Термическая обработка
Наши возможности
Компания Апгрейд оказывает услуги по проведению всего цикла термической обработки заготовок из конструкционных, инструментальных, коррозионно-стойких, жаростойких и жаропрочных сталей и сплавов.
Виды термообработки, которые выполняет наша компания: Отправить запрос
- Закалка (В масло и в воду, Поверхностная закалка ТВЧ, Объемная закалка, Плазменная закалка);
- Нормализация;
- Отпуск (Высокий отпуск, Средний отпуск, Низкий отпуск);
- Отжиг (Полный отжиг, Неполный отжиг, Низкотемпературный отжиг, Изотермический отжиг);
- Сорбитизация;
- Цементация;
- Старение.
Процесс термообработки осуществляется квалифицированными термистами с соблюдением всех установленных нормативов и контролируется на всех этапах.
Участок термообработки располагается в кузнечном цехе и оснащен следующим оборудованием: Фотогалерея
Назначение |
MaxТнагр, °С |
Габариты рабочего пространства, мм |
Масса садки, кг |
Среда нагрева |
|
Электропечь шахтная СШЦМ 8.12/9,5и9 в комплекте с модулем подготовки и контроля состава печных атмосфер МППА-ssi 04 на газообразном карбюризаторе |
|||||
Цементация, нагрев под закалку в автоматически регулируемой атмосфере. |
950 |
Ø800 х 1300 |
600 |
Атмосфера на основе углеродосодержащих газов: Карбюризатор: пропан-бутановая смесь в баллонах или сетевой природный газ Окислитель: воздух |
|
Многофункциональная шахтная закалочная печь ПШЗ 10.30/12И1 с гидроприводом |
|||||
Нагрев под закалку легированных сталей, обжиг длинномерных деталей и другие виды термической обработки, когда требуется нагрев до температуры не выше 1200 °С. |
1200 |
Ø1000 х 3000 |
4000 |
Воздух (окислительная) |
|
Электропечь камерная ПКМ 6.8.4/12,5 |
|||||
Для проведения различных видов термообработки металлических изделий в условиях воздушной атмосферы. |
1250 |
600х800х400 |
250 |
Воздух (окислительная) |
|
Печь шахтная ПШО 10.20/7И1 |
|||||
Для проведения режимов термообработки, требующих равномерного прогрева деталей и поддержания температуры с высокой точностью (отпуск, отжиг). |
700 |
Ø1000 х 2000 |
Воздух (окислительная) |
||
Электропечь камерная ПЛ-20/12,5 |
|||||
Для различных видов термообработки. |
1250 |
420х240х185 |
Воздух (окислительная) |
Закалочные ванны:
Назначение |
Закалочная среда |
Размеры рабочей зоны, мм |
Масса садки, кг |
Закалочная ванна ВЗ 15.100.15/0,8П |
|||
Для закалки металлических изделий в водополимерной среде рабочего пространства. Полное исключение «пятнистости» при закалке, благодаря одинаковой скорости охлаждения всей поверхности детали. |
Водный раствор полимера |
10000 х 1500 х 1500 (длина х ширина х высота) |
6000 |
Профессиональная закалочная ванна ВШЗ 10.35/0,8п |
|||
Для закалки металлических изделий в водополимерной среде рабочего пространства. |
Водный раствор полимера |
Ф1000 х 3500 (Ф х высота) |
1000 |
Закалочная ёмкость ВШЗ 25.30/0,8 |
|||
Для закалки металлических изделий в водной среде рабочего пространства. |
Вода |
Ø2500 х 3000 |
2000 |
Закалочная ёмкость ВШМ 25.40/0,8 |
|||
Для закалки металлических изделий в водной среде рабочего пространства. |
Масло |
Ø2500х4000 |
3000 |
Закалочный комплекс ТВЧ TESLINE 180Z-E-A20 |
|||
Для закалки ТВЧ внешних и внутренних поверхностей заготовок. |
|
1000 |
Термообработанные заготовки сопровождаются следующей документацией:
- паспорт заготовки;
- сертификат;
- схема нагрева (термообработка продукта);
- протокол аккредитованной лаборатории, удостоверяющий соответствие основного материала требованиям заказчика.
Заказать термообработку заготовок в компании Апгрейд можно, отправив заявку по email info@9hs.ru, связавшись с нашим менеджером по телефону 7(495) 984-97-09 или через форму обратной связи на сайте.
