Процесс изготовления поковок
Подбор исходного
материала
Сырьем могут быть:
блюмы, слябы, слитки, сортовой
металлопрокат
Материал может быть:
- давальческим
- приобретенным
- собственного производства
Входной контроль
- химсостав
- способ выплавки
Виды стали по способам выплавки (ГОСТ 14959-2016):
Резка заготовки
для получения необходимых
габаритов и веса
Оборудование для резки металлических заготовок
пресс
и высоколегированной стали обычно
режут с помощью пил.
Для разделки катаного металла
применяют способы:
- резка на пресс-ножницах и в штампах на кривошипных прессах (основные способы разделки в кузнечных цехах с крупно- и среднесерийным характером производства),
- резка пилами и абразивами,
- ломка на хладноломах, газовая резка.
Нагрев заготовок
Время нагрева заготовок под
ковку для термообработки в
методических печах была
определена Ю. М. Чижиковым
формулой:
T нагр = K • D
Где Т нагр - время нахождения
заготовки при рекомендуемой
температуре, час;
D - диаметр или меньшая сторона
сечения нагреваемого тела, см;
К - коэффициент:
- для углеродистых сталей К=0,1÷0,15;
- для легированных
конструкционных К=0,15÷0,2; - для высоколегированных и
инструментальных К=0,3÷0,4.
Цель нагрева - повышение пластичности металла и снижения его сопротивления деформированию
Процесс нагрева металла должен обеспечивать:
- достаточно равномерный прогрев по сечению заготовки до требуемой температуры
- минимальное окисление и обезуглероживание поверхности
- сохранение целостности нагреваемого металла т. е. отсутствие микро- и макротрещин
От способа и режима нагрева зависят:
- качество и себестоимость поковок
- расход металла и топлива
- стойкость инструмента
Температурный интервал ковки - максимальная температура нагрева металла в печи и температура окончания ковки.
Выбор температурного интервала ковки зависит от:
- химического состава материала,
- структуры заготовки (литая или деформированная),
- скорости деформирования (молот или пресс),
- степени и вида деформации (дробная или единичная),
- вида операции ковки, (осадка, протяжка и т. д.),
- массы слитка.
Чем выше скорость нагрева (т. е. чем меньше его продолжительность), тем меньше окисление и обезуглероживание поверхности и тем экономичнее (рентабельнее) нагрев. Однако при чрезмерно быстром нагреве в металле могут возникать термические напряжения, которые могут привести к образованию микро- и макротрещин => к браку поковок.
Процесс ковки металла

Ковка – процесс деформации заготовки путем воздействия ударной нагрузки бойков молота или пресса.
Преимущества:
-
Экономичность (по сравнению со штамповкой)
На производстве ковку применяют только в мелкосерийном и единичном производстве (ручной или машинный метод).
Недостатки:
- низкая производительность (ковку применяют только в мелкосерийном и единичном производстве (ручной или машинный метод)
- больший расход металла: припуск под обработку поковки кованой практически в 2 раза больше, нежели у поковки полученной методом штамповки

Штамповка – процесс деформации заготовки под давлением; осуществляется в матрице штампа, форма которой полностью идентична изготовляемой поковке. Ударным элементом нагрузки - пуансон.
Виды штамповки:
- с предварительным нагревом исходной заготовки
- без нагрева
Преимущества:
- высокая производительность,
- меньший расход металла: припуск под обработку поковки штамповкой практически в 2 раза меньше, чем ковкой,
- на выходе поковка имеет более высокую точность размеров и малую шероховатость поверхностного слоя.
Недостатки:
- дорогостоящий процесс (применение штампов целесообразно только в массовом и серийном производстве, чтобы оправдать затраты)
Виды штамповки
Объемная штамповка - процесс изготовления поковок в штампах, когда течение металла в стороны при деформации ограничено поверхностями отдельных частей штампа
Открытая объемная штамповка
а, б, в - начальная, промежуточная и конечная стадия штамповки 1,
2 - нижняя и верхняя части штампа
3 - заготовка
4 - облойная канавка; 5 - магазин для облоя
6 - поковка на промежуточной стадии процесса
7 - готовая поковка
8 - облой
штамповка
Оборудование для штамповки
2 - выталкиватель
молот
гидравлический пресс
Предварительная
термообработка
проводится с целью снижения
/снятия остаточных напряжений,
возникающих в результате
динамического воздействия
молота или статического
воздействия пресса на металл

НОРМАЛИЗАЦИЯ (Нормализованный отжиг)
нагрев стали до аустенитного состояния, выдержка при
температуре нагрева и последующего ускоренного
охлаждения на воздухе.
