Лабораторные испытания
Наши возможности
Компания Апгрейд имеет в своем распоряжении лабораторию для контроля качества производимой продукции и проведения требуемых испытаний:
- Испытания на растяжение с целью определения прочностных характеристик стали;
- Испытания на твердость для определения устойчивости стали к остаточной деформации;
- Испытания на стойкость к межкристаллитной коррозии стали (МКК) методами АМУ, АМ;
- Металлографические исследования (макроанализ и микроанализ структуры стали);
- Испытания на ударную вязкость для оценки прочности стали;
- Ультразвуковой контроль (УЗК) на выявление внутренних дефектов с стали;
- Определение химического состава стали (спектрометрия);
- Визуально-измерительный контроль (ВИК).
Наша лаборатория оснащена следующим оборудованием:
Оборудование | Назначение |
Микроскоп Olimpus PMEU F200 | Микроанализ структуры стали |
Оптико-эмиссионный спектрометр ДФС – 500 | Контроль химического состава |
Твердомер Бринелля ТБ-5004 | Испытания на твердость |
Машина испытательная универсальная TiniusOlsen 50ST | Испытания на растяжение |
Маятниковый копер для определения ударной вязкости по Шарпи | Испытания на ударную вязкость |
Вся производимая нами продукция:
- ПРОВЕРЯЕТСЯ НА ХИМ.СОСТАВ;
- ПРОХОДИТ КОНТРОЛЬ МЕХАНИЧЕСКИХ СВОЙСТВ (испытания на ударную вязкость, контроль твердости по Бринеллю НВ, испытания на растяжение);
- ПРОХОДИТ НЕРАЗРУШАЮЩИЙ КОНТРОЛЬ (по требованию): методом УЗК на наличие внутренних дефектов;
- ИССЛЕДОВАНИЯ МАКРО И МИКРОСТРУКТУРЫ (по требованию): металлографические исследования (оценка формы, размера и расположения зерен металла и неметаллических включений; определение микротрещин, пор, раковин; анализ микроструктуры после термообработки и обработки металлов давлением);
- ИСПЫТАНИЯ НА СТОЙКОСТЬ К МЕЖКРИСТАЛЛИТНОЙ КОРРОЗИИ (МКК) для нержавеющих марок сталей (по требованию);
- ПОСТАВЛЯЕТСЯ С СЕРТИФИКАТОМ КАЧЕСТВА.
В случае необходимости проведения дополнительных испытаний для подтверждения достижения требуемых характеристик продукции, отправьте запрос по электронной почте info@9hs.ru , свяжитесь с нашим менеджером по телефону 7(495) 984-97-09 или через форму обратной связи на сайте.
Фотогалерея
Наши преимущества
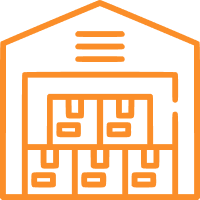
Постоянное складское наличие
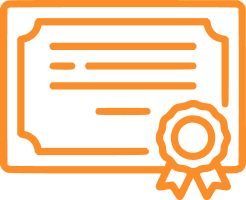
сертифицирована
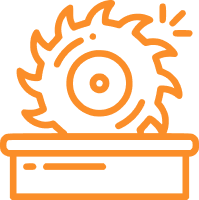
(резка, мех. обработка)

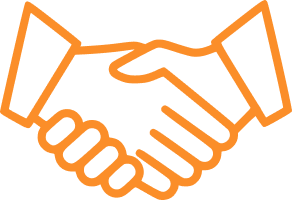
Персональный менеджер
Справочная информация
РАЗРУШАЮЩИЙ КОНТРОЛЬ
Разрушающий контроль (механические испытания) используется для опциональных тестирований отдельно взятых экземпляров продукции.
Это комплекс методик, заключающихся в разрушении испытуемого образца с целью контроля его характеристик требуемому уровню качества. При этом по окончании испытаний образец теряет свои эксплуатационные свойства.
На основе результатов механических испытаний образцов составляется заключение о качестве соответствующей партии продукции.
Недостаток данного метода заключается в том, что он не гарантирует качество каждого изделия в партии. Степень достоверности определяется однородностью свойств в образцах и в эксплуатируемых деталях, и схожестью условий при исследовании и реальном использовании.