Оказываем услуги по термообработке следующих металлов и сплавов:
Виды конструкционной стали |
Марки сталей |
Сталь конструкционная легированная |
12ХН3А, 12Х2Н4А, 12Х2НВФА, 15Х, 15ХМ, 18ХГТ, 18Х2Н4МА, 18Х2Н4ВА, 20Х, 20ХН, 20ХН3А, 20Х2Н4А, 25ХГТ, 30Х, 30ХГСА, 30ХГТ, 30ХГСН2А, 34ХН1М, 35ХГСА, 38ХМ, 38ХА, 38ХМА, 38ХС, 38Х2Н2МА, 38Х2Н2ВА, 38ХН3МФА, 40Г2, 40Х, 40ХН, 40ХН2МА, 40Х2Н2ВА, 40Х2Н2МА, 40ХН2ВА, 40ХФА, 45ХН2МФА, 10Г2, 07Х3ГНМЮА, 12ХН, 19ХГН, 12ХН2, 15Г, 15ХГН2ТА, 15ХФ, 18ХГ, 20Г, 13ХФА, 25ХСНВФА, 28Х3СНМВФА, 16Х3НВФМБ, 35Х, 38ХН3МА, 30Х2НВА, 30Х3МФ, 30ХН2МА, 30ХН2МФА, 30ХН3А, 30ХРА, 34ХН1МА, 34ХН3МА, 35Г2, 36Г2С, 38ХГМ, 38ХГН, 38ХН3ВА, 40ХГНМ, 40ХМФА, 45Г, 45Х, 45ХН, 50Г, 50Х, 50ХН, 38ХН3А, 35Х3НМ |
Сталь конструкционная углеродистая качественная |
Ст. 10, Ст. 15, Ст. 20, 20К, Ст. 35, Ст. 45, Ст. 50, 25ХГМ, 25ХГСА, 25Х2Н4МА, 30Г, 20ХГНР, 20ХН2М, 20ХГСА, 20ХН2МА, 25ГС, 25Х2Н4ВА, 20ХГНМ, 40ХН2СВА, 07Х21Г7АН5, Ст. 25, Ст. 30, Ст. 40, Ст. 55, Ст. 60 |
Сталь конструкционная рессорно – пружинная |
50ХФА, 60С2А, 65Г, 55С2А, 60Г, 60С2, 60С2ХА, 60С2ХФА, 65С2ВА, 70Г, Ст. 65, Ст. 70 |
Сталь конструкционная для сварных конструкций |
09Г2С, 10ХСНД, 15ХСНД, 17Г1С, 17ГС |
Сталь конструкционная подшипниковая |
ШХ15, 8Х4В9Ф2, ШХ15СГ, ШХ20СГ |
Сталь конструкционная повышенной обрабатываемости |
А12, АС14 |
Сталь конструкционная углеродистая обыкновенного качества |
Ст. 3, Ст. 5 |
Виды инструментальной стали |
Марки сталей |
Инструментальная углеродистая |
У7, У7А, У8, У8А, У8Г, У9, У9А, У10, У10А, У11, У11А, У12, У12А, У13 |
Инструментальная легированная |
ХВГ, ХВСГ, 3Х2МНФ, 4ХС, 4ХНМФС, 5ХНВ, 5ХНВС, 5ХВ2СФ, 6Х3МФС, 6Х4М2ФС, 7ХФ, 8ХФ, 9Х1, 9ХФ, 9ХС, 9Г2Ф, 9ХВГ, 9Х5ВФ, 11ХФ, 12Х1 |
Инструментальная валковая |
45ХНМ, 60ХН, 75ХСМФ, 9Х2, 55Х, 60ХСМФ, 7Х2СМФ, 9Х2МФ, 60Х2СМФ, 75ХМ, 90ХМФ, 60ХГ, 75ХМФ, 90ХФ |
Инструментальная штамповая |
3Х3М3Ф, 4Х3ВМФ, 4Х5МФС, 6ХВ2С, 7ХГ2ВМ, Х12, Х12МФ, 4Х4МФС, 5ХВ2С, 6ХВГ, Х12ВМ, Х12Ф1, 3Х2В8Ф, 4Х2В2ФС, 5ХГМ, 6ХС, 8Х3, Х12ВМФ, Х6ВФ, 4Х5МФ1С, 5ХНМ, 7Х3, Х12М, 5Х2МНФ, 4Х5В2ФС, |
Инструментальная быстрорежущая |
Р2М5, Р6М3, Р6М5, Р6АМ5, Р6М5К5, Р6АМ5Ф3, Р6М5Ф3, Р9, Р9К5, Р9Ф5, Р9К10, Р18 |
Виды жаропрочной стали |
Марки сталей и сплавов |
Жаропрочная низколегированная |
