Поковки
Наши возможности
Компания Апгрейд специализируется на поставке поковок из конструкционных, инструментальных, нержавеющих и жаропрочных сталей и сплавов. Собственное производство и возможность кооперации с кузницами и металлургическими комбинатами позволяет нам оперативно решать комплексные задачи клиента и выполнять сложные заказы с широким диапазоном по габаритам, весу и марочному ассортименту.
На складе нашей организации всегда в наличии широкий ассортимент кованой продукции, изготовленной согласно соответствующим стандартам: ГОСТ 8479-70, ГОСТ 1133-71, ГОСТ 25054, ТУ 14-1-1530, ОСТ 108.030.113 и др.
Возможные варианты изготовления и поставки поковок:
Фотогаларея- молотовые и прессовые;
- поковки без механической обработки (вчерне);
- поковки с предварительной механической обработкой;
- поковки с чистовой механической обработкой (детали): валы (коленчатые, эксцентриковые), шестерни, фланцы, плунжера, корпуса;
- в отожжённом состоянии и с заданными механическими свойствами;
- с термической обработкой (отжиг, закалка, нормализация, отпуск);
- с контролем качества;
- с проведением ультразвукового контроля или без, возможны и другие виды контроля по требованию заказчика;
- с контролем механических свойств;
- с различными видами укова: уков за операцию или переход; уков за вынос (частный); уков за весь период ковки (общий).
Все поковки поставляются с сертификатом качества.
Технические характеристикиОтправить запрос
Наименование |
Вид |
Технические характеристики |
Поковка круглая |
![]() |
Dmax = 2000 мм. Lmax = 18000 мм. m = 80000 кг Сроки изготовления: до 120 дней |
|
|
|
Поковка прямоугольного сечения |
|
Hmax = 2000 мм Bmax = 2000 мм. Lmax = 18000 мм. m = 80000 кг. Сроки изготовления: до 120 дней |
|
|
|
Поковка вал |
|
Dmax = 1600 мм. Lmax = 8000 мм. m = 30000 кг. Сроки изготовления: до 120 дней |
|
|
|
Поковка кольцо |
|
Dmax = 4200 мм. Hmax = 2500 мм. m = 30000 кг. Сроки изготовления: до 120 дней |
По требованию заказчика поставляем поковки других типоразмеров. |
Мы являемся производством полного цикла, кузнечные слитки малой развесовки изготавливаем в электропечах и затем куем их на молоте или прессе. Это позволяет нам конкурировать по ценам, срокам и выполнять любые объемы и выплавлять практически любые марки стали.
Изготовление слитков открытой плавки, шлакового и вакуумнодугового переплавов:
- технологическая возможность изготовления стали по заданному химическому составу;
- обладающие минимальным уровнем газовых примесей и неметаллических включений;
- изготавливаем слитки малой, средней и большой развесовки 8 и 12-гранные.
- с высокой степенью однородности структуры слитка.
