Металлообработка и изготовление конечных деталей любой сложности по чертежам Заказчика на ЧПУ станках
Наши возможности
Компания Апгрейд оказывает услуги по металлообработке и изготовлении конечных деталей из металла любой сложности по чертежам Заказчика на ЧПУ станках качественно и по конкурентным ценам.
Располагаем собственным парком современных ЧПУ станков и штатом высококвалифицированных технологов и инженеров.
Имея большой опыт работы с металлом, собственное производство кованых, штампованных, литых заготовок и складское наличие металлопроката, беремся за изготовление конечных деталей любой сложности по чертежам/образцам заказчика и гарантируем качество и соблюдение сроков выполнения заказов.
Выполняем штучные заказы и серийное изготовление для промышленных производств. Оказываем полный спектр услуг по механической обработке от разработки чертежей по эскизу или образцу Заказчика, до сборки и доставки продукции.Виды металлообработки на станках с ЧПУ, которые мы выполняем: Отправить заявку
Собственный парк современных токарных станков с ЧПУ
Наше оборудование позволяет осуществлять высокоточную механическую обработку крупногабаритных и тяжелых заготовок из стали, чугуна, алюминия и меди с диаметром до 2000 мм, высотой до 1200 мм и весом до 50 т.
Характеристики обрабатываемых заготовок
Максимальный диаметр устанавливаемой детали | Ø 2000 мм |
Максимальная длина обрабатываемой заготовки | 9500 мм |
Максимальная высота обрабатываемой заготовки | 1900 мм |
Максимальный вес обрабатываемой заготовки | 63 т |
Максимальный диаметр сверления | 100 мм |
Диапазон нарезаемой резьбы | М80 |
Максимальный диаметр обрабатываемых отверстий | Ø 450 мм |
Максимальная глубина сверления | 9500 мм |
Класс точности (ГОСТ 8—82Е) | Н |
Материал обрабатываемых заготовок | Стали и сплавы, чугун, цветные металлы |
СПИСОК ОБОРУДОВАНИЯ
ФРЕЗЕРОВАНИЕ | ТОКАРНАЯ ОБРАБОТКА | СВЕРЛЕНИЕ И РАСТАЧИВАНИЕ |
1) Горизонтально - фрезерный центр DOOSAN HM 800 с ЧПУ 2) Фрезерный обрабатывающий центр VMC1055 с ЧПУ 3) Продольно-фрезерный станок 6620 4) Зубофрезерный вертикальный станок 5А342 |
1) Токарно-винторезный станок ДИП500 с ЧПУ 2) Токарный станок STAR STL8 с ЧПУ 3) Токарно-винторезный станок 1A670 4) Токарно-карусельный вертикальный двухстоечный станок 1М557 5) Токарный станок TOS SUI 40 |
1) Радиально-сверлильный станок 2А576 2) Радиально-сверлильный станок 2Л540 3) Вертикально-сверлильный одношпиндельный станок 2С132 4) Станок глубокого сверления и растачивания РТ401 5) Горизонтально-расточной центр DOOSAN DBC 130 II 6) Горизонтально-расточной центр DOOSAN DBC 130 II 7) Токарно-винторезный станок ДИП500 с ЧПУ |
ВИДЫ МЕТАЛЛА, С КОТОРЫМИ МЫ РАБОТАЕМ
Характеристики | Особенности механической обработки |
КОНСТРУКЦИОННАЯСТАЛЬ Применяется при изготовлении конструкций, испытывающих большие нагрузки: прежде всего металлоконструкций и крепежных элементов, детали машин и оборудования. |
|
Преимущества ● устойчивость к механическим нагрузкам; ● сопротивляемость пластической деформации; ● высокая прокаливаемость; ● высокая значение вязкости; ● высокое значение хладноломкости.
Недостатки ● обратимая отпускная хрупкость (склонность); ● при деформации нарушается однородность; ● подверженность коррозии. |
● Отличаются высокой обрабатываемостью резанием и поддаются точению, сверлению, фрезерованию и т.д. ● С целью повышения обрабатываемости в состав углеродистых сталей вводят S, P и Pb, которые снижают трение и способствуют снижению скорости износа резцов, улучшение дробления стружки. ● При мех.обработке феррит имеет склонность: - налипать на резец с образованием на нем наростов; - образовывать длинную стружку; - образовывать заусенцы на деталях. ● Повышенный износ инструмента из-за повышенной твёрдости - рекомендуется обработка на пониженной скорости и/или использование смазочно-охлаждающей жидкости. |
ИНСТРУМЕНТАЛЬНАЯ СТАЛЬ Главное назначение инструментальной стали является изготовление деталей точной механики, режущих и измерительных предметов, штампов, точных деталей (шестеренки, подшипники, пружины и т.д.). |
|
Преимущества ● Невысокая цена. ● Хорошая обрабатываемость резанием и давлением. ● Высокая прочность и износоустойчивость. ● Хорошая прокаливаемость. ● Высокая пластичность в горячем состоянии. ● Низкая чувствительность к перегреву. ● Высокое сопротивление обезуглероживанию. ● Обычно плохая свариваемость.
