Х12НМБФ
- 07Х12НМФБ
- 07Х13АГ20
- 07Х15Н30В5М2
- 07Х15Н7ЮМ2
- 07Х16Н4Б
- 07Х16Н6
- 07Х17Н16
- 07Х18Н10Р
- 07Х21Г7АН5
- 07Х25Н16АГ6Ф
- 07Х25Н16АГЦ
- 08Х10Н20Т2
- 08Х13
- 08Х14МФ
- 08Х14Н2К3МФБ
- 08Х14Ф
- 08Х15Н24В4ТР
- 08Х15Н25М3ТЮБ
- 08Х15Н25Т2МФР
- 08Х15Н5Д2Т
- 08Х15Н5Д2ТУ
- 08Х16Н11М3
- 08Х16Н13М2Б
- 08Х17
- 08Х17Н13М2Т
- 08Х17Н15М3Т
- 08Х17Н5М3
- 08Х17Н6Т
- 08Х17Т
- 08Х18Г8Н2Т
- 08Х18Н10
- 08Х18Н10Т
- 08Х18Н12Б
- 08Х18Н12Т
- 08Х18Н4Г11АФ
- 08Х18Н5Г11БАФ
- 08Х18Н5Г12АБ
- 08Х18Т1
- 08Х18ТЧ
- 08Х19Н12ТФ
- 08Х20Н12АБФ
- 08Х20Н14С2
- 08Х20Н4АГ10
- 08Х20Н5АГ12МФ
- 08Х21Г11АН6
- 08Х21Н6М2Т
- 08Х22Н6Т
- 08ХГСДП
- 09Х14Н16Б
- 09Х14Н19В2БР
- 09Х14Н19В2БР1
- 09Х15Н8Ю
- 09Х15Н8Ю1
- 09Х16Н13М3
- 09Х16Н15М3Б
- 09Х16Н16МВ2БР
- 09Х16Н4Б
- 09Х16Н7М2Ю
- 09Х17Н
- 09Х17Н7Ю
- 09Х17Н7Ю1
- 09Х18Н10Т
- 09Х18Н9
- 0Х20Н4АГ10
- 10ГН2МФА
- 10Х11Н20Т2Р
- 10Х11Н20Т3Р
- 10Х11Н23Т3МР
- 10Х12Н20Т2
- 10Х12Н22Т3МРУ
- 10Х12Н3М2БФ
- 10Х12Н3М2ФА
- 10Х12НД
- 10Х13Г12БС2Н2Д2
- 10Х13Г12С2Н2Д2Б
- 10Х13Г18Д
- 10Х13СЮ
- 10Х14АГ15
- 10Х14Г14Н3
- 10Х15Н27Т3МР
- 10Х15Н28В2М4Б
- 10Х17Н13М2Т
- 10Х17Н13М3Т
- 10Х18Н10Т
- 10Х18Н5Г9АС4
- 10Х18Н9
- 10Х23Н18
- 10Х25Н6АТМФ
- 10Х2М1ФБ
- 10Х2МФБ
- 10Х32Н4Д
- 10Х32Н8
- 10Х9МФБ
- 10Х9НСМФБ
- 11Х11Н2В2МФ
- 11Х13Н3
- 11Х17Н
- 12Х11В2МФ
- 12Х12М1БФР
- 12Х13
- 12Х13Г12АС2Н2
- 12Х15Г9НД
- 12Х17
- 12Х17Г9АН4
- 12Х18Н10Е
- 12Х18Н10Т
- 12Х18Н12Т
- 12Х18Н9
- 12Х18Н9Т
- 12Х1МФ
- 12Х20Н14С2
- 12Х21Н5Т
- 12Х25Н16Г7АР
- 12Х2МФСР
- 12ХМ
- 12Ю
- 13Х11Н2В2МФ
- 13Х13С2М2
- 13Х14Н3В2ФР
- 13Х15Н4АМ3
- 13Х16Н3М2АФ
- 14Х17Н2
- 14Х20Н25В5МБ
- 15Х11МФ
- 15Х12ВНМФ
- 15Х12Н2МВФАБ
- 15Х16К5Н2МВФАБ
- 15Х16Н2АМ
- 15Х17АГ14
- 15Х18Н12С4ТЮ
- 15Х18СЮ
- 15Х1М1Ф
- 15Х25Т
- 15Х28
- 15Х5М
- 15Х6СЮ
- 15ХМ
- 16Х
- 16Х11Н2В2МФ
- 16Х12В2ФТАР
- 16Х12ВМСФ5Р
- 16Х12МВСФБР
- 16Х16Н3МАД
- 16Х20К6Н2МВФ
- 16ЮХ
- 17Х18Н9
- 17ХНГТ
- 18Х11МНФБ
- 18Х12ВМБФР
- 18Х13Н3
- 18Х14Н4АМ3
- 18Х15Н3М
- 18Х3МВ
- 18Х3МФ
- 19Х20Н4АМ3Д2С
- 1Х14Н14В2М
- 20Х12ВНМФ
- 20Х12НМВБФАР
- 20Х13
- 20Х13Н2ДМЮФ
- 20Х13Н4Г9
- 20Х17Н2
- 20Х1М1Ф1БР
- 20Х1М1Ф1ТР
- 20Х20Н14С2
- 20Х23Н13
- 20Х23Н18
- 20Х25Н20С2
- 21НКМТ
- 22Х15КТФ
- 24НХ
- 25НЮ
- 25Х12Н2В2М2Ф
- 25Х13Н2
- 25Х13Н2ВМФ
- 25Х15КЮБФ
- 25Х17Н2
- 25Х17Н2Б
- 25Х18Н10В2
- 25Х18Н8В2
- 25Х1М1Ф
- 25Х1М1ФА
- 25Х1МФ
- 25Х2М1Ф
- 26Х14Н2
- 27КХ
- 29НК
- 2Х7В9М2К9
- 30НКД
- 30Х13
- 30Х13Н7С2
- 30ХМ
- 30ХМА
- 31Н3Х
- 31Н4Х
- 31Н6Х
- 31Н8Х
- 31НХ3Г
- 32НК
- 32НКД
- 32НХ3
- 32Х13Н6К3М2БДЛТ
- 33Н2Х
- 33Н5Х
- 33НК
- 33НХ3
- 34Н2Х
- 34НКД
- 34НКМ
- 35КХ6Ф