Результат:
- перекристаллизация и измельчение зерна
- выравнивание хим.состава и свойств
- снятие внутренних остаточных напряжений
- повышение твердости и прочности
стали под нормализацию

ОТЖИГ
нагрев стали выше критических температур, выдержка
при температуре нагрева и последующего медленного
охлаждения (вместе с печью)
Результат:
- получение равновесной мелкозернистой структуры
- снятие внутренних напряжений в металле
- ↑пластичность и вязкость (↓ тв-ть и износостойкость)
- выведение флокенов (полости с газом) => достижение
требуемой чистоты металла - улучшение обрабатываемости заготовок давлением и
резанием
стали под отжиг
технологического процесса
в зависимости от требуемой
группы конечной поковки
(согласно ГОСТ 8479-70)
I-II группа
в дробеметном барабане
требованию заказчика
по требованию заказчика
определения твердости
без мех.обработки
- определение твердости
- определение твердости
(с мех.обработкой)
(без мех.обработки)
или I группы
(с мех.обработкой по
требованию заказчика)
без группы или I группы
(без мех.обработки)
Предварительная
механическая обработка
Обдирка, резка, правка,
зачистка…
Выбор способа
окончательной
термообработки
заготовки в зависимости от
назначения конечной детали

Закалка - является упрочняющей термообработкой, заключающейся в нагреве выше Т критич (доэвтектоидных сталей на 30-50С выше Ас3 (полная закалка), заэвтектоидных