Недостатки ● Вследствие отсутствия коррозионной стойкости требуются дополнительные защитные меры, особенно при эксплуатации во влажных или агрессивных средах; ● Возможность непредвиденного разрушения металла вследствие хрупкости при эксплуатации в низкотемпературных средах. |
● Рекомендуется мех.обработка на высоких темпах резки чтобы предотвратить наростообразование на резце, ухудшающее качество обработки поверхности. ● Кроки выбираемых резцов должны быть острыми для снижения налипания стружки, приводящее к ускоренному разрушению инструмента. |
СТАЛИ СПЕЦИАЛЬНОГО НАЗНАЧЕНИЯ | |
ЖАРОСТОЙКИЕ СТАЛИ (ОКАЛИНОСТОЙКИЕ) Жаростойкие стали применяются в следующих областях: ● Машиностроение. Из жаропрочных сталей создают корпуса и детали двигателей или силовых агрегатов, роторы и крыльчатки турбин, части компрессорных установок, корпуса, цилиндры и поршни ДВС, комплектующие для выхлопных систем. ● Производство нагревательных элементов: нагревательные котлы, камеры сгорания для печей или каминов, различные трубы и теплообменные конструкции. ● В авиационно-космической промышленности используется в производстве деталей, эксплуатирующихся при высокотемпературных нагрузках (например, реактивные, турбореактивные авиадвигатели, и корпуса космических аппаратов, теплозащитные экраны и обшивки). ● В химическом и нефтехимическом производстве применяются для изготовления изделий, эксплуатирующихся в высокотемпературных агрессивных средах (реакторов, колонн и резервуаров, трубопроводов). ● Энергетика: при создании изделий для АЭС. |
|
Преимущества ● высокая жаростойкость; ● сохранение физико-механических свойств при эксплуатации в агрессивных и высокотемпературных средах.
Недостатки ● высокая цена ● высокая себестоимость и трудоёмкость из-за наличия в химсоставе большого количества дорогостоящих легирующих элементов и необходимости выплавки в специальных печах (зачастую при вторичном переплаве); ● сложность при горячей обработке давлением (ковке) из-за необходимости специальных печей термообработки и риска образования трещин при ковке |
● Вследствие высокой твёрдости при мех.обработке требуется использование специальных инструментов и режимовы резания. ● При мех.обработке необходимо использовать смазочно-охлаждающие жидкости. ● Не рекомендуется мех.обработка на высоких оборотах по причине наклепа и высокой твердости так как это может привести к ускоренному износу резцов. С целью улучшения обрабатываемости рекомендуется проводить предварительную термообработку заготовок (отжиг или отпуск). ● При мех.обработки жаростойких сталей возможно неравномерное упрочнение по сечению резания заготовки, что приводит к низкой виброустойчивости. Для снижения этого эффекта требуется оптимальный подбор формы резцов со специальными режущими пластинами. |
ЖАРОПРОЧНЫЕСТАЛИ Нашли применение в следующих отраслях: авиационно-космической, нефтегазовой, металлургической, машиностроительной, пищевой и др. |
|
Преимущества ● Высокая жаростойкость и износостойкость ● Сохранение физико-механических характеристик в условиях агрессивных сред
Недостатки ● высокая себестоимость и трудоёмкость из-за наличия в химсоставе большого количества дорогостоящих легирующих элементов и необходимости выплавки в специальных печах (зачастую при вторичном переплаве); ● сложность при горячей обработке давлением (ковке) из-за необходимости специальных печей термообработки и риска образования трещин при ковке |
● При мех.обработке необходимо применять смазочно-охлаждающую жидкость вследствие резкого повышения температуры в области резания из-за низкой теплопроводности жаропрочных сталей. ● Жаростойкие стали обладают высокой истирающей способностью из-за содержащихся в них интерметаллидных или карбидных включений, что приводит к ускоренному изнашиванию резцов. По этой причине не рекомендуется мех.обработка на высоких оборотах. ● В процессе мех.обработки жаропрочных сталей возможно неравномерное упрочнение по сечению резания заготовки, что приводит к низкой виброустойчивости. Для снижения этого эффекта требуется: - оптимальный подбор формы резцов со специальными режущими пластинами; - применять систему охлаждения и специальные смазочно-охлаждающие жидкости. |
ИЗНОСОСТОЙКИЕ СТАЛИ Износостойкие стали и сплавы используются при: изготовлении деталей дорожно-строительной техники: ножей и режущих кромок, футеровок, лопастей; изготовлении деталей оборудования, работающего в карьерах: кузовов самосвалов, бункеров, футеровок, питателей; изготовлении деталей вторичной переработки: сит и решеток, ножей рециклинга, броней; изготовлении высокопрочных металлоконструкций |