- 35КХ8Ф
- 35Н2Х
- 35ХМ
- 36КНМ
- 36Н
- 36Н11Х
- 36НХ
- 36НХТЮ
- 36НХТЮ5М
- 36НХТЮ8М
- 36Х18Н25С2
- 36ХНТЮ
- 37Х12Н8Г8МФБ
- 38НКД
- 38НХМ
- 38Х2МЮА
- 40К27ХНМ
- 40Х10С2М
- 40Х13
- 40Х15Н7Г7Ф2МС
- 40Х18Н2М
- 40Х9С2
- 40ХНЮ
- 42Н
- 42НА-ВИ
- 42НХТЮ
- 42Х11М3Ф
- 44НХМТ
- 44НХТЮ
- 45Н
- 45НХТ
- 45Х14Н14В2М
- 45Х14Н14СВ2М
- 45Х22Н4М3
- 45Х25Н20С
- 45Х28Н49В5С
- 46НХТ
- 46ХНМ
- 47Н3Х
- 47НД
- 47НХ
- 47НХР
- 48НХ
- 49К2Ф
- 49К2ФА
- 49К2ФН
- 49КФ
- 49КФ2
- 4Х13Н6ЛВФ
- 4Х18Н2М
- 50Н
- 50Н3ХЮ
- 50Н6МФА
- 50НХС
- 50Х15МФАСЧ
- 50Х25Н35С2Б
- 50Х4Г18
- 52К10Ф
- 52К11Ф
- 52К12Ф
- 52К13Ф
- 52К5Ф
- 52К7Ф
- 52К9Ф
- 52Н
- 55Х20Г9АН4
- 55Х20Г9АН4Б
- 58Н
- 58НХВКТБЮ
- 5Х14В
- 5Х3Н12Г5
- 60Х3Г8Н8В
- 60Х3Г8Н8Ф
- 64Н
- 65Х13
- 67Н26М
- 68НХВКТЮ
- 79НМ
- 80Н2М
- 80НМ
- 80НМВ
- 80НХС
- 80Х20НС
- 81НМА
- 82Н6ХБ
- 90Г29Ю9ВБМ
- 95НИ
- 95Х13М3К3Б2Ф
- 95Х18
- 95Х18МФ
- 9Х13Н6ЛК4
- ЕВ6
- ЕХ3
- ЕХ5К5
- ЕХ9К15М2
- Н65Д29ЮТ
- Н65М
- Н70МФ
- Н70МФВ
- Н95Г
- НВМГ3-0,05В
- НВМГ3-0,08В
- НМГ0,05В
- НМГ0,08В
- Х15Ю5
- Х17Н14М2Т
- Х17Н14М3Т
- Х18Н13С2АМВФ5Р
- Х20Н32Т
- Х20Н80
- Х23Ю5
- Х23Ю5Т
- Х27Ю5Т
- Х33ТМДЮ
- ХК30НВМТ
- ХН20ЮС
- ХН28ВМАБ
- ХН30ВМТ
- ХН30МДБ
- ХН30ТДЮ
- ХН32Т
- ХН33КВЮ
- ХН35ВБ
- ХН35ВТ
- ХН35ВТЮ
- ХН35КВТ
- ХН35МТЮ
- ХН38ВБ
- ХН38ВТ
- ХН40Б
- ХН40МДБ
- ХН40МДТЮ
- ХН43БМТЮ
- ХН45МВТЮБР
- ХН45ТЮ
- ХН45Ю
- ХН46Б
- ХН50ВМТКФЮ
- ХН50ВМТЮБ
- ХН50МВКТЮР
- ХН50МД
- ХН51ВМТЮКФР
- ХН51МТЮКФР
- ХН52БМКТЮ (ЭК79)
- ХН52КВМТЮБ
- ХН55ВМТКЮ
- ХН55ВМТФКЮ
- ХН55МБЮ
- ХН55МВЦ
- ХН55МВЮ
- ХН56ВМКЮ
- ХН56ВМТЮ
- ХН56МБЮД
- ХН57МКЮВТБР
- ХН57МТВЮ
- ХН58В
- ХН58ВМКЮР
- ХН58МБЮ
- ХН58МБЮД
- ХН60ВТ
- ХН60КВЮМБ
- ХН60КМЮБВТФ
- ХН60КМЮВТБ
- ХН60М
- ХН60МВТЮ
- ХН60МЮВТ
- ХН60Ю
- ХН62БМВЮ
- ХН62БМКТЮ
- ХН62ВМКЮ
- ХН62ВМТЮ
- ХН62ВМЮТ
- ХН62МВКЮ
- ХН63МБ
- ХН65ВМБЮ
- ХН65ВМТЮ
- ХН65КМВЮБ
- ХН65МВ
- ХН65МВУ
- ХН67ВМТЮ
- ХН67МБЮ
- ХН67МВТЮ
- ХН68ВМТЮК
- ХН70ВМТЮ
- ХН70ВМТЮФ
- ХН70ВМФТЮ
- ХН70ВМЮТ
- ХН70МВТЮБ
- ХН70МВЮ
- ХН70Ю
- ХН73МБТЮ
- ХН75ВМФЮ
- ХН75ВМЮ
- ХН75МБТЮ
- ХН75ТБЮ
- ХН77ТЮ
- ХН77ТЮР
- ХН77ТЮРУ
- ХН78Т
- ХН80ТБЮ
- ХН85МЮ
- ЮНДК24
-
- 05Х12Н6Д2МФСГТ
- 05Х13Н6М2
- 11М5Ф
- 11Р3АМ3Ф2
- 11Х4В2МФ3С2
- 11ХФ
- 12Х1
- 13Х
- 3Х2В8Ф
- 3Х2МНФ
- 3Х2Н2МВФ
- 3Х3М3Ф
- 40Х5МФ
- 45ХНМ
- 4Х2В5МФ
- 4Х2НМФ
- 4Х3ВМФ
- 4Х3М2ВФГС
- 4Х4ВМФС
- 4Х5В2ФС
- 4Х5МФ1С
- 4Х5МФС
- 4Х8В2
- 4ХВ2С
- 4ХМНФС
- 4ХМФ
- 4ХМФС
- 4ХС
- 50Х14МФ
- 55СМ5ФА
- 55Х7ВСФМ
- 5Х2ГСМФ
- 5Х2МНФ
- 5Х3В3МФС
- 5ХАНМФ
- 5ХВ2С
- 5ХВ2СФ
- 5ХГМ
- 5ХГСМФ
- 5ХНВ
- 5ХНВС
- 5ХНМ
- 60Х2СМФ
- 60ХГ
- 60ХН
- 6Х3МФС
