Раскатные кольца
Компания Апгрейд специализируется на поставке кованых раскатных колец (поковка кольцо, поковка с отверстием, кольцо цельнокатаное) из углеродистых, легированных, нержавеющих и жаропрочных сталей и сплавов.
Изготавливаем кольца со следующими характеристиками:Отправить запрос
Характеристики | Значения |
Стандарты | ГОСТ 8479-70, ГОСТ 25054-81, ОСТ 108.109.01-92. ОСТ 108.030.113-87, ОСТ 1.90074-72, СТ ЦКБА. |
Габариты |
Внешний диаметр: до 2500 мм Внутренний диаметр: до 2200 мм, Высота: до 500 мм. |
Вес | до 3000 кг |
Сроки изготовления | 14 - 25 дней |
Группа кованых колец согласно ГОСТ 8479-70 | I, II, III, IV, V |
По требованию изготавливаем раскатные кольца других типоразмеров по индивидуальным чертежам заказчика (Техническому заданию)
Доставка: по всей России.
Фотогалерея продукции
Марочный ассортимент поставляемой продукции
Компания Апгрейд поставляет стальные поковки следующих марок:
Виды конструкционной стали |
Марки сталей |
Сталь конструкционная легированная |
12ХН3А, 12Х2Н4А, 12Х2НВФА, 15Х, 15ХМ, 18ХГТ, 18Х2Н4МА, 18Х2Н4ВА, 20Х, 20ХН, 20ХН3А, 20Х2Н4А, 25ХГТ, 30Х, 30ХГСА, 30ХГТ, 30ХГСН2А, 34ХН1М, 35ХГСА, 38ХМ, 38ХА, 38ХМА, 38ХС, 38Х2Н2МА, 38Х2Н2ВА, 38ХН3МФА, 40Г2, 40Х, 40ХН, 40ХН2МА, 40Х2Н2ВА, 40Х2Н2МА, 40ХН2ВА, 40ХФА, 45ХН2МФА, 10Г2, 07Х3ГНМЮА, 12ХН, 19ХГН, 12ХН2, 15Г, 15ХГН2ТА, 15ХФ, 18ХГ, 20Г, 13ХФА, 25ХСНВФА, 28Х3СНМВФА, 16Х3НВФМБ, 35Х, 38ХН3МА, 30Х2НВА, 30Х3МФ, 30ХН2МА, 30ХН2МФА, 30ХН3А, 30ХРА, 34ХН1МА, 34ХН3МА, 35Г2, 36Г2С, 38ХГМ, 38ХГН, 38ХН3ВА, 40ХГНМ, 40ХМФА, 45Г, 45Х, 45ХН, 50Г, 50Х, 50ХН, 38ХН3А, 35Х3НМ |
Сталь конструкционная углеродистая качественная |
Ст. 10, Ст. 15, Ст. 20, 20К, Ст. 35, Ст. 45, Ст. 50, 25ХГМ, 25ХГСА, 25Х2Н4МА, 30Г, 20ХГНР, 20ХН2М, 20ХГСА, 20ХН2МА, 25ГС, 25Х2Н4ВА, 20ХГНМ, 40ХН2СВА, 07Х21Г7АН5, Ст. 25, Ст. 30, Ст. 40, Ст. 55, Ст. 60 |
Сталь конструкционная рессорно – пружинная |
50ХФА, 60С2А, 65Г, 55С2А, 60Г, 60С2, 60С2ХА, 60С2ХФА, 65С2ВА, 70Г, Ст. 65, Ст. 70 |
Сталь конструкционная для сварных конструкций |
09Г2С, 10ХСНД, 15ХСНД, 17Г1С, 17ГС |
Сталь конструкционная подшипниковая |
ШХ15, 8Х4В9Ф2, ШХ15СГ, ШХ20СГ |
Сталь конструкционная повышенной обрабатываемости |
А12, АС14 |
Сталь конструкционная углеродистая обыкновенного качества |
Ст. 3, Ст. 5 |
Виды инструментальной стали |
Марки сталей |
Инструментальная углеродистая |
У7, У7А, У8, У8А, У8Г, У9, У9А, У10, У10А, У11, У11А, У12, У12А, У13 |
Инструментальная легированная |
ХВГ, ХВСГ, 3Х2МНФ, 4ХС, 4ХНМФС, 5ХНВ, 5ХНВС, 5ХВ2СФ, 6Х3МФС, 6Х4М2ФС, 7ХФ, 8ХФ, 9Х1, 9ХФ, 9ХС, 9Г2Ф, 9ХВГ, 9Х5ВФ, 11ХФ, 12Х1 |
Инструментальная валковая |
45ХНМ, 60ХН, 75ХСМФ, 9Х2, 55Х, 60ХСМФ, 7Х2СМФ, 9Х2МФ, 60Х2СМФ, 75ХМ, 90ХМФ, 60ХГ, 75ХМФ, 90ХФ |
Инструментальная штамповая |
3Х3М3Ф, 4Х3ВМФ, 4Х5МФС, 6ХВ2С, 7ХГ2ВМ, Х12, Х12МФ, 4Х4МФС, 5ХВ2С, 6ХВГ, Х12ВМ, Х12Ф1, 3Х2В8Ф, 4Х2В2ФС, 5ХГМ, 6ХС, 8Х3, Х12ВМФ, Х6ВФ, 4Х5МФ1С, 5ХНМ, 7Х3, Х12М, 5Х2МНФ, 4Х5В2ФС, |
Инструментальная быстрорежущая |
Р2М5, Р6М3, Р6М5, Р6АМ5, Р6М5К5, Р6АМ5Ф3, Р6М5Ф3, Р9, Р9К5, Р9Ф5, Р9К10, Р18 |
Виды жаропрочной стали |