Механические испытания включают:
- Механические статические испытания;
- Механические динамические испытания;
- Методы измерения твердости;
- Испытания на коррозионную стойкость;
- Методы технологических испытаний;
- Методы исследования структуры материалов;
- Методы определения содержания элементов.
1. Механические статические испытания – заключается в воздействии на испытуемый образец постепенно увеличивающейся или статической нагрузки, являющийся наиболее востребованным и дает возможность оценить большой набор прочностных и пластических характеристик материала
К статическим испытаниям относятся испытания:
Начальный образец: |
![]() |
|
![]() |
|
![]() |
|
![]() |
|
![]() |
1.1 Испытание на статическое растяжение
Является одним из наиболее распространённых методов при экспертизе сплавов, позволяющих определить прочностные и пластические характеристики металла при разных нагрузках.
Данный метод заключается в воздействии на образец постепенно возрастающей деформирующей нагрузки (на растяжение) пока не произойдет его разрыв. Форма образцов в рабочей зоне является цилиндрической или прямоугольной.
Определяемые характеристики
Предел прочности |
наибольшая механическая нагрузка, при превышении которой испытуемый материал разрушается. |
Предел текучести |
наибольшая механическая нагрузка, при превышении которой происходит пластическая деформация материала после снятия нагрузок (т.е. заготовка получает необратимую деформацию и не возвращается к своей исходной форме). |
Относительное удлинение |
величина, показывающая на сколько процентов, удлиняется материал, прежде чем образец разорвется, и характеризующая его пластичность. |
Относительное сужение |
называется отношение абсолютного уменьшения площади поперечного сечения в шейке на первоначальную площадь и выражается в процентах от начальной площади поперечного сечения. |
Во время проведения испытания установка регистрирует данные, показывающие степень зависимость растяжения образца от нагрузки.
По построенной диаграмме растяжения определяют следующие параметры:
предел текучести, предел прочности, относительной удлинение.
ОВ – участок упругости. После нагружения в пределах этого участка бразец возвращается в исходное состояние. Такая деформация, полностью исчезающая после разгрузки, называется упругой.
ВС – участок общей текучести (площадка текучести). На этом участке на поверхности образца появляется сетка линий, направленная под углом 45 к оси напряжения. Это свидетельствует о появления нового механизма деформации. После разгрузки образец не возвращается в исходное состояние, приобретая остаточную или пластическую, деформацию.
CD – участок упрочнения. Пластическая деформация изменяет внутреннюю структуру металла, в результате чего образец снова проявляет сопротивление деформированию, и растягивающая сила повышается.
DK – участок местной текучести. Точка D диаграммы соответствует появлению на образце локального сужения – шейки. Точка К соответствует разделению образца на части.
1.2 Испытания на сжатие
Целью данного испытания является определение свойств сплава при постепенно увеличивающейся сжимающей нагрузке, которая прикладывается до разрушения образца или до возникновения трещин, или до определения степени осадки.
В результате испытания строится диаграмма деформации, которая показывает предел упругости, предел пропорциональности, предел текучести.
1.3 Испытание на изгиб
Осуществляется применением к образцу (с сечением круглым, квадратным, прямоугольным или многоугольным) нагрузки постоянного направления пока не будет достигнут требуемый угол.
Полученные данные анализируются в соответствии с НТД на продукцию, а в случае ее отсутствия – визуально изучают образец и если трещин нет, считается, что испытание выдержано.
1.4 Испытания на кручение
Целью данного вида испытания является определение предела прочности и предела текучести.
Во время испытания на кручение поперечные сечения материала смещаются относительно оси.
![]() |
![]() |
1.5 Испытания на ползучесть
Ползучестью называется постепенный рост деформации при определенной температуре, происходящий при длительном применении нагрузки, которая является источником внутренних напряжений, превышающих предел упругости и меньших предела текучести материала.
Перед проведением испытания материал нагревают в электрической печи до требуемой температуры. После проведения строятся кривые длительной прочности и ползучести.