- 6Х4М2ФС
- 6Х6В3МФС
- 6Х6М1Ф
- 6Х7В7ФМ
- 6ХВ2С
- 6ХВГ
- 6ХС
- 75ХМ
- 75ХМФ
- 75ХСМФ
- 7Н2МФА
- 7Х15ВМФСН
- 7Х2СМФ
- 7Х3
- 7ХГ2ВМ
- 7ХГ2ВМФ
- 7ХНМ
- 7ХФ
- 8Х3
- 8Х4В2МФС2
- 8Х6НФТ
- 8ХФ
- 90ХМФ
- 95Х6М3Ф3СТ
- 9Х1
- 9Х1Ф
- 9Х2
- 9Х2МФ
- 9Х4М3Ф2АГСТ
- 9Х5ВФ
- 9Х6Ф2АРСТГ
- 9ХВГ
- 9ХС
- 9ХФ
- 9ХФМ
- Р10К5Ф5
- Р12
- Р12М3К5Ф2
- Р12МФ5-МП
- Р12Ф2К5М3
- Р12Ф2К8М3
- Р12Ф3
- Р12Ф3К10М3
- Р12Ф5М
- Р13Ф4К5
- Р14Ф4
- Р18
- Р18К5Ф2
- Р18Ф2К8М
- Р2АМ9К5
- Р6АМ5
- Р6АМ5Ф3
- Р6М5
- Р6М5К5
- Р6М5Ф3
- Р6Ф2К8М5
- Р8Ф2К8М5
- Р9
- Р9К10
- Р9К5
- Р9М4К6С
- Р9М4К8
- Р9Ф5
- У10 / У10А
- У11А
- У12
- У12А
- У13А
- У16
- У7
- У7А
- У8 / У8А
- У8Г
- У8ГА
- У9
- У9А
- Х12
- Х12ВМ
- Х12М
- Х12МФ
- Х12Ф1
- Х6ВФ
- Х6Ф4М
- Х9ВМФ
- ХВ4Ф
- ХВГ
- ХВСГФ
- ХГС
-
- 01Н17К12М5Т
- 03Н18К8М5Т
- 03Н19К6М5ТР
- 03Х14Н7В
- 03Х19АГ3Н10
- 03Х19Г10Н7М2
- 03Х20Н16АГ6
- 03ХГЮ
- 04Х14Т3Р1Ф
- 05Х18Н10АГ10МБ
- 06Г2АФ
- 06Г2МФБ
- 06Г2ФР
- 06Х1Ф
- 06ХГР
- 06ХГСЮ
- 06ХФ
- 07ГБЮ
- 07ГФБ
- 07Х3ГНМЮА
- 08Г2МФ
- 08Г2С
- 08Г2СФБ
- 08Г2Т
- 08Г2ФБТ
- 08ГБЮ
- 08ГБЮТР
- 08Х16Н9М2
- 08Х18Н10ГТ
- 08Х2Г2ФА
- 08ХМФЧА
- 08Ю
- 08ЮА
- 08ЮП
- 08ЮПР
- 09Г2
- 09Г2Д
- 09Г2С
- 09Г2СД
- 09ГБЮ
- 09ГСНБЦ
- 09Н2МФБА
- 09СФА
- 09Х16НМ2Д
- 09ХГ2НАБЧ
- 09ХГН2АБ
- 09ХН2МД
- 09ХН3МД
- 09ХН4МД
- 100ХНМФ
- 10Г2
- 10Г2Б
- 10Г2БД
- 10Г2С1Д
- 10Г2СБ
- 10Г2СФБ
- 10Г2Т
- 10Г2ФБ
- 10Г2ФБЮ
- 10ГНБ
- 10ГТ
- 10Х14Г14Н4Т
- 10Х1С2М
- 10Х2ГНМ
- 10Х2М
- 10Х2М1
- 10Х3ГНМЮА
- 10ХГСН1Д
- 10ХДП
- 10ХН1М
- 10ХН3МД
- 10ХНДП
- 10ХСНД
- 10ЮА
- 110Х18М
- 11МТЮА
- 11Х18М
- 11ЮА
- 120Г13
- 12Г1Р
- 12Г2АФ
- 12Г2Б
- 12Г2МФТ
- 12Г2С
- 12Г2СБ
- 12Г2СМФ
- 12Г2СМФАЮ
- 12ГН2МФАЮ
- 12ГС
- 12ГСБ
- 12ГФ
- 12К
- 12МХ
- 12Х18Н10ГТ
- 12Х2МФА
- 12Х2Н4А
- 12Х2НВФА
- 12Х2НВФМА
- 12Х2НМ1ФА
- 12Х2НМФА
- 12Х3ГНМФБА
- 12Х8
- 12Х8ВФ
- 12ХГДАФ
- 12ХГН2МФБДАЮ
- 12ХГНМФ
- 12ХН
- 12ХН2
- 12ХН2А
- 12ХН2МД
- 12ХН3А
- 12ХН3МД
- 12ХН4МБД
- 12ХСНД
- 138ИЗ-2
- 13Г1С
- 13Г1СБ
- 13Г2АФ
- 13ГС
- 13Н2ХА
- 13Х3Н3М2ВФБ
- 13Х3НВМ2Ф
- 13ХГМРБ
- 13ХГН2МД
- 13ХГН2МФД
- 13ХГСН1МД
- 13ХФА
- 13ХФЮ
- 14Г2
- 14Г2АФ
- 14Г2АФД
- 14ГС
- 14ГФ
- 14Н2МФД
- 14Х2ГМР
- 14Х2Н3МА
- 14Х3ГМЮ
- 14ХГ2САФД
- 14ХГМДЦ
- 14ХГН
- 14ХГН2МДАФБ
- 14ХГНМДАФБРТ
- 14ХГС
- 14ХГСН2МА
- 14ХН3МА
- 15Г
- 15Г2АФД
- 15Г2СФ
- 15Г2СФД
- 15Г2ФБЮ
- 15ГС
- 15ГФД
- 15ГЮТ
- 15К
- 15Н3МА
- 15ФЮА
- 15Х
- 15Х16Н3КАМФ2
- 15Х1СМФБ
- 15Х2ГМФ
- 15Х2ГН2ТА
- 15Х2ГН2ТРА
- 15Х2НМФА
- 15Х5
- 15Х5ВФ
- 15ХА
- 15ХГН2МАФАЧ
- 15ХГН2ТА
- 15ХГНМ
- 15ХДП
- 15ХМФА
- 15ХН3
- 15ХР
- 15ХСМФБ
- 15ХСНД
- 15ХФ
- 15ЮА
- 16Г
- 16Г2