12ХМ, 12Х1МФ, 15Х1МФ, 15Х5, 15Х5ВФ, 15Х5М, 15ХМ, 15Х2М2ФБС |
Жаропрочная высоколегированная |
08Х16Н11М3, 08Х16Н13М2Б, 08Х21Н6М2Т, 09Х14Н16Б, 10Х11Н20Т2Р, 10Х11Н20Т3Р, 10Х23Н18, 12Х14Н14В2М, 13Х11Н2В2МФ, 16Х11Н2В2МФ, 20Х20Н14С2, 20Х23Н13, 20Х23Н18, 45Х14Н14В2М |
Жаропрочная релаксационностойкая |
20Х1М1Ф1БР, 20Х1М1Ф1ТР, 25Х1М1Ф, 25Х1МФ, 25Х2М1Ф, 30ХМ, 30ХМА, 38Х2МЮА |
Жаропрочный сплав |
ХН32Т, ХН35ВТ, ХН35ВТЮ ХН38ВТ, ХН45Ю, ХН55МВЮ, ХН60ВТ, ХН70Ю, ХН77ТЮР, ХН78Т |
Виды коррозионно-стойкой стали |
Марки сталей и сплавов |
Коррозионно-стойкая |
03ХН28МДТ, 06ХН28МТ, 06ХН28МДТ, ХН65МВ |
Коррозионно-стойкая качественная |
03Х18Н11, 07Х16Н4Б, 07Х16Н6, 08Х17Н13М2Т, 08Х17Н6Т, 08Х18Н12Т, 08Х22Н6Т, 09Х16Н4Б, 10Х17Н13М2Т, 10Х17Н13М3Т, 20Х17Н2, 25Х13Н2, 98Х18 |
Коррозионно- стойкая жаропрочная |
08Х13, 08Х17Т, 08Х18Н10, 08Х18Н10Т, 10Х18Н10Т, 12Х18Н12Т, 12Х18Н9, 12Х18Н10Т, 14Х17Н2, 15Х25Т, 20Х13, 30Х13, 40Х13 |
Наши преимущества
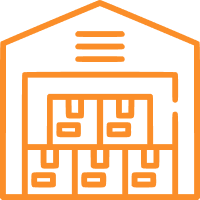
Постоянное складское наличие
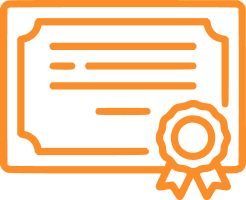
сертифицирована
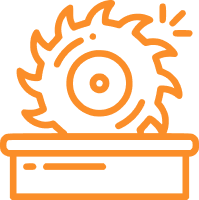
(резка, мех. обработка)

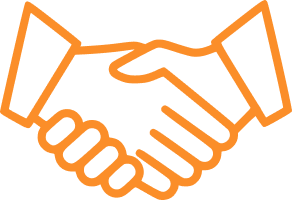
Персональный менеджер
Справочная информация
Термическая обработка
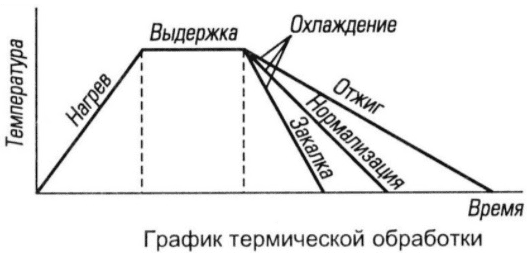
Тепловая обработка применяется:
- на промежуточном этапе производства для увеличения обрабатываемости сплава;
- на окончательном этапе производства для достижения заданных физ.-мех. характеристик.
Общее время нагрева определяется по формуле: Общее время нагрева при ТО = длительность нагрева до необходимой Т + выдержка при этой Т
Длительность прогрева определяется:
- видом печи,
- габаритами заготовки,
- размещением в печи.
Длительность выдержки определяется характером развития фазовых превращений структуры, характеризующихся температурными критическими точками.
На диаграмме железо углерод буквой A обозначены критические точки, определяющие Тнагр для ТО.
ВИДЫ ТЕРМИЧЕСКОЙ ОБРАБОТКИ
1. Нормализация (нормализованный отжиг)
В результате нормализации:
- ↑ прочность;
- ↑ вязкость;
- ↑ сопротивление излому;
- ↑ обрабатываемость;
- происходит размельчение зерна;
- устраняются явление наклепа и внутренние напряжения.