- все слитки проходят УЗК по ГОСТ 24507-80 гр. 4n
Слитки открытой выплавки
Тип слитка | Вес слитка, кг | Основные размеры слитка | |||||||||||||||
D1 | D2 | D3 | h | H | |||||||||||||
СЛИТОК 8 и 12-ГРАННЫЕ Вес: 1150 - 11300 кг Длина L: 1400 - 3370 мм |
1150 | 350 | 400 | 300 | 1080 | 1400 | |||||||||||
2950 | 430 | 542 | - | 1260 | 1780 | ||||||||||||
3200 | 580 | 640 | 550 | 1135 | 1360 | ||||||||||||
3360 | 450 | 570 | 374 | 1200 | 1740 | ||||||||||||
3800 | 640 | 730 | 600 | 1200 | 1525 | ||||||||||||
4500 | 606 | 706 | 560 | 1460 | 1888 | ||||||||||||
4500 | 606 | 706 | 560 | 1460 | 1910 | ||||||||||||
4900 | 606 | 706 | 560 | 1670 | 2090 | ||||||||||||
4750 | 709 | 792 | 560 | 1170 | 1630 | ||||||||||||
4800 | 450 | 648 | 540 | 1270 | 1918 | ||||||||||||
4800 | 670 | 740 | 640 | 1670 | 2045 | ||||||||||||
5200 | 720 | 760 | 680 | 1400 | 2080 | ||||||||||||
5300 | 760 | 900 | 700 | 1400 | 1875 | ||||||||||||
6400 | 750 | 800 | 700 | 1700 | 2150 | ||||||||||||
7000 | 598 | 748 | 434 | 1430 | 2063 | ||||||||||||
8300 | 604 | 816 | 560 | 1468 | 2146 | ||||||||||||
9400 | 800 | 870 | 720 | 2120 | 2820 | ||||||||||||
11300 | 820 | 910 | 730 | 2540 | 3370 |
Слитки электрошлакового переплава
Тип слитка | Вес слитка, кг | Основные размеры слитка | ||||||
D1 | D2 | D3 | h | H | ||||
СЛИТОК круглого сечения | 1150 | 350 | 300 | 400 | 1080 | 1400 |
Слитки вакуумнодугового переплава
Тип слитка | Вес слитка, кг | Основные размеры слитка | ||||||
D | H | |||||||
СЛИТОК круглого сечения | 40 | 100 | 560 | |||||
75 | 145 | 560 |
Участок термической обработки
Печь | Max Тнагр, °С | Габариты рабочего пространства, мм | Среда нагрева |
Электропечь шахтная СШЦМ | 950 | Ø1000 х 3000 | Атмосфера на основе углеродосодержащих газов (с автоматизированным модулем контроля состава) |
Шахтная закалочная печь ПШЗ 10.30/12и1 | 950 | Ø1000 х 3300 | Воздух (окислительная) |
Электропечь шахтная ПШО | 700 | Ø1000 х 2000 | Воздух (окислительная) |
Электропечь камерная ПКМ | 1250 | 600х800х400 | Воздух (окислительная) |
Электропечь камерная ПЛ-20 | 1050 | 420х240х185 | Воздух (окислительная) |
Название | Рабочая среда | Размеры |
Закалочная ванна ВЗ 15.100.15/0, |
водный раствор |
длина 10 000 мм ширина 1 500 мм высота 1 500мм Максимальная масса садки (с оснасткой) 6 000 кг. |
Профессиональная закалочная ванна ВШЗ 10.35/0,8п | водополимерная среда |
диаметр 1 000 мм высота 3 500 мм |
Закалочная ёмкость | вода | Ø2500х3000 мм |
Закалочная ёмкость | масло | Ø2500х4000 мм |
Фотогалерея кованой продукции
Фотогалерея производства
Фотогалерея испытаний продукции
Наши преимущества
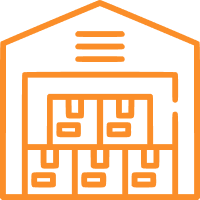
Постоянное складское наличие
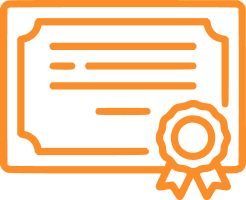
сертифицирована