Разрушение начинается с появления пор или трещин клиновидной формы на границах зерен сплава, которые увеличиваются и объединяются с течением времени, формируя макротрещины. |
![]() |
2. Динамические механические испытания относятся к категории испытаний на разрушение, где объект исследования подвергается ударным и динамичным нагрузкам, вызывая быстрое деформирование материала. Наиболее распространенной формой таких испытаний является проверка на ударный изгиб. Обычно эти испытания осуществляются при стандартной комнатной температуре или при сниженных температурных условиях. Этот метод широко используется для анализа качества сварки, предоставляя возможность выявить склонность металла к хрупкому разрушению.
2.1 Испытания на ударный изгиб.
Ударная вязкость характеризует свойство стойкости к разрушению при применении динамических нагрузок и определяется на маятниковых корпах.
2.2 Испытания падающим грузом (DWTT - Drop Weight Tear Testing)
Техника испытаний предполагает разрушение образца, оснащенного концентратором нагрузки, при помощи удара молота, который падает свободно с вертикального копра или маятникового устройства при температурах, указанных в НТД. В процессе таких испытаний с использованием падающего груза вычисляется процентное содержание вязкой составляющей в разломе образца. Для испытания основного металла используют стандарт ГОСТ 30456. Процент пластичной части в разломе определяется на основании среднего арифметического из результатов двух образцов, при этом отклонение доли пластической компоненты в одном из образцов от стандартного значения не должно превышать 10%.
Этот метод широко применяется в трубопроизводстве.
3. Методы измерения твердости (твердометрия)
Твердость характеризуется сопротивлением материала вдавливанию в его поверхность инородного тела.
Твердометрия проводятся путем применения к индентору, находящемуся на поверхности, силы под прямым углом, до появления отпечатка.
Идеальным индентором считается алмазный конус, но также применяются металлические сферы.
На практике применяются следующие методы определения твердости (шкалы):
Вид замера твердости | Схема испытаний | |
Метод Виккерса | ||
Обозначение твердости HV Сущность метода заключается во вдавливании в испытуемый материал правильной четырёхграннойалмазнойпирамиды с углом 136° между противоположными гранями. Величина твёрдости по Виккерсу количественно равна отношению нагрузки Р к площади поверхности полученного пирамидального отпечатка. |
![]() |
|
Метод Бринелля | ||
Обозначение твердости HB Твёрдостьопределяется по диаметру отпечатка, оставляемому металлическим шариком, вдавливаемым в поверхность. Твёрдостьвычисляется как отношение усилия, приложенного к шарику, к площади отпечатка, (причём площадь отпечатка берётся как площадь части сферы, а не как площадь круга. |
![]() |
|
Метод Роквелла | ||
Обозначение твердости HRA, HRB, HRC Метод Роквелла основан на измерении глубины проникновения твёрдого наконечникав исследуемый материал при приложении одинаковой для каждой шкалы твёрдости нагрузки (обычно 60, 100 и 150кгс). В качестве инденторов применяются прочные шарики иалмазныеконусы с углом при вершине 120° со скруглённым острым концом. Из-за своей простоты, скорости по сравнению с другими методами и воспроизводимости результатов он является одним из наиболее распространённых методов испытаний материалов на твёрдость. |
![]() |
Основные преимущества таких испытаний заключаются:
- в возможности осуществления измерений непосредственно на детали,
- простота,
- оперативность испытания,
- компактность приборов.
Твердость стали определяется режимом термообработки и химическим составом, прежде всего содержанием углерода.
Повысить твердость стали можно:
- термообработкой;
- химико-термическими методами (например, легированием, хромированием и т.д.);
- механическими способами (наклеп, старение, прокатка и др.).
4. Испытания на коррозионную стойкость
Испытания на коррозионную стойкость – это способы оценки ресурса исследуемого объекта эксплуатироваться под действием коррозионно-активных сред. Целью таких испытаний является определение соответствия продукции требованиям длительной безопасности ее использования. В результате испытаний определяются: скорость и тип коррозии, состав и свойства продуктов коррозии, уровень эффективности антикоррозионных покрытий.
Данный вид испытаний востребован в следующих отраслях: судостроение, нефтегазовая промышленность, машиностроение и строительство.
Результаты, полученные в результате исследований, делают возможным с большой степенью точности прогнозировать операциональный ресурс продукции, однако такие испытания требуют много времени, т.к. в реальности коррозия развивается с медленной скоростью.