Достигаемая твердость не более 300 НВ.
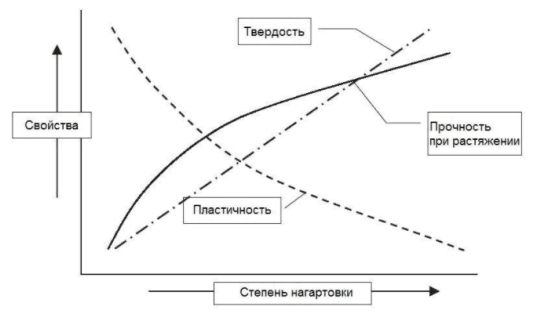
Наклёп (нагарто́вка) — упрочнение верхних слоев вследствие деформации структуры при пластической деформации при Т ≤ Т рекристаллизации.
Как видно на рисунке справа с увеличением степени нагартовки уменьшается пластичность, увеличиваются прочностные характеристики.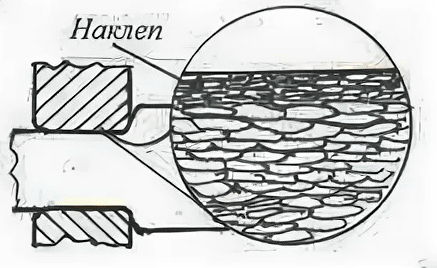
Этапы нормализации:
- прогрев до Т на 30°С-50°С выше А3 (GSE);
- выдержка;
- остывание на воздухе.
2. Отжиг
Этапы отжига:
- прогрев до Т немного выше критических точек;
- выдерживание при этой температуре;
- медленное остывание (в печи).
В результате Отжига:
- достигается равновесная мелкозернистая микроструктура стали;
- устранить внутренние усилиями в структуре стали;
- ↑ вязкости и пластичности;
- ↓ твердости и износостойкости;
- вывести флокены (полости с газом), что позволяет достичь требуемую чистоту сплава
- улучшить обрабатываемость давлением и резанием
Виды отжига:
Вид отжига |
Результат |
Режимы обработки |
График отжига |
ОТЖИГ I РОДА |
|||
Гомогенизация (диффузионный отжиг) Применяется в основном для легированных сталей |
|
|
|
Рекристаллизация (низкий отжиг) используется после обработки пластическим деформированием, которое вызывает упрочнение за счет изменения формы зерна (наклеп). |
|
|
|
Изотермический отжиг Подвергаются легированные стали, для того чтобы произошел распад аустенита. |
|
|
|
Снятие внутренних и остаточных напряжений Используется после сварочных работ, литья, мех. обработки. |
Снятие внутренних и остаточных напряжений Остаточные напряжения возникают:
Остаточные напряжения могут вызвать деформацию деталей при обработке резанием или в процессе эксплуатации. Во многих сплавах они вызывают склонность к растрескиванию, к хрупкому разрушению. |
|
|
ОТЖИГ II РОДА |
|||
Полный отжиг Обычно применяют для эвтектоидных сталей и конструкционных сталей при Тн = ТАс3 + (30 – 50°С) Используется для литых, кованных и штампованных заготовок, которые будут в дальнейшем обрабатываться резанием и подвергаться закалке. |
|
|
|
Неполный отжиг (Сфероидизация) (т.к. входящий в состав стали перлит из пластинчатого превращается в зернистый) Обычно применяют для инструментальных (при Тн = ТАс1 + (30 - 50°С) и заэвтектоидных сталей. |
|
|
|
3. Закалка
Закалка - это упрочняющий вид ТО, состоящий из прогрева заготовки выше Т критич., выдержки и ускоренного охлаждения со скоростью , превышающей критическую (в различных средах: вода, техническое масло, соляные водные растворы, инертные газы).
Полная закалка – осуществляется для доэвтектоидных сталей, прогрев на 30-50С выше Ас3.
Неполная закалка - осуществляется для заэвтектоидных сталей, прогрев на 30-50°С выше Ас1.
Низкоуглеродистые стали (С до 0,3%) практически не закаливаются.
Закалка – это не окончательный этап, после нее заготовку необходимо подвергнуть отпуску.
Структура: мартенситная.
Результат:
- ↑ твердость и ↑ прочность
- ↓ пластичность и ↓ предел на сжатие
- ↑ износостойкость
- ↑ хрупкость
В случае если нет необходимости проведения объемной закалки, калению подвергается только верхний слой заготовки на установках ТВЧ.