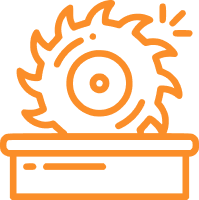
(резка, мех. обработка)

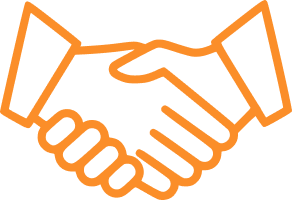
Персональный менеджер
Марочный ассортимент поставляемой продукции
Компания Апгрейд поставляет стальные поковки следующих марок:
Виды конструкционной стали |
Марки сталей |
Сталь конструкционная легированная |
12ХН3А, 12Х2Н4А, 12Х2НВФА, 15Х, 15ХМ, 18ХГТ, 18Х2Н4МА, 18Х2Н4ВА, 20Х, 20ХН, 20ХН3А, 20Х2Н4А, 25ХГТ, 30Х, 30ХГСА, 30ХГТ, 30ХГСН2А, 34ХН1М, 35ХГСА, 38ХМ, 38ХА, 38ХМА, 38ХС, 38Х2Н2МА, 38Х2Н2ВА, 38ХН3МФА, 40Г2, 40Х, 40ХН, 40ХН2МА, 40Х2Н2ВА, 40Х2Н2МА, 40ХН2ВА, 40ХФА, 45ХН2МФА, 10Г2, 07Х3ГНМЮА, 12ХН, 19ХГН, 12ХН2, 15Г, 15ХГН2ТА, 15ХФ, 18ХГ, 20Г, 13ХФА, 25ХСНВФА, 28Х3СНМВФА, 16Х3НВФМБ, 35Х, 38ХН3МА, 30Х2НВА, 30Х3МФ, 30ХН2МА, 30ХН2МФА, 30ХН3А, 30ХРА, 34ХН1МА, 34ХН3МА, 35Г2, 36Г2С, 38ХГМ, 38ХГН, 38ХН3ВА, 40ХГНМ, 40ХМФА, 45Г, 45Х, 45ХН, 50Г, 50Х, 50ХН, 38ХН3А, 35Х3НМ |
Сталь конструкционная углеродистая качественная |
Ст. 10, Ст. 15, Ст. 20, 20К, Ст. 35, Ст. 45, Ст. 50, 25ХГМ, 25ХГСА, 25Х2Н4МА, 30Г, 20ХГНР, 20ХН2М, 20ХГСА, 20ХН2МА, 25ГС, 25Х2Н4ВА, 20ХГНМ, 40ХН2СВА, 07Х21Г7АН5, Ст. 25, Ст. 30, Ст. 40, Ст. 55, Ст. 60 |
Сталь конструкционная рессорно – пружинная |
50ХФА, 60С2А, 65Г, 55С2А, 60Г, 60С2, 60С2ХА, 60С2ХФА, 65С2ВА, 70Г, Ст. 65, Ст. 70 |
Сталь конструкционная для сварных конструкций |
09Г2С, 10ХСНД, 15ХСНД, 17Г1С, 17ГС |
Сталь конструкционная подшипниковая |
ШХ15, 8Х4В9Ф2, ШХ15СГ, ШХ20СГ |
Сталь конструкционная повышенной обрабатываемости |
А12, АС14 |
Сталь конструкционная углеродистая обыкновенного качества |
Ст. 3, Ст. 5 |
Виды инструментальной стали |
Марки сталей |
Инструментальная углеродистая |
У7, У7А, У8, У8А, У8Г, У9, У9А, У10, У10А, У11, У11А, У12, У12А, У13 |
Инструментальная легированная |
ХВГ, ХВСГ, 3Х2МНФ, 4ХС, 4ХНМФС, 5ХНВ, 5ХНВС, 5ХВ2СФ, 6Х3МФС, 6Х4М2ФС, 7ХФ, 8ХФ, 9Х1, 9ХФ, 9ХС, 9Г2Ф, 9ХВГ, 9Х5ВФ, 11ХФ, 12Х1 |
Инструментальная валковая |
45ХНМ, 60ХН, 75ХСМФ, 9Х2, 55Х, 60ХСМФ, 7Х2СМФ, 9Х2МФ, 60Х2СМФ, 75ХМ, 90ХМФ, 60ХГ, 75ХМФ, 90ХФ |
Инструментальная штамповая |
3Х3М3Ф, 4Х3ВМФ, 4Х5МФС, 6ХВ2С, 7ХГ2ВМ, Х12, Х12МФ, 4Х4МФС, 5ХВ2С, 6ХВГ, Х12ВМ, Х12Ф1, 3Х2В8Ф, 4Х2В2ФС, 5ХГМ, 6ХС, 8Х3, Х12ВМФ, Х6ВФ, 4Х5МФ1С, 5ХНМ, 7Х3, Х12М, 5Х2МНФ, 4Х5В2ФС, |
Инструментальная быстрорежущая |
Р2М5, Р6М3, Р6М5, Р6АМ5, Р6М5К5, Р6АМ5Ф3, Р6М5Ф3, Р9, Р9К5, Р9Ф5, Р9К10, Р18 |
Виды жаропрочной стали |
Марки сталей и сплавов |
Жаропрочная низколегированная |
12ХМ, 12Х1МФ, 15Х1МФ, 15Х5, 15Х5ВФ, 15Х5М, 15ХМ, 15Х2М2ФБС |
Жаропрочная высоколегированная |
08Х16Н11М3, 08Х16Н13М2Б, 08Х21Н6М2Т, 09Х14Н16Б, 10Х11Н20Т2Р, 10Х11Н20Т3Р, 10Х23Н18, 12Х14Н14В2М, 13Х11Н2В2МФ, 16Х11Н2В2МФ, 20Х20Н14С2, 20Х23Н13, 20Х23Н18, 45Х14Н14В2М |
Жаропрочная релаксационностойкая |