5. Методы технологических испытаний
Используются для исследования возможностей сплава подвергаться деформации при условиях, наиболее близких к рабочим.
К технологическим испытаниям относятся:
Испытания на сплющивание | ||
Проба на сплющивание трубынеобходима для определения способности металла подвергаться деформации сплющивания. Образец длиной, равной примерно наружному диаметру трубы, сплющивают ударами молотка (молота, кувалды) или под прессом до размеров, указанных в технических условиях. Образец считается выдержавшим пробу, если в нем после расплющивания отсутствуют трещины или надрывы. |
![]() |
|
Испытания загиб | ||
Изгиб —это вид деформации, характеризующийся искривлением оси или срединной поверхности деформируемого объекта под действием внешних сил или температуры, встречается в строительных конструкциях, деталях и узлах машин. Целесообразность проведения испытаний на изгиб определяется широким распространением изгиба в практике нагружения деталей. |
![]() |
|
Испытания раздачу | ||
Испытаниеметалланараздачу. Для сварныхтруб– это испытаниепрочности сварного шва. Процедураиспытаниярегламентируется специальным стандартом (ГОСТ 8694) и его разновидностью (ГОСТ 11706). Дляпроведения испытанияизтрубывырезают кольцевой образец определённой ширины.Испытаниепроводят на универсальных испытательных машинах или прессах. В результате определяется один показатель: величинараздачиобразца конусной оправкой до разрыва. |
|
|
Испытания бортование | ||
Испытание на бортование трубзаключается в отбортовке отрезка трубы с образованием фланца заданного диаметраD.Такое испытание широко применяется, например, в производстве паровых котлов с дымогарными трубами. |
![]() |
|
Испытания осадку | ||
Испытание на осадку в холодном состоянииприменяют для определения способности металла принимать заданную по размерам и форме деформацию сжатия. Испытаниям подвергают прутки, направленные в ковку и предназначенные для изготовления болтов, заклепок и т.д. Образец должен иметь диаметр, равный диаметру испытуемого прутка, и высоту, равную двум диаметрам прутка. В этой пробе образец осаживают ударами кувалды до высоты, заданной техническими условиями. |
![]() |
|
Испытание на выдавливание | ||
Испытание на выдавливаниеприменяют для определения способности листового металла подвергаться холодной штамповке и вытяжке. Образец закладывают в специальный прибор, в котором пуансоном с шаровой поверхностью выдавливается лунка до появления первой трещины в металле. Характеристикой пластичности металла является глубина лунки до разрушения металла. |
![]() |
6. Контроль структуры материалов
К металлографическим исследованиям относится макроанализ и микроанализ, заключающиеся в изучении под микроскопом структуры поверхности обработанного шлифа.
Данный вид исследований применяется в металлургической, атомной, аэрокосмической промышленностях, энергетике и автомобилестроении.
Металлографические методы
Макроскопический анализ
Макроанализ проводится при предварительном изучении стальных образцов.
Макроструктура – структура сплава, определяемая визуально или при увеличении до 30 раз.
Макроанализ состоит из 4х этапов:
- отбор проб
- подготовка проб
- изучение макроструктуры
- заключение результатов
Макроструктуру исследуют:
- на поверхности образца (литой заготовки, поковки после мех.обработки);
- на поверхности излома
- на макрошлифах – отшлифованных и спец.подготовленных поверхностях.
Макроанализ позволяет выявить:
- нарушение сплошности металла (усадочную рыхлость, газовые пузыри, пустоты, трещины);
- химическую неоднородность в распределении некоторых элементов (например, ликвацию серы и фосфора);
- неоднородность строения сплава после горячей обработки давлением (например, фигуры течения металла, волокнистость и др.);
- макростроение сварного шва;
- вид излома, по которому можно установить характер разрушения образца или детали
- наличие неметаллических включений - примесей, находящихся в затвердевшем сплаве в виде отдельных включений маленького размера.
Микроанализ
Осуществляется с использованием оптического микроскопа с увеличением до 2000 раз. Микроанализ позволяет:
- определить микроструктуру;
- определить фазовый состав;
- оценить количество, форму, размер и распределение различных фазовых составляющих сплава.
Для проявления микроструктуры используются травление, обеспечивающее выборочное растворение фаз химическим или электрохимическим способом. К наиболее используемым относится травление в растворах кислот, щелочей и солей, когда при наблюдении под микроскопом изображение рельефа на поверхности контрастное.