сталей на 30-50С выше Ас1 (неполная закалка), выдержке при этой Т и быстрое охлаждение со скоростью, превышающую критическую, в различных средах (вода, соляные водные растворы, техническое масло, инертные газы).
После закалки внутри стали возникают напряжения. Чтобы их снять закаленные изделия подвергают отпуску
Цель:
получение мартенситной структуры, обеспечивающей максимальную твердость, прочность и износоустойчивость
Результат:
↑ твердость и прочность (обеспечивается за счет получения структуры мартенсита)
↓ пластичность и предел на сжатие
↑ износостойкость
↑ хрупкость

Отпуск - заключительная термообработка, т.к. обеспечивает требуемые мех.св-ва стали.
Отпуск заключается в нагреве до Т ниже критической, выдержке при этой температуре и охлаждении на воздухе.
Цель:
- получение более равновесной структуры,
- снятие внутренних напряжений (температурных и структурных), возникающих при закалке.
Результат:
- ↑ ударная вязкость, предел упругости и пластичность
- ↓ тв-ти и внутренние напряжения
ЗАКАЛКА И НИЗКИЙ ОТПУСК
применяется для деталей машин, работающих в условиях изнашивания, высоких контактных нагрузок (детали подшипников качения, режущий, измерительный инструмент).
Микроструктура стали:
- для доэвтектоидной стали - мартенсит отпуска (полная закалка)
- для заэвтектоидной стали - мартенсит отпуска + цементит вторичный (неполная закалка).