20Х1М1Ф1БР, 20Х1М1Ф1ТР, 25Х1М1Ф, 25Х1МФ, 25Х2М1Ф, 30ХМ, 30ХМА, 38Х2МЮА |
Жаропрочный сплав |
ХН32Т, ХН35ВТ, ХН35ВТЮ ХН38ВТ, ХН45Ю, ХН55МВЮ, ХН60ВТ, ХН70Ю, ХН77ТЮР, ХН78Т |
Виды коррозионно-стойкой стали |
Марки сталей и сплавов |
Коррозионно-стойкая |
03ХН28МДТ, 06ХН28МТ, 06ХН28МДТ, ХН65МВ |
Коррозионно-стойкая качественная |
03Х18Н11, 07Х16Н4Б, 07Х16Н6, 08Х17Н13М2Т, 08Х17Н6Т, 08Х18Н12Т, 08Х22Н6Т, 09Х16Н4Б, 10Х17Н13М2Т, 10Х17Н13М3Т, 20Х17Н2, 25Х13Н2, 98Х18 |
Коррозионно- стойкая жаропрочная |
08Х13, 08Х17Т, 08Х18Н10, 08Х18Н10Т, 10Х18Н10Т, 12Х18Н12Т, 12Х18Н9, 12Х18Н10Т, 14Х17Н2, 15Х25Т, 20Х13, 30Х13, 40Х13 |
Виды испытаний
В соответствии с ГОСТ 8479-90 поставляем поковки I, II, III, IV, V групп в зависимости от объема обязательных испытаний:
Группа поковок |
Виды испытаний |
Условия комплектности партии |
Сдаточные характеристики |
Документы |
I |
Без испытаний |
Поковки одной или разных марок стали |
- |
Хим. анализ |
II |
Определение твердости |
Поковки одной марки стали, совместно прошедшие термическую обработку |
Твердость |
Сертификат |
III |
Определение твердости |
Поковки одной марки стали, прошедшие термическую обработку по одинаковому режиму |
Твердость |
Сертификат |
IV |
- Испытание на растяжение, - Определение твердости и ударной вязкости |
Поковки одной плавки стали, совместно прошедшие термическую обработку |
Предел текучести Относительное сужение Ударная вязкость |
Сертификат, паспорт |
V |
- Испытание на растяжение, - Определение твердости и ударной вязкости |
Принимается индивидуально каждая поковка |
Предел текучести Относительное сужение Ударная вязкость |
Сертификат, паспорт |
По согласованию с заказчиком возможно проведение других лабораторных испытаний металлопродукции.
В этом случае поковки также относятся к одной из групп: II, III, IV и V.
Справочная информация
1. Поковки. Определение, стандарты, виды
Поковка, кованая заготовка – это промежуточное изделие металлургии, полученное в результате пластической деформации металла: ковкой, или горячей объемной штамповкой в кузнечно-штамповочном производстве.
Производство с учетом массы изделий, их форм, припусков, качества обработки осуществляется в соответствии со следующими стандартами:
- ГОСТ 1133-71 для поковок круглого и квадратного сечения
- ГОСТ 8479-70 для поковок из конструкционной углеродистой и легированной стали
- ГОСТ 7505-89 для стальных штамповок
- ГОСТ 26645-85 для отливок
Если габариты требуемой детали значительно превосходят стандарты сортового проката, исходную заготовку целесообразно получить именно методом ковки или штамповки. Например, огромные валы, кольца, масса которых может достигать порядка 10-350 тонн. Такие ответственные детали должны соответствовать целому ряду технических характеристик и требований.