1. Методы определения содержания элементов
Спектральный анализ (Спектрометрия)
Основывается на изучения спектров излучения, поглощения или комбинационного рассеяния атомного и молекулярного состава вещества.
В основе данного метода лежит свойство молекул при определенных условиях (т-ра, давление) изменять интенсивность и спектр светового излучения и на уникальности спектра испускания, характерной каждому хим.элементу.
Спектральный анализ позволяет провести качественный и количественный анализ вещества: определить процентное содержание элементов в сплаве и соответствие его ГОСТ.
Преимущества применения спектрального анализа:
- Высокая чувствительность позволяет определить с большой точностью процентное содержание элемента в составе многокомпонентного сплава, что широко применяется в установлении марки сталей и сплавов.
- Позволяет определить одновременного наличие в сплаве более 20 элементов.
- Изучение осуществляется без разрушения образца.
- Возможность определить присутствие элемента даже в очень малом количестве.
- Высокая производительность.
- Отсутствие сложной пробоподготовки.
К недостаткам относятся:
- Высокая стоимость оборудования
- Возможны проблемы с оптической и электрической стабильностью.
Стилоскопирование
Данный метод базируется на исследовании спектра паров сплава с поверхности, накаленных электрической дугой.
Этот метод позволяет:
- осуществлять спектрометрию высоко качества;
- определять наличие легир. составляющих сплава;
- классифицировать по маркам сталей и сплавов;
- анализировать химический состав сплава.
НЕРАЗРУШАЮЩИЙ КОНТРОЛЬ (НК)
Неразрушающий контроль позволяет осуществить проверку надежности не только всего объекта, но и его составляющих без демонтажа объекта и с сохранением его эксплуатационных характеристик.
Виды НК:
2.1 Визуальный и измерительный контроль
2.1 Визуальный и измерительный контроль (ВИК)
ВИК это первичный метод дефектоскопии и имеет следующие преимущества: информативность, низкая стоимость проведения, простота и скорость.
ВИК позволяет:
- проверить качество подготовки объекта для сварки;
- проверить сварочные швы;
- определить качество металла;
- зафиксировать присутствие видимых дефектов: коррозия, наплывы, вмятины
Внешний осмотр производится:
- визуально:
- с применением простых оптических приспособлений (зеркало, лупа)
- с использованием более сложных устройств, позволяющих выявить даже небольшие дефекты.
2.2 Ультразвуковой контроль (УЗК)
Ультразвуковая дефектоскопия является широко востребованным основным методом НК и сводится к обнаружении дефектов посредством эмиссии и приема ультразвуковых волн, и дальнейшего изучения амплитуды и формы колебаний, времени и остальных показателей с помощью ультразвукового дефектоскопа.
- В основе работы УЗК лежит тот факт, что в гомогенном материале акустические волны не меняют траекторию распространения.
- Отражение звуковых волн происходит от границы сред с отличными удельными акустическими сопротивлениями.
- В случае наличия в стали неметаллических включений, которые нередко содержат воздух, с намного меньшим удельным сопротивлением, отражение будет фактически полным.
- Разрешающая способность УЗК анализа зависит от длины акустической волны, т.к. при очень малом размере дефекта (меньше 1/4 длины волны), практически не происходит отражения волны от препятствия.
- Поэтому целесообразно применение ультразвуковых колебаний, имеющих высокую частоту. Однако, с увеличением частоты волн происходит их затухание по глубине, что лимитирует достижимую глубину анализа. Вследствие этого УЗК металла в наибольшей степени осуществляется на частотах 0,5-10 МГц.
- УЗК относится к необходимым процедурам при производстве многих деталей в авиационной, атомной промышленности, машиностроении и др.
- УЗК поможет обнаружить трещины, несплошности, поры, непроваренные швы, расслоения и т.д.
-
Достоинства УЗК:
- высокая чувствительность к выявлению трещинообразных дефектов;
- широкий диапазон толщин и большой спектр материалов;
- благодаря малым габаритам УЗК аппаратуре есть возможность контроля в труднодоступных местах, а также возможность получения результатов на месте;
- относительно небольшая стоимость;
- безвредность метода для исполнителя анализа и окружающей среды (в отличие от рентгеновской дефектоскопии).