- 16Г2АФ
- 16Г2АФД
- 16Г2СФ
- 16ГД
- 16ГМЮЧ
- 16ГНМА
- 16ГС
- 16ГФБ
- 16К
- 16Х2Н3МФБАЮ
- 16Х3НВФМБ
- 16ХГ
- 16ХГТА
- 16ХН3МА
- 16ХСН
- 17Г1С
- 17ГС
- 17Н3МА
- 17ХГ
- 18Г2АФ
- 18Г2АФД
- 18Г2С
- 18Г2ХФЮД
- 18К
- 18Х20Н13
- 18Х2МФА
- 18Х2Н4ВА
- 18Х2Н4МА
- 18ХГ
- 18ХГН2МФБ
- 18ХГТ
- 18ХН2Т
- 18ХН3МА
- 18ХНВА
- 18ХНМФД
- 18ЮА
- 18ЮТ
- 19Х2НВФА
- 19Х2НМФА
- 19ХГН
- 19ХГНМА
- 19ХГС
- 19ЮФТ
- 1Х2М1
- 20-КС
- 20Г
- 20Г2
- 20Г2АФ
- 20Г2Р
- 20Г2С
- 20ГСФ
- 20ГЮТ
- 20К
- 20Ф
- 20Х
- 20Х2М
- 20Х2МА
- 20Х2МФА
- 20Х2Н4А
- 20Х2Н4МФ
- 20Х3МВФ
- 20Х3МВФА
- 20Х3НМФ
- 20ХГ2Ц
- 20ХГНМ
- 20ХГНМТ
- 20ХГНР
- 20ХГНТР
- 20ХГР
- 20ХГСА
- 20ХГСН2МФА
- 20ХГСНМ
- 20ХМ
- 20ХН
- 20ХН2М
- 20ХН2МА
- 20ХН3А
- 20ХН3МФА
- 20ХН4ФА
- 20ХНР
- 20ХФА
- 20ЮА
- 20ЮЧ
- 21Н5А
- 21Х2НВФА
- 21Х2НМФА
- 22ГЮ
- 22К
- 22Х2Г2Р
- 22Х3М
- 22ХГНМА
- 22ХНМ
- 23Г2Д
- 23Х2НВФА
- 23Х2НМФА
- 23ХН2М
- 24Г2
- 24Х3МФ
- 24ХНМ
- 25Г
- 25Г2С
- 25ГС
- 25Н
- 25Н3А
- 25Х20Н9В2М
- 25Х2ГНТА
- 25Х2ГНТРА
- 25Х2МФА
- 25Х2Н4ВА
- 25Х2Н4МА
- 25Х2Н4МФА
- 25Х2НМФ
- 25Х3МФА-А
- 25Х5М
- 25ХГМ
- 25ХГМНТБА
- 25ХГНМА
- 25ХГНМТ
- 25ХГСА
- 25ХГСНМА
- 25ХГТ
- 25ХМ
- 25ХН3
- 25ХН3МФА
- 25ХНТЦ
- 25ХСНВФА
- 26Г1
- 26Г2СТА
- 26Х2НВМБР
- 26ХГМ
- 26ХМА
- 26ХН3М2ФА
- 26ХН3МФ
- 26ХН4МФ
- 27ХГР
- 27ХН3М2ФА
- 27ХН3МФА
- 28Х3СНМВФА
- 28ХГНМФД
- 28ХН3МФА
- 30Г
- 30Г1Р
- 30Г2
- 30Т
- 30Х
- 30Х2ГСН2ВМ
- 30Х2ГСНВМ
- 30Х2Н2ВФА
- 30Х2Н2ВФМА
- 30Х2Н2СВМФА
- 30Х2НВА
- 30Х2НВФА
- 30Х2НВФМА
- 30Х2НМА
- 30Х2НМФА
- 30Х3ВА
- 30Х3МА
- 30Х3МФ
- 30Х3МФСА
- 30Х3НВА
- 30ХГС
- 30ХГСА
- 30ХГСН2А
- 30ХГСН2МА
- 30ХГТ
- 30ХН2ВА
- 30ХН2ВФА
- 30ХН2МА
- 30ХН2МФА
- 30ХН3А
- 30ХН3М
- 30ХН3М1ФА
- 30ХН3М2ФА
- 30ХНМФА
- 30ХРА
- 30ХСНВФА
- 32Г2
- 32Г2С
- 32Х2НВМБР
- 32ХН8М1ФК5А
- 33Х3СНМВФА
- 33ХН3МА
- 33ХС
- 34ХМ1А
- 34ХМА
- 34ХН1ВА
- 34ХН1М
- 34ХН1МА
- 34ХН3М
- 34ХН3МА
- 35Г
- 35Г2
- 35Г2Ф
- 35Г2ФА
- 35ГС
- 35Х
- 35Х2ГЮФ
- 35Х3НМ
- 35ХГ2
- 35ХГН2
- 35ХГСА
- 35ХМА
- 35ХМФА
- 35ХН1М2ФА
- 35ХН2Ф
- 35ХН3МА
- 35ХН3МФА
- 35ХС2Н3М1ФА
- 35ХСН3М1А
- 36Г2С
- 36Г2СР
- 36Х2Н2МФА
- 36ХН3МФА
- 37Г2С
- 37Х2НВМБР
- 37ХН3А
- 38Х2Н2ВА
- 38Х2Н2МА
- 38Х2Н3М
- 38Х2НМ
- 38Х2НМФ
- 38Х2Ю
- 38Х3М1Ф1А
- 38Х3СНМВФА
- 38ХА
- 38ХВ
- 38ХГМ
- 38ХГН
- 38ХГНМ
- 38ХГСА
- 38ХМ
- 38ХМА
- 38ХМФЮА
- 38ХН3А
- 38ХН3ВА
- 38ХН3МА
- 38ХН3МФА
- 38ХНМ
- 38ХС
- 38ХФР
- 40Г
- 40Г18Ю3Ф
- 40Г2
- 40ГМФР
- 40ГР
- 40Р
- 40Х
- 40Х2Н2ВА
- 40Х2Н2МА
- 40Х3М2ФА
- 40ХГНМ
- 40ХГСМА
- 40ХГТР
- 40ХМФА
- 40ХН
- 40ХН2ВА
- 40ХН2МА
- 40ХН2СВА
- 40ХН2СМА
- 40ХР
- 40ХС
- 40ХСН2МА
- 40ХФА
- 42Х2ГСНМ