Отдельно стоит отметить поковки с Морским и Речным регистром, которые изготавливаютсяс предварительной механической обработкой и последующим ультразвуковым контролем. Используются для производства гребных валов, поршней, подъемно-мачтовых устройств, комингсов и иных деталей, используемых в судостроении.
Виды и форма поковок
По форме сечения поковки бывают:
- круглые (кованый круг, кованые оси и валы..)
- квадратные
- прямоугольные
- кольца, диски (с отверстием и без, раскатные)
- цилиндры (с отверстием и без)
Преимущества поковок перед литыми заготовками:
- Поковки имеют лучшие механические свойства: более высокую прочность и вязкость, более устойчивы к усталостным нагрузкам. Следовательно, поковки лучше подходят для деталей, к которым предъявляются требования высокой прочности, ударной вязкости и сопротивления
- Кованые заготовки менее подвержены износу и хорошо выдерживают высокие нагрузки
- Поковки лучше подвергаются механической обработке.
2 Классификация поковок
В зависимости от оборудования, на котором произведены поковки, их подразделяют на следующие виды:
- поковки, полученные на молотах
- поковки, изготовленные на кривошипных горячештамповочных прессах (КГШП)
- поковки, штампуемые на гидравлических прессах
- поковки, штампуемые на горизонтально-ковочных машинах (ГКМ)
2.1 Классификация молотовых поковок
Молотовые штампованные поковки разделяют на группы по следующим признакам:
- по способу штамповки — плашмя или осадкой в торец;
- по форме поковки и соотношению ее основных размеров;
- по форме поперечных сечений поковки;
- по формам главной оси поковки и линии разъема.
В зависимости от выбранного способа штамповки, в значительной степени определяющего характер технологического процесса, различают две группы молотовых поковок.
I группа |
удлиненные и изогнутые поковки, штампуемые перпендикулярно оси заготовки (штамповка плашмя). Для этих поковок характерна значительная величина отношения их длины к средней ширине в плане. |
II группа |
круглые и квадратные поковки или поковки, близкие к ним по форме в плане (два взаимно перпендикулярных размера в плане приблизительно равны); поковки с отростками (основные элементы имеют круглую или квадратную форму). |
2.2 Классификация поковок, изготовленных на кривошипных горячештамповочных прессах (КГШП)
Поковки, штампуемые на КГШП, по сравнению с молотовыми поковками, отличаются меньшим разнообразием формы, и подразделяются следующим образом:
- в зависимости от характера формоизменения и течения металла при формоизменении — на два класса: класс поковок, получаемых с преобладанием процесса осадки, и класс поковок, получаемых с преобладанием процесса выдавливания;
- в зависимости от конфигурации и сложности изготовления — на пять основных групп. Методы изготовления учитывают при выделении подгрупп поковок.
Группа |
Характеристики |
Схематичное изображение |
I |
осесимметричные поковки, изготовляемые осадкой в торец или осадкой с одновременным выдавливанием — т.е. поковки круглые в плане или близкие к этой форме, в том числе квадратные и близкие к круглым и квадратным в плане, а также поковки с отростками. |
Штамповку осуществляют в открытых и закрытых штампах. |
II |
поковки удлиненной формы, имеющие небольшую разницу в площадях поперечных сечений. |
|
III |
поковки удлиненной формы, имеющие значительную разницу в площадях поперечных сечений. |
|
IV |
поковки с изогнутой осью |
|
V |
поковки, изготовляемые выдавливанием |
|
2.3 Классификация поковок, штампуемых на гидравлических прессах
На гидравлических прессах штампуют поковки простой формы (типа дисков и колес) и сложной формы (коленчатый вал) следующих видов:
- крупные поковки, которые невозможно получить на другом кузнечном оборудовании из-за его недостаточной мощности;
- поковки, для штамповки которых необходим большой рабочий ход, а усилие деформирования не имеет максимального значения в начале или в конце хода деформации (например, при глубокой прошивке);
- поковки, требующие специальных физико-химических условий горячей деформации.