Марки сталей и сплавов |
Жаропрочная низколегированная |
12ХМ, 12Х1МФ, 15Х1МФ, 15Х5, 15Х5ВФ, 15Х5М, 15ХМ, 15Х2М2ФБС |
Жаропрочная высоколегированная |
08Х16Н11М3, 08Х16Н13М2Б, 08Х21Н6М2Т, 09Х14Н16Б, 10Х11Н20Т2Р, 10Х11Н20Т3Р, 10Х23Н18, 12Х14Н14В2М, 13Х11Н2В2МФ, 16Х11Н2В2МФ, 20Х20Н14С2, 20Х23Н13, 20Х23Н18, 45Х14Н14В2М |
Жаропрочная релаксационностойкая |
20Х1М1Ф1БР, 20Х1М1Ф1ТР, 25Х1М1Ф, 25Х1МФ, 25Х2М1Ф, 30ХМ, 30ХМА, 38Х2МЮА |
Жаропрочный сплав |
ХН32Т, ХН35ВТ, ХН35ВТЮ ХН38ВТ, ХН45Ю, ХН55МВЮ, ХН60ВТ, ХН70Ю, ХН77ТЮР, ХН78Т |
Виды коррозионно-стойкой стали |
Марки сталей и сплавов |
Коррозионно-стойкая |
03ХН28МДТ, 06ХН28МТ, 06ХН28МДТ, ХН65МВ |
Коррозионно-стойкая качественная |
03Х18Н11, 07Х16Н4Б, 07Х16Н6, 08Х17Н13М2Т, 08Х17Н6Т, 08Х18Н12Т, 08Х22Н6Т, 09Х16Н4Б, 10Х17Н13М2Т, 10Х17Н13М3Т, 20Х17Н2, 25Х13Н2, 98Х18 |
Коррозионно- стойкая жаропрочная |
08Х13, 08Х17Т, 08Х18Н10, 08Х18Н10Т, 10Х18Н10Т, 12Х18Н12Т, 12Х18Н9, 12Х18Н10Т, 14Х17Н2, 15Х25Т, 20Х13, 30Х13, 40Х13 |
Виды испытаний
В соответствии с ГОСТ 8479-90 поставляем раскатные кольца I, II, III, IV, V групп в зависимости от объема обязательных испытаний:
Группа поковок |
Виды испытаний |
Условия комплектности партии |
Сдаточные характеристики |
Документы |
I |
Без испытаний |
Поковки одной или разных марок стали |
- |
Хим. анализ |
II |
Определение твердости |
Поковки одной марки стали, совместно прошедшие термическую обработку |
Твердость |
Сертификат |
III |
Определение твердости |
Поковки одной марки стали, прошедшие термическую обработку по одинаковому режиму |
Твердость |
Сертификат |
IV |
- Испытание на растяжение, - Определение твердости и ударной вязкости |
Поковки одной плавки стали, совместно прошедшие термическую обработку |
Предел текучести Относительное сужение Ударная вязкость |
Сертификат, паспорт |
V |
- Испытание на растяжение, - Определение твердости и ударной вязкости |
Принимается индивидуально каждая поковка |
Предел текучести Относительное сужение Ударная вязкость |
Сертификат, паспорт |
Справочная информация
Процесс изготовления раскатных колец
Поковки цельнокатаных колец изготавливают на прессе по типовому алгоритму (без проведения процесса протяжки прибыльной части слитка под патрон), включающему в себя следующие этапы:
№ |
Схематичное изображение процесса |
Этап изготовления раскатных колец |
I вынос |
||
1 |
|
В первом выносе слиток кладут на нижнюю плоскую плиту вдоль верхнего плоского слитка и одновременно двумя топорами отрубают заготовку, удаляя в отход прибыльную и донную части слитка |
II вынос |
||
2 |
|
После отрубки слиток обкатывают, перемещая стол пресса. |
3 |
|
Далее, произведя кантовку заготовки на торец, осаживают ее и пробивают (или прошивают) отверстие. |
4 |
|
Затем после подогрева выполняют раскатку заготовки на оправке до размеров поковки. Раскатка сопровождается уширением, величину которого заранее учитывают. |
По этому алгоритму изготовляют раскатные кольца, предназначенных для производства деталей, у которых:
где D — внешний диаметр; d — внутренний диаметр; Н — высота.