|
Преимущества ● Высокие показатели твердости (НВ 450-600) при сохранении достаточной пластичности ● Сталь обладает хорошей свариваемостью ● Сталь обладает хорошей ударной вязкостью в различных температурных диапазонах
Недостатки ● Вследствие плохой обрабатываемости износостойких сталей резанием, при изготовлении деталей из них в основном используют методы литья без мех. обработки. |
● Вследствие высокой твердости износостойких сталей, для их механической обработки необходимо применять: - специальные режущие инструменты твердосплавные или с покрытиями из карбидов (например, титана), обладающие повышенной прочностью и износостойкостью - эффективную систему охлаждения специальными смазочно-охлаждающими жидкостями (для предотвращения перегрева резца и заготовки в зоне резания) |
БЫСТРОРЕЖУЩИЕ СТАЛИ Применяются при изготовлении режущих инструментов (фрез, сверл) |
|
Преимущества ● Высокая красностойкость ● Высокая износостойкость ● Высокая вязкость. ● Хорошая обрабатываемость резанием
Недостатки ● Эта сталь склонна к обезуглероживанию ● Необходимость в регулярной заточке режущих инструментов вследствие затупления режущей кромки ● Снижение остроты режущей кромки инструмента при резком охлаждении |
Вследствие высокой твердости износостойких сталей, для их механической обработки необходимо применять: ● специальные режущие инструменты твердосплавные или с покрытиями из карбидов (например, титана), обладающие повышенной прочностью и износостойкостью ● эффективную систему охлаждения специальными смазочно-охлаждающими жидкостями (для предотвращения перегрева резца и заготовки в зоне резания) |
ПОДШИПНИКОВЫЕ СТАЛИ Применяется в энергетике; судостроении; машино- и автомобилестроении; химическом производстве. |
|
Преимущества ● Сталь обладает высокой прочностью, износостойкостью и низкой хрупкостью; ● Сохраняют форму и размеры при эксплуатации при температуре более +100°С; ● Удовлетворительная обрабатываемость резанием и хорошая пластичность при холодной штамповке шариков или роликов.
Недостатки ● Наличие вредных примесей. ● Влияние неметаллических включений. Они являются концентраторами напряжений и могут стать причиной появления микротрещин. |
● В процессе производства подшипников особое внимание нужно уделять контролю микроструктуры на отсутствие ее дефектов, так как их наличие способствует снижению обрабатываемости заготовки. Рекомендуется проводить смягчающий сфероидизирующий отжиг чтобы получить структуру мелкозернистого перлита, обладающую повышенными свойствами пластичности и обрабатываемости резанием. |
АВТОМАТНЫЕ СТАЛИ Применяются: в автомобилестроении для изготовления авто-деталей (валов, шестерней, болтов, гаек), в электронике - детали электронных устройств, при изготовлении бытовой техники, для изготовления инструментов (гаечные ключи, отвёртки, плоскогубцы), в станкостроении (автоматная сталь используется при изготовлении станков и металлообрабатывающего оборудования), в судостроении (детали судовых корпусов, установок двигателей и систем управления), в производстве подшипников. |
|
Преимущества ● высокая обрабатываемость резанием (что важно при изготовлении изделий со сложной геометрией); ● невысокая себестоимость коне; ● ломкая легкоудаляемая из зоны резания стружка; ● возможность достижения высокого качества обработки поверхности; ● высокая прочность, долговечность; ●простота при выплавке.
Недостатки ● низкие вязкость и пластичность по причине наличия серы и фосфора. |
● рекомендуется обработка на высоких скоростях резания резцами, имеющими острые кромки; ● обеспечить эффективный отвод стружки. |
РЕССОРНО-ПРУЖИННЫЕ СТАЛИ Применяются при изготовлении изделий, не подвергающихся при длительных ударных нагрузках.: рессор автомобилей; упорных шайб; подшипников и тормозных лент; пружинных механизмов; фрикционных дисков; клинков, ножей, бритв; медицинских изделий. |
|
Преимущества ● стойкость к динамическим нагрузкам; ● эти стали просты в заточке; ● высокое сопротивление разрыву; ● высокое значение предела текучести; ● данная сталь хорошо куется; ● образует в процессе чернения на поверхности защитную оксидную пленку, придающую свойство коррозионной стойкости; ● относительная экономичность.