Все поковки, штампуемые на гидравлических прессах, в зависимости от применяемых для их изготовления операций, подразделяют на группы:
Группа |
Определение |
Схематичное изображение |
I |
поковки типа стаканов с гладкими стенками или сложной формы с глухими или сквозными отверстиями (корпуса снарядов, гильзы, втулки, муфты, цилиндры и др.). |
|
II |
поковки типа дисков: невысокие чашки и втулки с фланцами, роторы турбин, диафрагмы и др. |
|
III |
поковки с вытянутой осью типа коленчатых валов и др. |
|
IV |
поковки типа крестовин (втулки авиационного винта и т.д.), изготовляемых комбинированной штамповкой в разъемных штампах |
|
V |
поковки типа панелей, получаемые в блочных и секционных штампах |
|
2.4 Классификация поковок, штампуемых на горизонтально-ковочных машинах (ГКМ)
Поковки, изготовляемые на ГКМ, в зависимости от их конфигурации подразделяют на шесть основных групп.
Группа |
Определение |
Схематичное изображение |
I |
поковки типа стержня с утолщением (размеры поперечного сечения заготовки сохраняются постоянными в стержневой части поковки). |
|
II |
поковки типа колец и втулок. Размеры поперечного сечения поковок этой группы изменяются на всех участках поковок по сравнению с исходной заготовкой. |
|
III |
поковки с полостями или глухими отверстиями. По конфигурации наружной и внутренней поверхностей эти поковки аналогичны поковкам II группы, но по технологии отличаются отсутствием пробивки. |
|
IV |
полые поковки, штампуемые из труб. К ним относят поковки, размеры поперечных сечений которых изменяются на концевых участках. |
|
V |
поковки смешанной формы, разнообразные по конфигурации, в том числе с отростками и развилинами, с прямой и криволинейной осью, с глухими или сквозными отверстиями, ось которых может не совпадать с осью стержневой части поковки. |
|
VI |
поковки, требующие дополнительной штамповки на ГКМ (имеют разнообразную форму) |
|
3 Процесс получения поковок методом ковки
Кованые заготовки получают следующими способами:
- ковка
- штамповка (горячая объемная штамповка, холодная штамповка, листовая штамповка)
Ковка
Ковка – технологический процесс получения заготовок или деталей в результате пластического деформирования нагретой исходной заготовки в бойках без ограничения бокового течения металла.
Сущность процесса ковки заключается в формоизменении исходной заготовки вдоль одной (вертикальной) или двух осей (вертикальной и горизонтальной).
Исходные заготовки – отливки, блюмы, слябы, прокат.
Инструмент – бойки (плоские, фигурные), плиты для осадки, прошивки, кольца, раскатки, пережимки, обжимки, топоры, подкладные штампы.
Оборудование:
- Ручная ковка: кувалда, наковальня
- Машинная ковка: Паровоздушные молоты и гидравлические прессы
Паровоздушные молоты – машины ударного действия (для высокопластичных материалов)
Гидравлические прессы – машины статического действия (для малопластичных материалов)
|
Силы Р оказывают сжимающее действие, способствующее течению металла в продольном направлении.
В фигурных бойках заготовку получают более точной цилиндрической формы.
|
Ковку без подкладных штампов применяют для получения заготовок простой формы массой до 250т. Подкладные штампы позволяют получить заготовку относительно сложной формы.
3.1 Основные технологические этапы ковки
В процессе производства поковок методом ковки выделяют следующие основные этапы:
- Предварительные операции (для получения заготовки нужных размеров и формы): обкатка слитка, отрубка, разрубка.
- Основные операции (деформация нагретой заготовки под давлением): осадка, высадка, прошивка, пробивка и вырубка, протяжка, разгонка, отрубка, гибка и закручивание.
- Отделочные операции: правка, клеймение.