Твердость - 60 HRC
ЗАКАЛКА И СРЕДНИЙ ОТПУСК
применяется для упругих элементов машин из высокоуглеродистых сталей (пружины, рессоры, мембраны).
Микроструктура стали:
троостит отпуска (обеспечивает высокий предел упругости, выносливости и релаксационной стойкости).
Твердость - 40 HRC
ПОЛНАЯ ЗАКАЛКА И ВЫСОКИЙ ОТПУСК
(термическое улучшение)
применяется для деталей машин из среднеуглеродистых сталей, испытывающих статические и динамические/циклические нагрузки (валы, оси, шатуны, крепежные детали).
Данная комбинация ТО создает наилучшее сочетание прочности и пластичности стали при повышенной ударной вязкости.
Микроструктура стали:
зернистый сорбит отпуска.
Твердость - 30 HRC
Очистка поковок от окалины
в дробеметном барабане
Проведение испытаний в
зависимости от группы
поковки согласно
ГОСТ 8479-70
определения твердости
без мех.обработки
определения твердости
без мех.обработки
или по требованию
заказчика
или по требованию
заказчика
ОТК
-
определение
твердости
(Поковки одной
марки стали,
прошедшие ТО по
одинак режиму)
ОТК
-
определение
твердости
(Поковки одной
марки стали,
прошедшие ТО по
одинак режиму)
ОТК
-
Испытание на
растяжение -
Определение ударной
вязкости -
Определение
твердости (Поковки
одной плавки стали,
совместно
прошедшие ТО)
ОТК
-
Определение
твердости (Поковки
одной плавки стали,
совместно
прошедшие ТО)
ОТК
-
Испытание на
растяжение -