Для изготовления поковок с отверстием, предназначенных для производства деталей, габариты которых отвечают условиям:
используют следующий алгоритм:
- Отрубка;
- Обкатка;
- Осадка, пробивка отверстия;
- Протяжка на оправке;
- Раскатка.
Если детали короткие, то их обычно изготовляют в виде одной поковки, которую потом разрезают на кольца необходимых размеров.
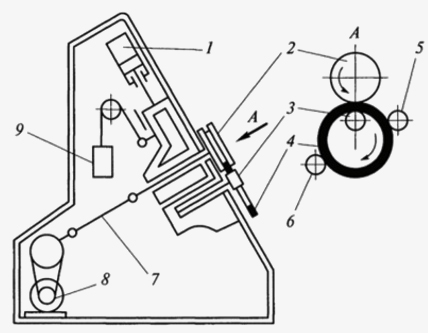
- Гидравлический цилиндр;
- Нажимной валок (Бандаж);
- Раскатной валок
- Исходная заготовка;
- Направляющий ролик;
- Контрольный ролик;
- Карданный вал;
- Электродвигатель;
- Груз;
Рис. 1. Схема работы раскатной машины:
Исходную заготовку 4 устанавливают отверстием на раскатной валок 3, который свободно вращается в подшипниках. Нажимной валок (бандаж) 2, приводимый во вращение от электродвигателя 8, через карданный вал 7 с помощью гидравлического цилиндра 1 нажимает на заготовку и, вращая, обжимает ее. Направляющий ролик 5 служит для формирования правильного круга, а контрольный ролик 6 фиксирует достижение заданного размера. Обратный ход бандажа осуществляет груз 9.
Виды раскатки
Радиальная раскатка кольцевых поковок
При данном способе происходит одновременное увеличение диаметра отверстия и внешнего диаметра заготовки благодаря уменьшению толщины стенки.
Радиальная раскатка позволяет изготовлять раскатные кольца (поковки с отверстием) следующих габаритов:
- Диаметр от 50 до 7000 мм;
- Ширина стенки от 5 до 1200 мм;
- Масса от нескольких десятков граммов до 12,5 т.
Данный вид раскатки кольцевых поковок может быть выполнен в горячем, полугорячем и холодном состояниях.
В зависимости от способа формоизменения радиальная раскатка бывает:
- открытая;
- полуоткрытая;
- закрытая.
Схемы радиальной раскатки |
Описание |
Изготовление раскатных колец открытым способом
Обозначения на схеме:
|
Этот способ является наиболее распространенным. Процесс формоизменения стенки заготовки происходит между двумя инструментами.
|
Изготовление раскатных колец полуоткрытым способом
|
Полуоткрытый способ раскатки позволяет получить более точную высоту кольца с отверстием за счет добавленения двух пар свободно вращающихся роликов (неприводных), которые обжимают торцы поковки в процессе ее раскатки. Данный способ раскатки имеет ограниченное применение в отечественной промышленности.
|
Изготовление раскатных колец закрытым способом
|
Закрытая раскатка, получившая малое применение, отличается тем, что зона деформации закрыта со всех четырех сторон. В отличие от предыдущих способов формоизменения заготовки осуществляется прокаткой между наружным полым валком 7 и внутренним валком 6. Процесс деформации выполняется до тех пор, пока толщина стенки заготовки 1 не достигнет заданной, а внешний диаметр не примет размера диаметра отверстия полого валка. |
Кольцевая раскатка
Кольцевая раскатка относится к ресурсосберегающим технологиям, т.к. способствует повышению производительности и сокращению расхода металла.