Осадка – уменьшение высоты заготовки при увеличении площади ее поперечного сечения
|
|
Высадка – осадка заготовки на части ее длины
|
|
Пробивка – получение в заготовке сквозного отверстия. Разделение исходной заготовки по замкнутому контуру, когда изделием является часть заготовки с пробитым отверстием, не смещаемая в матрицу.
|
|
Вырубка – разделение исходной заготовки по замкнутому контуру, когда изделием является часть заготовки, смещаемая в матрицу |
|
Прошивка – получение полостей в заготовке |
|
Протяжка – удлинение заготовки или ее части за счет уменьшения толщины заготовки |
|
Гибка – придание заготовке изогнутой формы |
|
Разгонка – операция увеличения ширины части заготовки за счет уменьшения ее толщины |
|
Отрубка – отделение части заготовки. Попасть в полость первоначального надруба трудно, поэтому всегда образуется заусенец. Операция выполняется в 2 шага. |
|
3.2 Преимущества и недостатки ковки
Преимущества:
- Более высокое качество металла с повышенной прочностью, пластичностью и ударной вязкостью, лучшей структурой, меньшим количеством дефектов по сравнению с отливками.
- Возможность изготовления крупногабаритных поковок: массой до сотен тонн, длиной до десятков метров. Такие изделия с высоким качеством металла другими способами получить невозможно.
- Низкие затраты на оборудование и инструменты ввиду их универсальности при единичном производстве.
Благодаря получению высокой пластичности материала и прочности, ковка рекомендуется для заготовок высоконагруженных деталей: роторов гидротурбин, валов, дисков турбин, колес и др.
Недостатки:
- Низкая производительность и большая трудоемкость по сравнению со штамповкой
- Большие отходы металла и объем последующей механической обработки из-за больших напусков, припусков и допусков.
3.3 Оборудование для ковки
Общая классификация оборудования для ковки:
Ковка |
Молоты |
- приводные-пневматические - паровоздушные |
Прессы и машины |
-гидравлические прессы - механические кривошипные прессы - обрезные кривошипные прессы - винтовые фрикционные прессы - кривошипные горячештамповочные прессы |
3.3.1 Молоты
Молоты - это машины динамического ударного действия.
Металл деформируется за счет энергии, накопленной подвижными (падающими) частями молота к моменту их соударения с заготовкой.
Часть энергии теряется на упругие деформации инструмента и колебания шабота (детали молота, на которую устанавливают нижний боек).
Чем больше масса шабота, тем больше КПД (практически масса шабота бывает в 15р больше массы падающих частей).
Пневматический молот
Пневматический молот - применяют для ковки мелких поковок (примерно до 20кг) и изготавливают с массой падающих частей 50-1000 кг.
|
Пневматический молот 1 – баба 2 - верхний боек 3 – нижний боек 4 - шабот |
Паровоздушный молот
Такие молоты приводятся в действие паром или сжатым воздухом давлением 0,7-0,9 МН/м2.
В зависимости от конструкции станины паровоздушные ковочные молоты бывают:
- Арочные
- Мостовые
- Одностоечные
|
Паровоздушный ковочный молот арочного типа:
1 — рабочий цилиндр; 2 — золотниковая коробка; 3 — боковые стойки; 4 — шток; 5 — баба; 6 — верхний боёк; 7 — рукоятка; 8 — нижний боёк; 9 — промежуточная подушка; 10 — общая плита; 11 — шабот |
Ковочные паровоздушные молоты строят с массой падающих частей 1000-8000 кг. На этих молотах изготавливают поковки средней массы (20 - 350 кг) преимущественно из прокатанных заготовок.
3.3.2 Прессы
Гидравлические прессы
В гидравлическом прессе усилие создается с помощью жидкости (водной эмульсии или минерального масла) высокого давления (20 – 30 МН/м2), подаваемой в рабочий цилиндр.
|
На гидропрессах штампуют крупные поковки, которые невозможно получить на другом кузнечном оборудовании, а также поковки, для которых необходим большой рабочий ход силовых органов. Область применения – массовое производство (например, железнодорожных колес подвижного состава, диски, коленвалы и т.д.,.). |
3.4 Основные показатели качества поковок и типы производств
Сравнительная таблица характеристик способов ковки