- 42Х2НВМБР
- 42Х2НМБР
- 42ХМФА
- 43Х3СНМВФА
- 44Х2НМБР
- 45Г
- 45Г15Н9Х2ЮФ
- 45Г17Ю3
- 45Г2
- 45Х
- 45Х3НМ2ФА
- 45ХГМА
- 45ХН
- 45ХН2МФА
- 47ГТ
- 48ХН3М
- 50Г
- 50Г2
- 50Г23Х4ФВ7
- 50Х
- 50ХГ
- 50ХГА
- 50ХГФА
- 50ХН
- 50ХФА
- 51ХФА
- 55С2
- 55С2А
- 55С2ГФ
- 55ХГР
- 55ХФА
- 5ХНМ2
- 60Г
- 60С2
- 60С2А
- 60С2Г
- 60С2Н2А
- 60С2Х
- 60С2ХА
- 60С2ХФА
- 60Х13С
- 60ХФА
- 65Г
- 65ГА
- 65С2ВА
- 70Г
- 70Г14Н3
- 70Г2
- 70С2ХА
- 70С3А
- 70ХГФА
- 80Г20Ф2Ю
- 85Г13
- 85ГФ
- 8Х4В9Ф2
- 8Х4М4В2Ф1
- A36
- А11
- А12
- А20
- А35
- А40Г
- АК36
- АС12ХН
- АС14
- АС14ХГН
- АС19ХГН
- АС20ХГНМ
- АС30ХМ
- АС35Г2
- АС38ХГМ
- АС40Х
- АС40ХГНМ
- АС45Г2
- АСЦ30ХМ
- АЦ18ХГТ
- АЦ18ХН2Т
- АЦ20
- АЦ20Х
- АЦ20ХГНМ
- АЦ20ХН3
- АЦ25ХГТ
- АЦ28ХГН2АФБ
- АЦ28ХГН3ФТ
- АЦ30
- АЦ30Х
- АЦ30Х3МФ
- АЦ30ХМ
- АЦ35
- АЦ35Г2
- АЦ35Х
- АЦ38ХС
- АЦ40
- АЦ40Г
- АЦ40Х
- АЦ45
- АЦ45Г2
- АЦ45Х
- АЦ50
- Е55
- ст. 10
- ст. 15
-
ст. 20
- Круг г/к
- Круг калибр.
- Лист г/к
- Лист х/к
- Поковка
- Полоса г/к
- Труба - ГОСТ 10704-91
- Труба - ГОСТ 10705-80
- Труба - ГОСТ 10706-76
- Труба - ГОСТ 20295-85
- Труба - ГОСТ 32528-2013
- Труба - ГОСТ 3262-75
- Труба - ГОСТ 550-75
- Труба - ГОСТ 8639-82
- Труба - ГОСТ 8696-74
- Труба - ГОСТ 8732-78
- Труба - ГОСТ 8645-68
- Труба - ГОСТ 8734-75
- Труба сталь 20 - ГОСТ 9567-75
- Труба - ГОСТ 8731-74
- Труба - ГОСТ 8733-74
- ст. 25
- ст. 3
- ст. 30
- ст. 35
- ст. 40
- ст. 45
- ст. 50
- ст. 55
- ст. 58
- ст. 60
- ст. 65
- ст. 70
- ст. 75
- ст. 80
- ст. 85
- Х11МНАФБ
- Х56
- ШХ15
- ШХ15С2Г3
- ШХ15СГ
- ШХ15СМ
- ШХ20СГ
- ШХ4
-
- ст. 10850
- ст. 10860
- ст. 10864
- ст. 10880
- ст. 10895
- ст. 11850
- ст. 11860
- ст. 11880
- ст. 11895
- ст. 1211
- ст. 1212
- ст. 1213
- ст. 1311
- ст. 1312
- ст. 1313
- ст. 1411
- ст. 1412
- ст. 1413
- ст. 1512
- ст. 1513
- ст. 1514
- ст. 1521
- ст. 1561
- ст. 1562
- ст. 1571
- ст. 1572
- ст. 2011
- ст. 2012
- ст. 2013
- ст. 2014
- ст. 20850
- ст. 20880
- ст. 20895
- ст. 2111
- ст. 2112
- ст. 21850
- ст. 21860
- ст. 21880
- ст. 21895
- ст. 2211
- ст. 2212
- ст. 2311
- ст. 2312
- ст. 2411
- ст. 2412
- ст. 2413
- ст. 2421
- ст. 3311
- ст. 3404
- ст. 3405
- ст. 3406
- ст. 3407
- ст. 3408
- ст. 3411
- ст. 3412
- ст. 3413
- ст. 3414
- ст. 3415
- ст. 3421
- ст. 3422
- ст. 3423
- ст. 3424
- ст. 3425
- ст. 3471
- ст. 3472
Нержавеющие и жаропрочные стали и сплавы
Фотогаларея продукцииКомпания Апгрейд специализируется на поставке поковок, сортового, листового проката из нержавеющих и жаропрочных сталей и сплавов.