Определение ударной
вязкости -
Определение
твердости (Принимается
индивидуально
каждая поковка)
(с мех.обработкой)
(без мех.обработки)
(с мех.обработкой)
(без мех.обработки)
(с мех.обработкой)
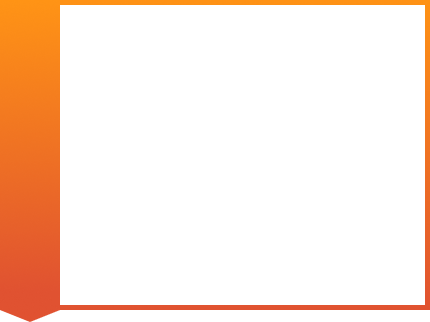
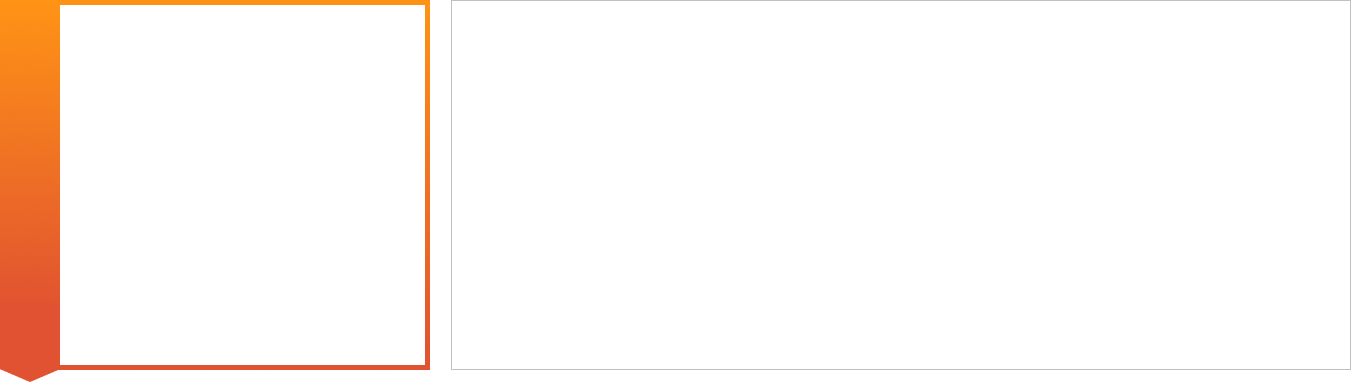
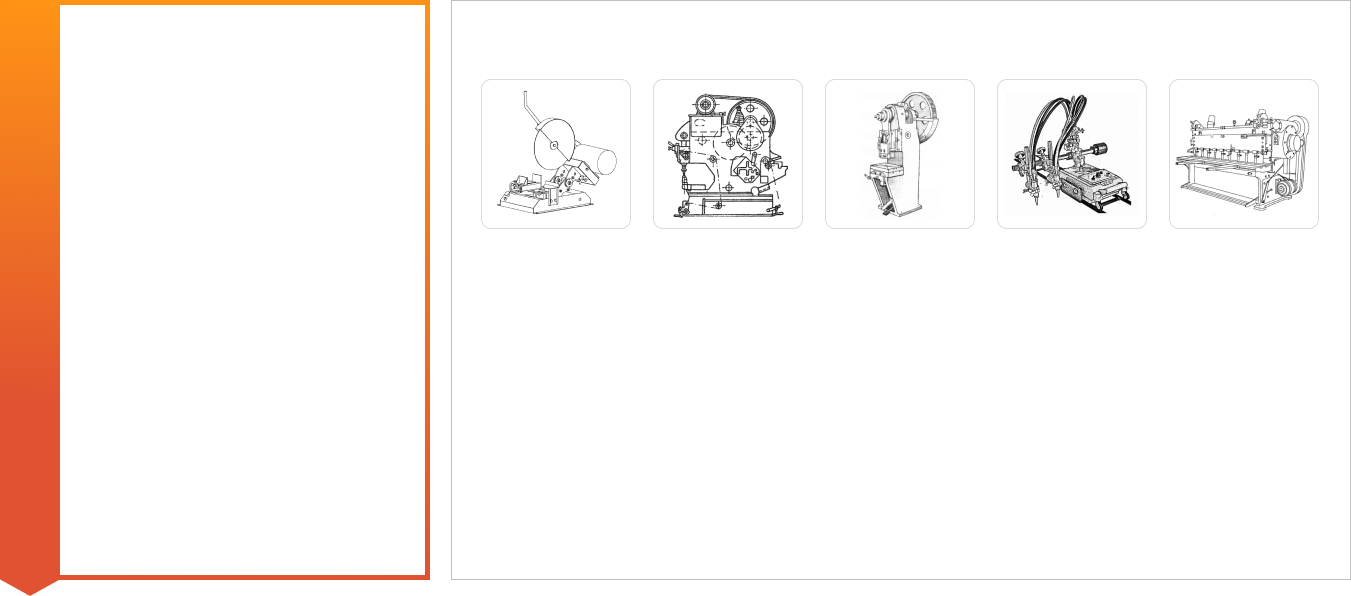
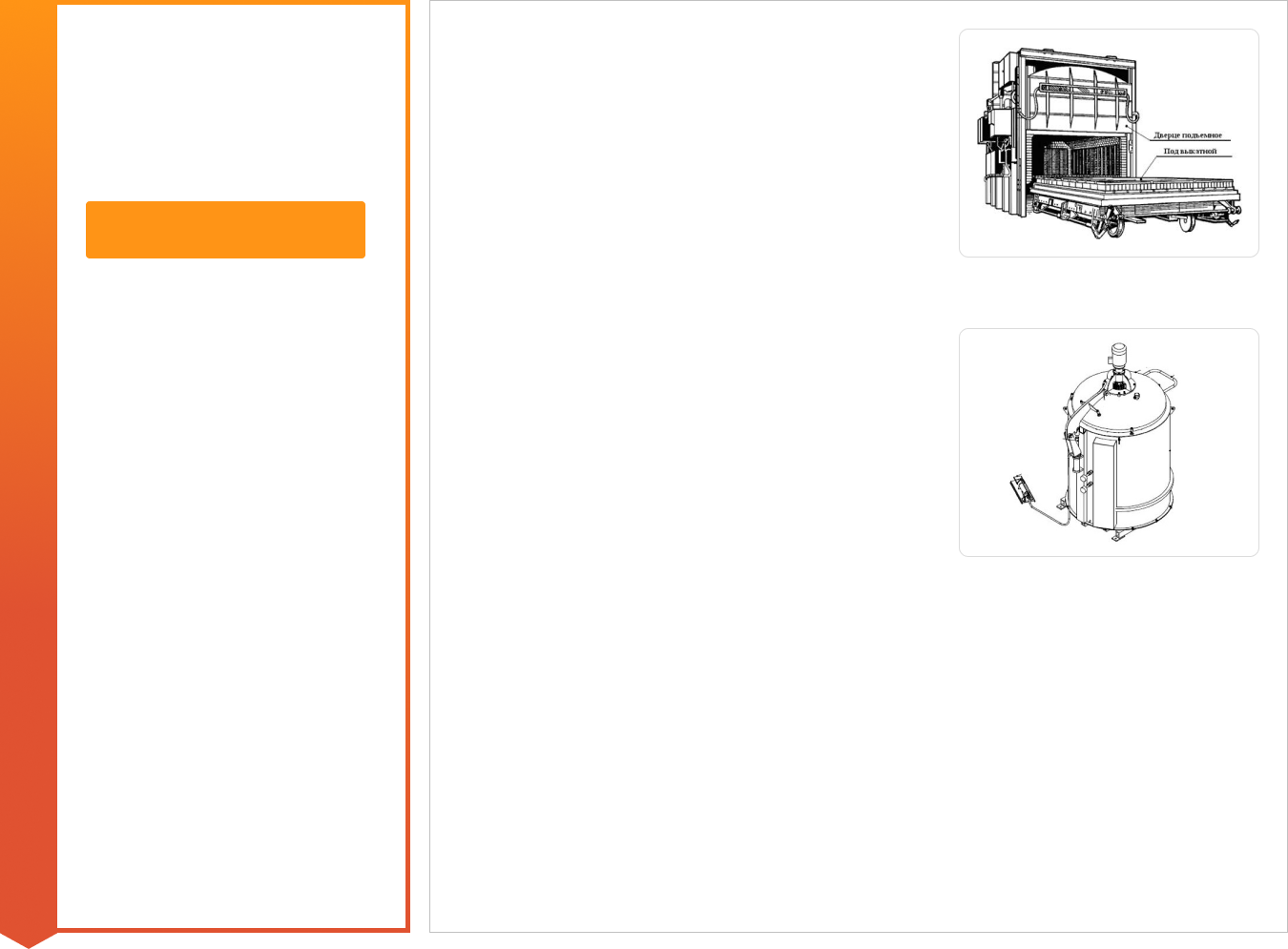
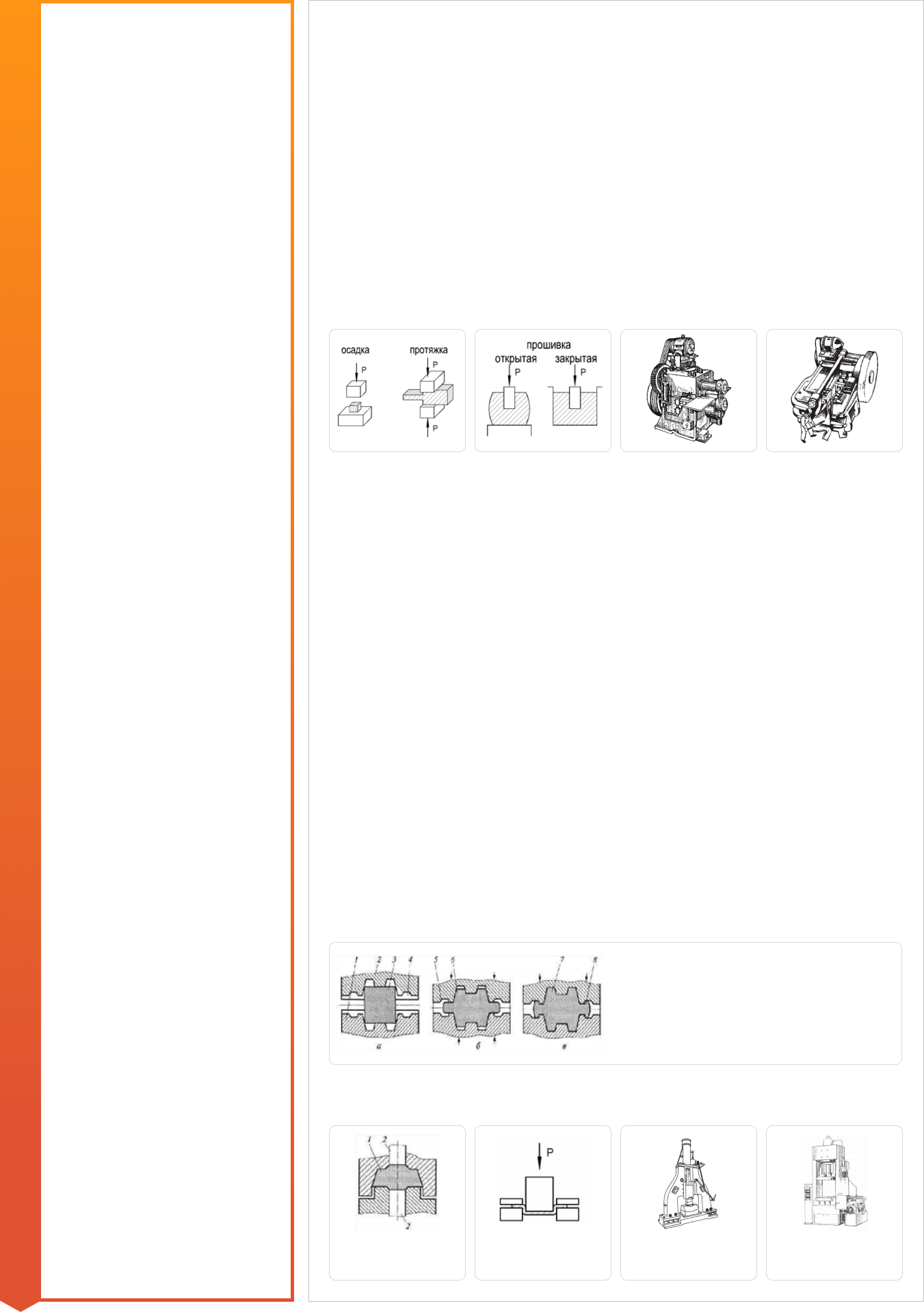
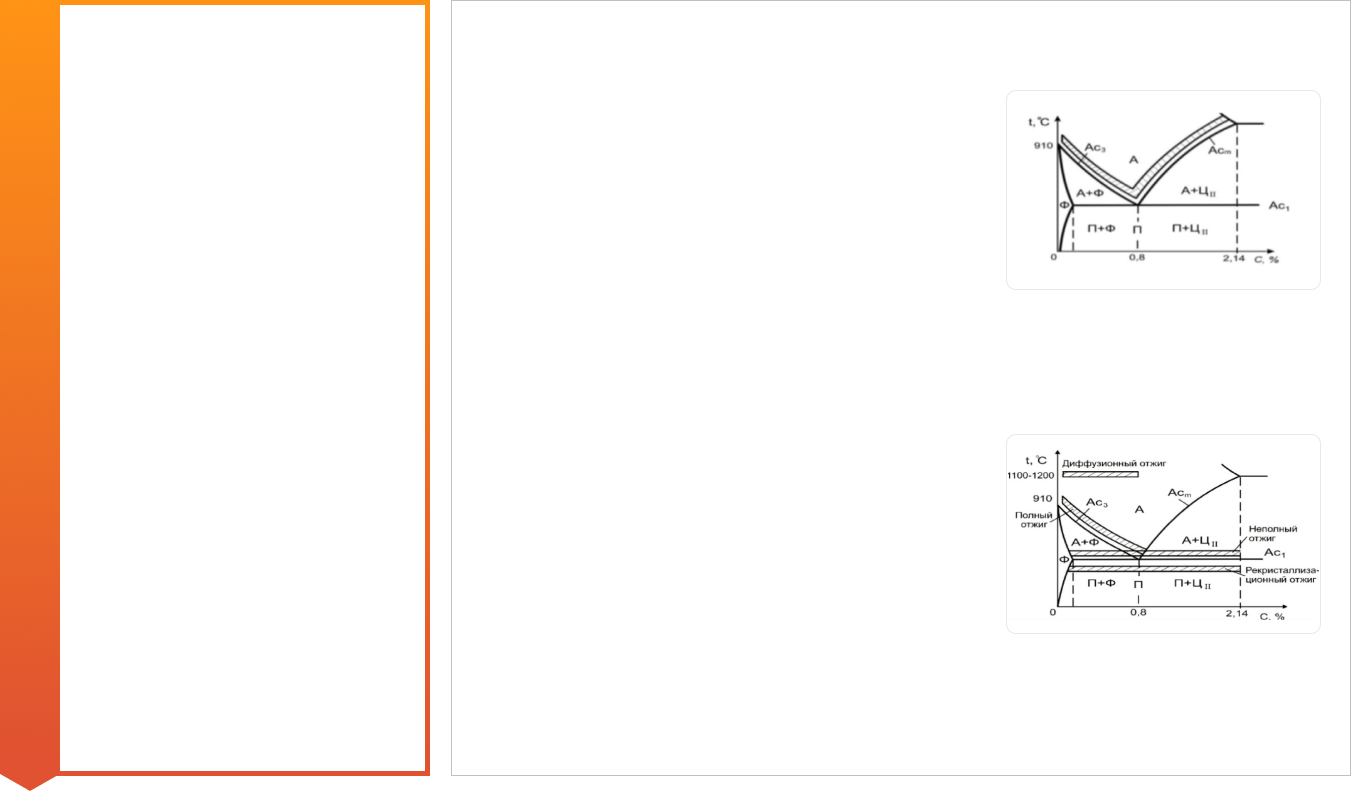
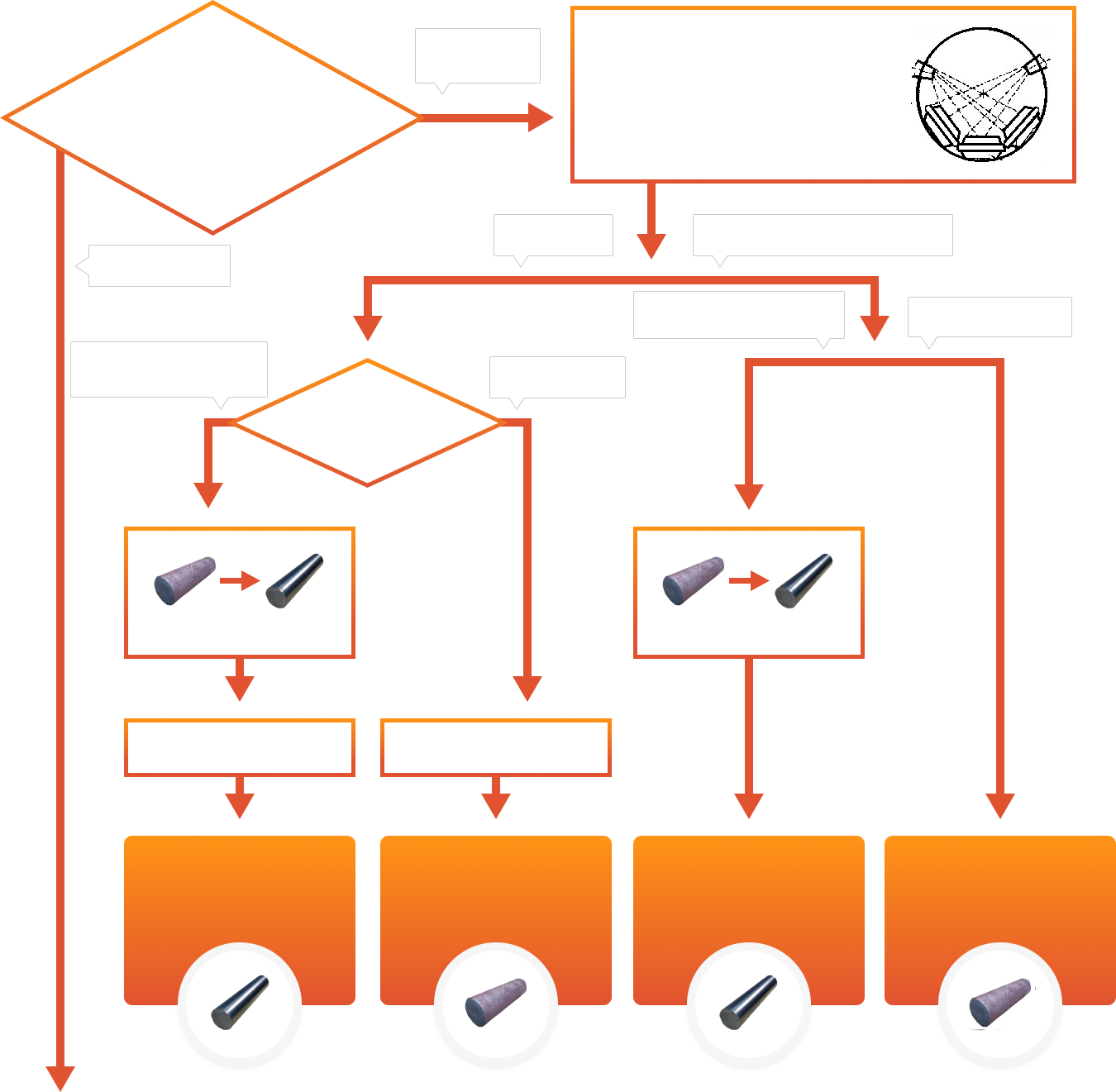
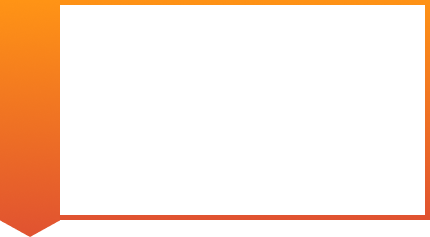
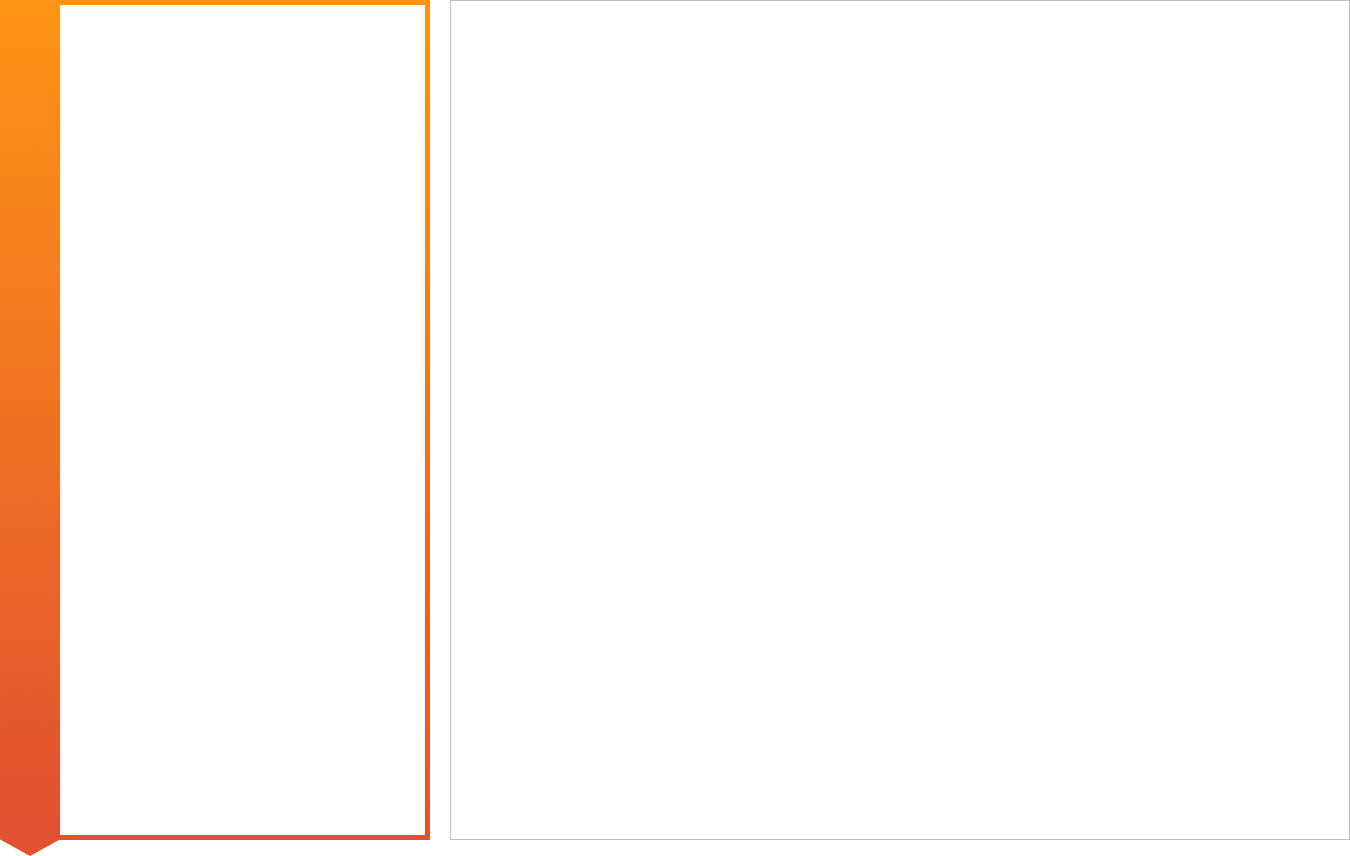
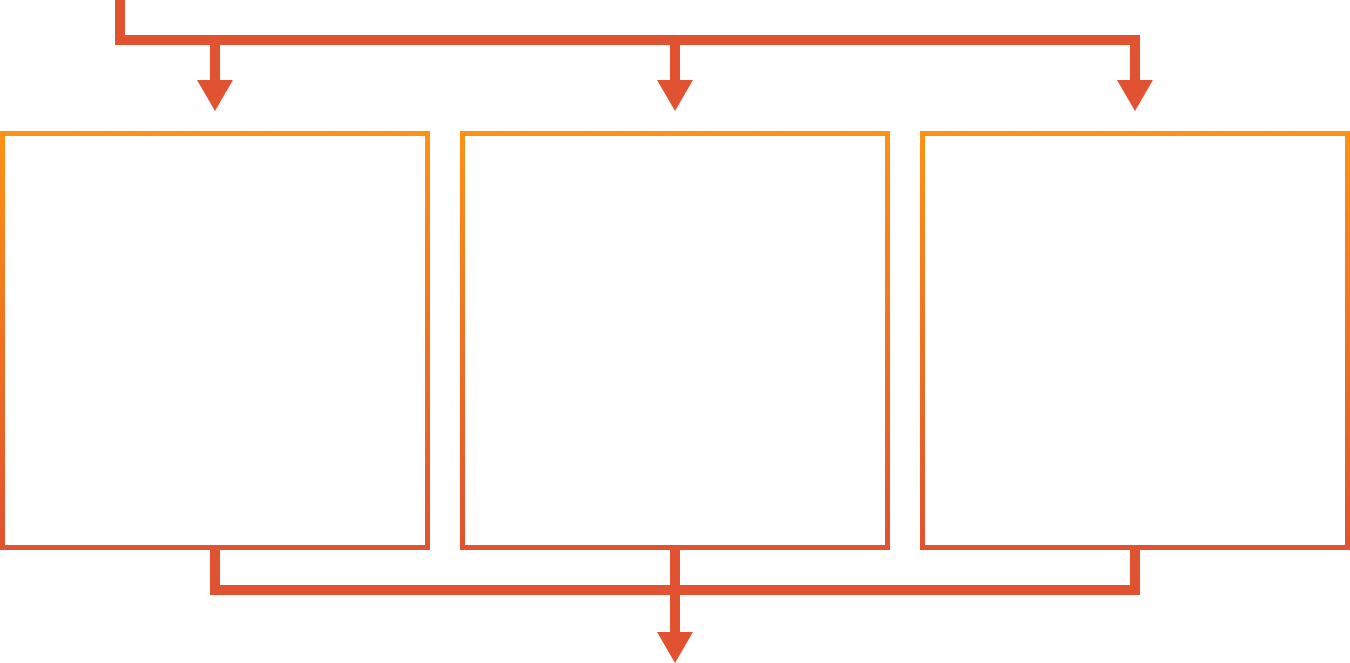
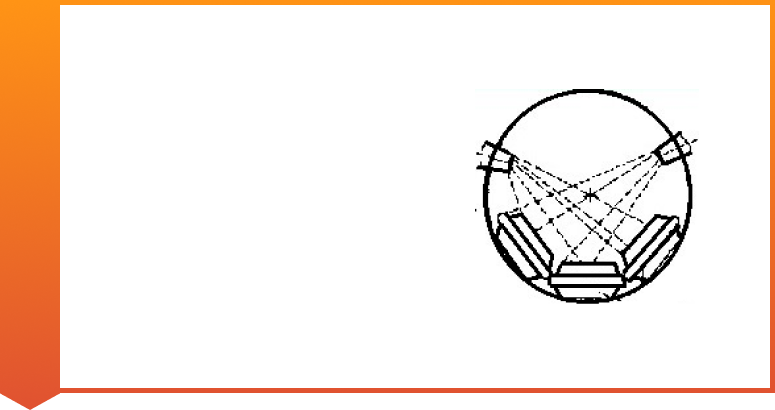
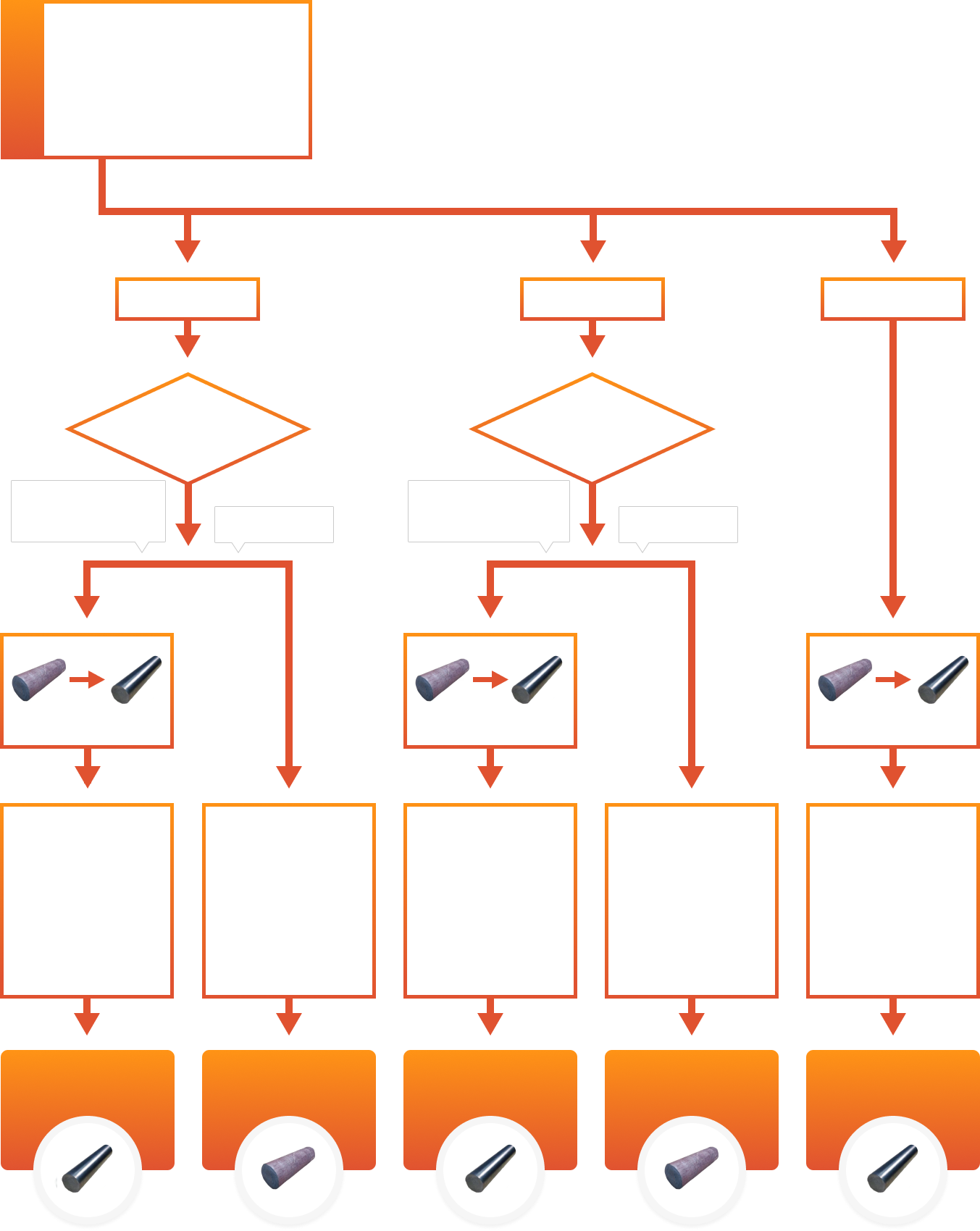