Глубина прокаливаемости 1- 10мм.
В результате ↑ износоустойчивость поверхности при сохранении вязкости внутри.
Наиболее ответственной операцией при закалке является охлаждение, которое должно осуществляться со скоростью, равной или выше критической, для получения структуры мартенсита.
Для углеродистых сталей критическая скорость составляет 1400...400 °С/с - такие скорости охлаждения достигаются погружением закаленных деталей в холодную воду или в воду с добавками солей.
Наилучшей закалочной средой является та, которая быстро охлаждает в интервале Т=550...650 С и медленно охлаждает при Т ниже 200...300 С. Закалку углеродистых и некоторых низколегированных сталей проводят в воде и водных растворах NaCl и NaOH. Для легированных сталей применяют минеральное масло.
На практике применяют закалку непрерывную, ступенчатую и закалку в 2х средах.
Закалка в 2х средах включает охлаждение с прерыванием: в воде до Т=300°С, затем на воздухе или в масле до Т=20°С.
Ступенчатая закалка состоит из следующих этапов:- охлаждение прогретой заготовки в расплавленных солях;
- недолгая выдержка с целью равномерного прогревания заготовки по сечению;
- охлаждение на воздухе.
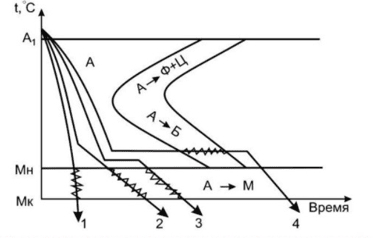
- непрерывная закалка
- закалка в двух средах
- ступенчатая закалка
- изометрическая закалка
4. Отпуск
ОТПУСК – это финишная ТО и осуществляется для достижения требуемых характеристик стали.
Отпуск состоит из этапов:
- прогрева до Т ≤ Т критич,
- выдержки
- охлаждения на воздухе.
Цель:
- увеличение однородности микроструктуры,
- снятие структурных и температурных напряжений, образующихся при закалке.
Результат:
- ↑ пластичности,
- ↑ ударной вязкости,
- ↑ предела упругости,
- ↓ твердости,
- снятие внутренних усилий в структуре.
Виды отпуска
Вид отпуска |
Результат |
Режимы обработки |
Применение |
НИЗКИЙ ОТПУСК (на мартенсит) |
Структура: Мартенсит закалки переходит в мартенсит отпуска. |
|
Применяют для деталей, работающих в условиях изнашивания, высоких контактных нагрузок: детали подшипников качения, измерительный и режущий инструмент, а также деталей машин, подвергнутых поверхностной закалке. |
СРЕДНИЙ ОТПУСК (на троостит)
|
Структура: Мартенсит закалки переходит в троостит отпуска. |
|
Применяют для закаленых изделий, которые должны иметь макс упругие свойства при относительно высокой твердости (из высокоуглеродистых сталей): пружины, мембраны, рессоры, ударный инструмент - зубила, штампы и др. |
ВЫСОКИЙ ОТПУСК (на сорбит)
|
Структура: Мартенсит закалки переходит в сорбит отпуска. |
|
Применяют для конструкционных среднеуглеродистых сталей, для деталей, испытывающих статические, динамические и циклические, ударные и знакопеременные нагрузки: валы, шатуны двигателей, полуоси, оси автомобилей и тракторов, болты и др. |
5. Улучшение стали
Улучшение стали – состоит из закалки и одного из видов отпуска стали.
Вид улучшения стали |
Структура |
Твердость |
Применение |
ЗАКАЛКА И НИЗКИЙ ОТПУСК |
|
60 HRC |
Применяется для деталей машин, работающих в условиях изнашивания, высоких контактных нагрузок (детали подшипников качения, режущий, измерительный инструмент). |
ЗАКАЛКА И СРЕДНИЙ ОТПУСК |
Троостит отпуска (обеспечивает высокий предел упругости, выносливости и релаксационной стойкости). |
40 HRC |
Применяется для упругих элементов машин из высокоуглеродистых сталей (пружины, рессоры, мембраны). |
ПОЛНАЯ ЗАКАЛКА И ВЫСОКИЙ ОТПУСК (термическое улучшение) |
зернистый сорбит отпуска Данная комбинация ТО создает наилучшее сочетание прочности и пластичности стали при повышенной ударной вязкости. |
30 HRC |
Применяется для деталей машин из среднеуглеродистых сталей, испытывающих статические и динамические/циклические нагрузки (валы, оси, шатуны, крепежные детали). |