На складе нашей организации всегда в наличии широкий ассортимент сертифицированной металлопродукции, изготовленной согласно ГОСТ 8479-90, ГОСТ 1133-71, ГОСТ 2590-2006, ГОСТ 7417-75, 2879-2006, ГОСТ 19903-74, ГОСТ 19904-90, ГОСТ 103-2006, ГОСТ 82-70 и др.
Широкий ассортимент продукции, постоянный складской запас и сотрудничество с металлургическими комбинатами позволяет оперативно решать комплексные задачи и обеспечивать заказчика необходимым объемом сертифицированного металлопроката.
Продукция из наличия
Выбор продукции по марке стали
Наши преимущества
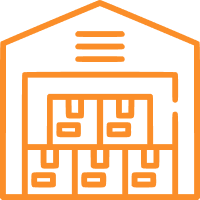
Постоянное складское наличие
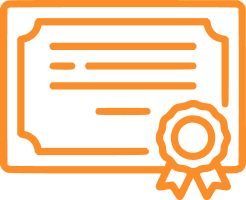
сертифицирована
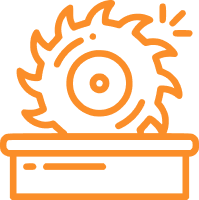
(резка, мех. обработка)

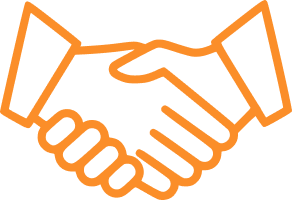
Персональный менеджер
Справочная информация
Легированные стали – это сплавы на основе Fe-C, в химический состав которых специально введены легирующие элементы, обеспечивающие при определенных способах обработки требуемую структуру и свойства.
Легирующие элементы – химические элементы, специально введенные в сталь для получения требуемой структуры, физико-химических и механических свойств.
Относительно недефицитные легирующие элементы |
Mn, Si, Cr, Al, Ti, V |
Дефицитные легирующие элементы |
Nb, Mo, Cu, Pb, Ta |
Особо дефицитные легирующие элементы |
W, Ni, Co |
Легирующими элементами также могут быть |
Zr, P, S, N, Se, Te, La |
Высоколегированные стали и сплавы получают методом электрошлакового (ЭШ), вакуумно-дугового (ВД) переплавов и индукционной электроплавкой (ЭП) и в зависимости от основных свойств подразделяют на следующие группы:
- коррозионностойкие;
- жаростойкие;
- жаропрочные.
1. Коррозионностойкие (нержавеющие) стали и сплавы.
Коррозией называется процесс самопроизвольного разрушения материалов вследствие химического или электрохимического взаимодействия с окружающей средой.
Химическая коррозия – протекает при непосредственном взаимодействии металла и среды без возникновения электрического тока.
Электрохимическая коррозия – разрушение металлов связано с возникновением электрического тока под действием электролитов или других причин.
Электрохимическая коррозия возникает при действии на металлы кислот, щелочей, воды и представляет для деталей механизмов и конструкций наибольшую опасность.
Виды коррозии металлов
Сплошная равномерная коррозия |
Коррозия, равномерно захватившая всю поверхность металла |
|
Сплошная неравномерная коррозия |
Коррозия, неравномерно захватившая всю поверхность металла |
|
Местная коррозия |
Поражения металла локальны |
|
Межкристаллитная коррозия |
Один из наиболее опасных видов коррозии. Разрушение металла происходит преимущественно вдоль границ зерен. Вызвана диффузионными процессами в структуре стали, приводящими к образованию карбидов хрома по границам зерен и одновременным обеднением хромом участков, непосредственно прилегающим к границам зерен. Такие поражения могут приводить к полной потере прочности и разрушению детали или конструкции. |
|
Транскристаллитная коррозия |
Один из наиболее опасных видов коррозии. Рассекает металл трещиной прямо через зерна, малозаметна. Такие поражения могут приводить к полной потере прочности и разрушению детали или конструкции. |
|
Ножевая коррозия |
Один из наиболее опасных видов коррозии, особенно ему подвержены сварные швы. Такая коррозия словно ножом разрезает металл при эксплуатации в агрессивных средах. Подобные поражения могут приводить к полной потере прочности и разрушению детали или конструкции. |
|
Коррозионностойкие стали и сплавы обладают стойкостью против химической и электрохимической коррозии (атмосферной, почвенной, щелочной, кислотной, межкристаллитной и коррозии под напряжением).
Коррозионностойкие стали и сплавы бывают низкоуглеродистые (с содержанием углерода менее 0,3 %) и среднеуглеродистые (массовая доля углерода более 0,3 %).
Значительное увеличение коррозионной стойкости сталей достигается введением в ее состав повышенного количества хрома. При его содержании более 12% возникает высокая устойчивость против коррозии. Происходит это вследствие образования тонкой плотной оксидной пленки, которая защищает сталь от агрессивной среды и разрушения.