-
Одновременно с этим, недостатками метода являются:
-
Разнообразие требований, обозначающихся при потребности использования УЗК, вызвало создание и применение разных методов, которые подразделяются на 2 группы (ГОСТ 23829-85 ):
- активные методы - основаны на эмиссии и приеме волновых колебаний (наиболее распространены);
- пассивные методы – только на приеме колебаний и волн.
Классификация акустических методов:
Методы | Описание |
Методы прохождения | выявляют глубинные дефекты типа нарушения сплошности, расслоения. |
Методы отражения | выявляют дефекты типа нарушения сплошности, определяет их координаты, размеры, ориентацию путём прозвучивания изделия и приёма отраженного от дефекта эхо-сигнала. |
Импедансный метод | предназначен для контроля клеевых, сварных и паяных соединений, имеющих тонкую обшивку, приклеенную или припаянную к элементам жёсткости. |
Методы свободных колебаний | применяются для обнаружения глубинных дефектов. |
Методы вынужденных колебаний (резонансные) | применяются в основном для измерения толщины изделия и для обнаружения зоны коррозионного поражения, расслоений в тонких местах из металлов. |
Акустико-эмиссионный метод | обнаруживает и регистрирует только развивающиеся трещины или способные к развитию под действием механической нагрузки (квалифицирует дефекты по степени их опасности во время эксплуатации). |
2.3 Радиографический контроль
Основывается на свойстве неравномерного поглощения гамма-излучения при различной толщине и составе.
Данный метод может указать на минимальные дефекты. Легче всего определить дефект, такого же размера, как и пучок излучения.
2.4 Капиллярный контроль
Относится к одному из наиболее чувствительных исследований неразруш. контроля.
Основывается на способности специальной индикаторной жидкости просачиваться в дефекты (поверхностные или сквозные), и оставлять следы, видимые визуально или могущими быть зарегистрироваными преобразователем.
Данным контролем выявляют:
- локализацию дефекта,
- его величину,
- направленность.
Применяется для контроля объектов разной формы и габаритов из цветных и черных металлов и сплавов, неферромагнитных веществ (стеклянные, пластмассовые..).
2.5 Магнитный контроль
Осуществляется с целью для нахождения поверхностных дефектов в ферромагнетиках. В основе метода лежит исследование магнитных полей рассеяния возле намагниченных материалов. На локацию дефекта указывают измененные магнитные потоки.
Данным способом выявляются:
- немет. включения,
- щели, углубления,
- волосовины,
- флокены.
2.6 Тепловой контроль
Этот подход представляет собой основную технику для анализа состояний различных объектов, основываясь на анализе неоднородности их тепловых полей.
Он включает в себя регистрацию и трансформацию инфракрасного излучения в диапазон видимого света и разделяется на несколько категорий, включая анализ интенсивности теплового излучения, измерение температур, контроль теплопроводности и тепловизионный контроль.
Тепловая диагностика находит применение во многих областях, таких как строительство, производство и энергетика, благодаря своим ключевым преимуществам: гибкость в применении, быстрота выполнения, высокая эффективность и возможность осуществления измерений на расстоянии.
2.7 Вихретоковый контроль
Данный метод основан на способности внешнего электромагнитного поля вступать во взаимодействие с вихревыми токами.
В качестве источника электромагнитного поля выступает вихретоковый преобразователь (ВТП) — это индуктивная катушка, через которую пропускается ток, генерирующий электромагнитное поле. Это поле, в свою очередь, индуцирует вихревые токи в исследуемом объекте, что приводит к возникновению электродвижущей силы (ЭДС) в ВТП или изменению его сопротивления. В результате измеряется напряжение или изменение сопротивления в индукционной катушке.
Вихретоковое тестирование применяется для выявления различных дефектов, анализа характеристик объектов, и используется для:
- анализ сварных и резьбовых соединений;
- контроля поверхности внутренних каналов роторов турбин;
- определение толщины защитных покрытий, тонкостенных труб и листового проката;
- обнаружение коррозии;
- оценка качества термообработки материалов;
- определение состава материалов;
- измерение глубины поверхностных дефектов, таких как трещины, на электропроводящих материалах.