В зависимости от габаритов исходной заготовки, способы выполнения кольцевой раскатки могут быть следующими:
- Небольшие заготовкивесом в несколько десятков килограммов раскатывают на универсальных токарных станках.
- Кольцевые поковки средней габаритностивесом до нескольких сотен килограммов раскатывают на специальной оправке на гидравлических прессах или молотах по схеме (рис. 2).
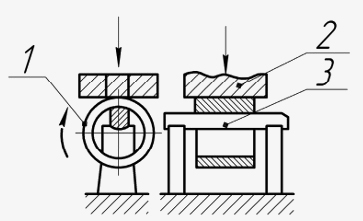
- Раскатываемое кольцо;
- Боёк пресса или молота;
- Оправка.
-
Крупногабаритные кольцевыепоковки весом в несколько тонн изготавливать ковкой на молотах или прессах не целесообразно по причине:
- значительного перерасхода металла из-за больших размерных припусков, которые приходится делать т.к. полученная такой раскаткой заготовка имеет форму многогранника;
- повышения трудоемкости при мех. обработке заготовки;
- повышения износа режущего инструмента.
Производство раскатных колец методом кольцевой раскатки позволяет:
- уменьшить расход металла до 30%;
- снизить трудоемкость процесса ковки до 25%;
- уменьшить трудоемкость процесса механической обработки в 2 раза;
- уменьшить износ режущего инструмента;
- увеличить производительность благодаря сокращению цикла производства крупногабаритных поковок колец и высвобождению производственных мощностей предприятия.
Кольцевая раскатка включает следующие этапы:
- Отрубка донной части заготовки;
- Обкатка;
- Осадка заготовки, прошивка;
- Раскатка заготовок на оправке до размеров, позволяющих осуществление транспортировки;
- Термическая обработка;
- Раскатка заготовки (с параллельной правкой в процессе раскатки) на раскатном стане до требуемых размеров;
- Окончательная механическая обработка.
Кольцевая раскатка выполняется на раскатных станах горизонтального и вертикального типа (рис. 3).
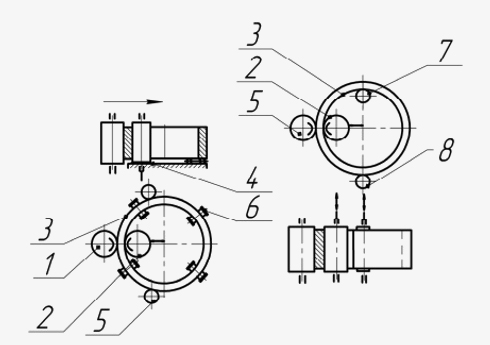
- Наружный раскатной валок;
- Внутренний раскатной валок;
- Раскатываемая заготовка;
- Опорный стол;
- Центрирующие (опорные) ролики;;
- Радиальные салазки
- Верхний опорный валок;
- Нижний опорный валок.
Главные различия станов заключаются в расположении осей наружного 1 и внутреннего 2 валков заготовки 3:
- стан вертикального типа имеет вертикальном расположении осей валков параллельно оси заготовки;
- стан горизонтального (радиального) типа имеет горизонтальное положение осей валков и заготовки.
Преимущества раскатных колец
Изготовление кованых колец методом раскатки имеет следующие преимущества:
- Возможность получения бесшовных колец;
- Более высокая точность размеров и формы благодаря сокращению припусков, напусков, допусков, разностенностни и овальности;
- Увеличение производительности при дальнейшей механической обработке раскатанных поковок.
Применение раскатных колец
Раскатные кольца применяют:
- В шарикоподшипниковой промышленности для изготовления корпусов, втулок подшипников;
- В авиадвигателестроении для изготовления деталей авиационных двигателей;
- В ядерной промышленности для изготовления деталей ядерных реакторов;
- Для изготовления фланцев, передаточных шестерен, оболочек сосудов высокого давления, канатных шкивов, кольцевых деталей, дисков, узлов опорно-поворотных устройств;
- В энергетической промышленности (в том числе для ветрогенераторов);
- В машиностроении при изготовлении спецтехники;
- В судостроении;
- В космической промышленности для изготовления деталей ракетной техники.
Свяжитесь с нами
Заказать изготовление раскатного кольца в компании Апгрейд или получить консультацию по продукции можно по телефону 7(495) 984-97-09, e-mail info@9hs.ru.