Кроме хрома, для увеличения стойкости против коррозии и улучшения качества стали добавляют никель.
Наилучшими коррозионными свойствами обладают хромистые и хромоникелевые стали.
Хромистые коррозионностойкие стали
В зависимости от структуры хромистые стали делятся на следующие классы:
- мартенситные: 20Х13, 30Х13, 40Х13. Применяют для слабых агрессивных сред (воздух, вода, пар).
- мартенситно-ферритные (содержат более 10% феррита): 12Х13.
- ферритные: 12Х17, 15Х25Т, 15Х28 – низкоуглеродистые высокохромистые стали, обладают повышенной коррозионной стойкостью.
Структура для наиболее характерных сплавов этого типа:
Сталь |
Класс в зависимости от структуры |
Применение |
12Х13 |
мартенситно-ферритные |
Применяют для деталей, работающих в слабых агрессивных средах (воздух, вода, пар). |
20Х13, 30Х13, 40Х13 |
мартенситные |
|
12Х17, 15Х25Т, 15Х28 |
ферритные |
К этому типу относятся низкоуглеродистые высокохромистые стали, обладающие повышенной коррозионной стойкостью. Эксплуатируются в условиях работы в растворах азотной и фосфорной кислот. |
12Х18Н10Т |
аустенитные |
Применяют для деталей, работающих в морской воде, органических и азотной кислотах, слабых щелочах. |
10Х17Н13М3Т |
Используют для деталей, работающих в фосфорной, уксусной и молочной кислотах. |
Хромистые нержавеющие стали обычно содержат 0,08…0,45% углерода и 12,5…18% хрома.
Стали с 13% Cr обладают лучшей стойкостью против коррозии только при условии, что все содержание Cr в стали приходится на долю твердого раствора. В этом случае он образует на поверхности изделия плотную защитную оксидную пленку типа Cr2O3. Увеличение содержания углерода, приводящее к образованию карбидов, создает двухфазную структуру, уменьшая количество хрома в твердом растворе, и поэтому понижает коррозионную стойкость стали.
Хромистые коррозионностойкие стали используют для изготовления компрессоров, лопаток турбин, клапанов, арматуры нефтеустановок и аппаратов, а стали 30Х13 и 40Х13 — для режущего и измерительного инструмента, деталей карбюраторов, пружин и других деталей, работающих при температуре до 400 °С. Сталь марки 40Х13 широко применяется для изготовления хирургического и бытового инструмента.
Детали, изготовленные из этих сталей, подвергаются закалке и низкому, среднему и высокому отпуску в зависимости от марки и требуемых свойств.
Хромоникелевые аустенитные коррозионностойкие стали:
Хромоникелевые стали обладают повышенными механическими и химическими свойствами.
Имеют в своем составе до 0,3% углерода, 18-25% хрома и 8-20% никеля: 12Х18Н9, 04Х18Н10, 12Х18Н10Т, 10Х17Н13М2Т.
Хромоникелевые стали в зависимости от структуры бывают следующих классов:
- аустенитный;
- аустенитно-ферритный;
- аустенитно-мартенситный.
аустенитный |
Стали этого класса способны работать при высоких температурах в агрессивных средах, в том числе в растворах кислот, обладают высокой обрабатываемостью давлением и свариваемостью. Благодаря своим специальным свойствам аустенитные стали широко применяются в химической промышленности и в строительстве.
Аустенитные стали имеют очень низкий порог хладноломкости и поэтому широко используются для конструкций, работающих при температурах до -200°С (сталь 07Х21Г7АН5). Для получения особо коррозионностойких материалов аустенитные стали дополнительно легируют медью или медью с молибденом (сталь 06Х23Н28МДТ). |
аустенитно-ферритный |
Стали этого класса кроме хрома и никеля в своем составе содержат титан и кремний. Отличаются более высокими антикоррозионными свойствами в активных средах, а также высокими технологическими свойствами. |
аустенитно-мартенситный |
Кроме хрома в своем составе имеют марганец, алюминий и никель. Аустенитно-мартенситные стали используются как коррозионностойкий конструкционный материал, способный работать в агрессивных рабочих средах. Эти стали имеют более высокие, по сравнению с аустенитными и аустенитно-ферритными сталями, механические и физико-химические свойства. |
2. Жаростойкие стали и сплавы.
Жаростойкость (окалиностойкость) – способность металла сопротивляться окислению в газовых средах (воздух, газы, водяной пар) в условиях повышенных температур.
При высоких температурах металлы окисляются кислородом, образуя оксидную пленку. Оксидные пленки железа, вольфрама и других элементов обладают низкими защитными свойствами, т.к. являются неплотнымии через них легко проникает кислород с образованием новых слоев окалины, которая растрескивается, становится пористой. Происходит окисление на еще большую глубину, и металл выгорает.
Железо образует оксиды трех видов: FeO, Fe3O4, Fe2O3. а) До температуры 560-600°С окалина состоит преимущественно из плотных оксидов Fe2O3 и Fe3O4. Слой окалины на поверхности изделия затрудняет диффузию атомов кислорода к металлу и, соответственно, скорость окисления небольшая. б) При температуре выше 570-600°С происходит растрескивание плотной оксидной пленки и под ними образуется быстро растущий рыхлый слой FeOс низкой прочностью. Рыхлые оксиды мало препятствуют доступу кислорода к поверхности металла, что приводит к интенсивному окислению, которое классифицируют как химическую коррозию. |
|
Жаростойкость стали повышают легированием хромом, алюминием, кремнием и никелем, которые образуют на поверхности металла плотные оксидные пленки (FeO*Cr2O3, Cr2O3, FeO*Al2O3, Al2O3, 2FeO*SiO2),не разрушающиеся при высоких температурах и, следовательно, защищающими металл от дальнейшего разрушения.
Жаростойкость определяется, прежде всего, количеством легирующих элементов и мало связана со структурой стали.
При равном содержании хрома, температура образования окалины Ток повышается на 100-150°С при добавлении кремния и алюминия.
Содержание хрома в жаростойких сталях составляет 5-28%, кремния 2-3%, алюминия 5-6%.
Различают 2 основные группы жаростойких сталей:
- Высокохромистые стали с ферритной структурой: 08Х17Т, 15Х25Т, 15Х28, 05Х25Ю5 и др.
- Хромоникелевые стали с аустенитной структурой: 08Х18Н9Т, 20Х23Н18, 20Х25Н20С2 и др.
Жаростойкость некоторых сталей:
Марка |
Жаростойкость |
12Х13 |
700°С |
15Х6СЮ |
800°С |
08Х17Т |
900°С |
Сплавы на никелевой основе с Cr и Al обладают более высокой жаростойкостью |
|
ХН70Ю (26-29% Cr и 2,8-3,5% Al) |
1200°С |
3. Жаропрочные стали и сплавы.
Жаропрочность – свойство металла сопротивляться пластической деформации и разрушению при длительном воздействии нагрузки при повышенных температурах > 0,3Тпл.
Факторами, способствующими жаропрочности, являются:
- высокая температура плавления основного металла;
- наличие в сплаве твердого раствора и мелкодисперсных упрочняющих фаз;
- пластическая деформация, вызывающая наклеп;
- высокая температура рекристаллизации;
- легирование: элементы, повышающие жаропрочность: Mo, W, V, Nb, Ti, Co, Al, Ca, Ni.
- термическая и термомеханическая обработка для получения однородной структуры с дисперсными частицами карбидов, интерметаллидов и других частиц;
- введение в жаропрочные стали бора, церия, ниобия, циркония (в десятых, сотых и даже тысячных долях).
Наибольшая жаропрочность достигается при аустенитной структуре стали.
Оптимальная структура жаропрочных сталей – твердый раствор, упрочненный дисперсными частицами вторых фаз.
Марка стали |
Класс стали |
Режим термообработки |
Структура после термообработки |
Жаропрочность при Т,°С |
12ХМ |
Перлитный |
Нормализация 910°С, отпуск 670°С |
Легир.Феррит+карбиды |
540°С |
40Х10С2М |
Мартенситный |
Закалка 1030°С, масло, отпуск 720°С |
Легир.Сорбит+ карбиды |
650°С |
12Х18Н10Т |
Аустенитный |
Закалка 1100°С, вода, отпуск 700°С |
Легир.Аустенит |
700°С |
45Х14Н14В2М |
Аустенитный с карбидным упрочнением |
Закалка 1150°С, вода, старение 750°С ( в теч.5ч) |
Легир.Аустенит + карбиды |
650°С |
09Х14Н19В2БР |
Аустенитный с интерметаллидным упрочнением |
Закалка 1140°С, воздух, старение 700°С ( в теч.16ч) |
Легир. Аустенит + интреметаллиды |
700°С |
Жаропрочные стали подразделяются на 2 группы:
- теплоустойчивые стали: углеродистые, низколегированные, хромистые
- жаропрочные аустенитные стали: гомогенные (однофазные) стали, стали с карбидным упрочнением, стали с интерметаллидным упрочнением.
Группа |
Вид |
|
1. Теплоустойчивые стали |
углеродистые |
12К, 15К, 20К, 22К – применяют до 450°С. Буква К означает «котельная», цифры – среднее содержание углерода в сотых долях процента.
|
низколегированные |
12Х1МФ, 15Х1М1Ф |
|
хромистые |
- стали с 10-12% Cr, дополнительно легированные молибденом, вольфрамом, ванадием и ниобием: 15Х11МФ, 18Х12ВМФБР. Применяются до 550-620°С.
- стали с 5-10% Cr, дополнительно легированные кремнием (сильхромы): 40Х9С2, 40Х10С2М. Эти стали обладают повышенной жаростойкостью и применяются при длительной эксплуатации до 500-600°С. |
|
2.Жаропрочные аустенитные стали |
с карбидным упрочнением |
Эти стали предназначены для работы при 650-750°С и высоких напряжениях: 45Х14Н14В2М, 31Х19Н9МВБТ, 37Х12Н8Г8МФБ, 40Х15Н7Г7Ф2МС |
с интерметаллидным упрочнением |
Такие стали предназначены для работы при 550-750°С. 10Х11Н20Т3Р (ЭИ696), 10Х12Н22Т3МР (ЭП33), ХН35ВТ (ЭИ612), ХН35ВТЮ (ЭИ787) |
Жаропрочные легированные стали в зависимости от применения подразделяются на котельные, клапанные, котлотурбинные, для реактивной техники.
Применяются для производства различных деталей и конструкций: клапанов машинных двигателей, труб паро- и газопроводов, аппаратов и котлов сверхвысокого давления, крепежных деталей, лопаток паровых и газовых турбин и др.
4. Криогенные стали
Криогенные стали и сплавы по химическому составу являются низкоуглеродистыми (0,1% С) и высоколегированными (Cr, Ni, Mn и др.) сталями аустенитного класса.
Основными свойствами этих сталей являются пластичность и вязкость, которые с понижением температуры (от +20 до -196°С) либо не меняются, либо мало уменьшаются, т.е. не происходит резкого уменьшения вязкости, характерного при хладноломкости. Криогенные стали классифицируют по температуре эксплуатации в диапазоне от -196 до -296°С и используют для изготовления деталей криогенного оборудования.
Марка |
Применение |
03Х13Н9Д2ТМ |
для изделий, эксплуатируемых при температурах от +20 до -253°С |
03Х17Н14М3 сталь аустенитного класса |
сварные конструкции, работающие в средах повышенной агрессивности при температурах до -196°С |
03Х19Г10Н7М2 |
для изготовления сварных изделий, эксплуатируемых при температурах от 0 до -253°С |
03Х20Н16АГ6 |
для изготовления сварных крупногабаритных емкостей и резервуаров, находящихся под давлением при температурах от 20 до -26°С |