Недостатки ● подверженность коррозии; ● подверженность деформации при сильных ударах; ● плохая свариваемость. |
● Данные стали плохо режутся из-за большого сопротивления к деформации. Поэтому необходимо применять специальный режущий инструмент. ● После механической обработки заготовки рекомендуется подвергать обдувке дробью для уменьшения поверхностных напряжений. |
ЛИТЕЙНЫЕ СТАЛИ Литейные стали нашли применение в следующих областях: химическая и нефтехимическая промышленность, энергетика, судостроение, добывающая, машиностроение и др. |
|
Преимущества ● Хорошее свойство жидкотекучести ● Достижение высокой точности размеров заготовок; ● Возможность получения отливок различного веса и габаритов.
Недостатки ● Усадка при отвердевании сплава и склонность к растрескиванию ● Плохая ковкость и обрабатываемость резания ● Ликвация ● Склонность к газопоглощению жидких литейных сплавов |
● Поверхность литых деталей отличается высокой шероховатостью и неточностью, поэтому отливки для достижения точности размеров и необходимой чистоты поверхности часто требуют проведения механической обработки
|
КОРРОЗИОННО-СТОЙКИЕ СТАЛИ Использование: В химическом и нефтегазовом производстве для изготовления промышленного оборудования, реакторов, труб, ёмкостей и цистерн, эксплуатирующихся в агрессивных средах; В медицинской и фармацевтической сферах промышленности; При изготовлении бытовых приборов и кухонной утвари; В электроэнергетике; В строительной и машиностроительной сферах |
|
Преимущества ● Высокая коррозионная стойкость ● Прочность и износостойкость ● Гладкая поверхность и блестящий вид ● Температурная стойкость
Недостатки ● Высокая себестоимость ● Низкая обрабатываемость. ● Низкая свариваемость |
● Рекомендуется непрерывный режим обработки на невысоких скоростях из-за образования наклёпа. ● Рекомендовано применение твердосплавных или керамических режущих пластин с покрытием. ● Необходимо обеспечение хорошего отвода стружки и предотвращения нагрева в рабочей зоне, приводящего к преждевременному износу инструмента. ● СОЖ нужно подавать под высоким давлением. |
ТИТАН Применяется: ● В авиастроении – для изготовления двигателей, винтов, корпусов, крыльев, обшивки, трубопроводов, крепежа и др. ● В судостроении - для изготовления судовой обшивки, гребных винтов, валов, деталей палубной арматуры, антенн, приборов, рукояток, постоянно погружённых в морскую воду. ● В химическом и нефтехимическом производстве –насосы, компрессоры, фильтры и трубопроводы для перекачки кислот. ● В сфере атомной энергетики – при производстве оболочек и узлов ядерных реакторов, электродов. ● В медицине – при изготовлении инструментов, имплантов и др. ● В пищевом производстве – для изготовления пище-перерабатывающих аппаратов, котлов, тар взаимодействующих с кислыми и острыми пищевыми продуктами. ● В автомобильной промышленности – изготавливаются коленвалы, клапаны, втулки, детали подвесок и техники специального назначения. ● В электронике |
|
Преимущества ● Легкость, что широко используется для уменьшения веса конструкций ● Более высокая по сравнению с жаропрочной сталью тугоплавкость титана (1670 °C) позволяет применять его там, где жаропрочка не выдерживает ● Низкая теплопроводность титана позволяет использовать его в печах и двигателях, увеличивая их КПД (из-за снижения расхода энергии). ● Высокая прочность, сохраняющаяся при отрицательных температурах. ● Коррозионная стойкость (из-за образующейся на поверхности оксидной пленки, защищающей металл от влаги, ультрафиолета, многих щелочей и кислот). ● Высокая пластичность и хорошая обрабатываемость давлением (титан хорошо куется). ● Титан немагнитен.
Недостатки ● Высокие издержки и сложность при производстве титана: титановая шихта намного дороже железной и многих других цветных металлов, а способность жидкого титана взаимодействовать с атмосферными газами требуют выплавлять его в вакууме или в среде инертных газов, что требует дорогостоящего специального оборудования и печей. ● Сложность утилизации отходов производства титана ● Низкие антифрикционные свойства способствуют налипанию титановой стружки при мех.обработке. ● Титан плохо поддается резанию и сварке. ● Титан склонен к водородной хрупкости и солевой коррозии. |
● Титановые сплавы плохо поддаются обработке резанием. ● Титановая стружка склонна: - налипать на резец, снижая его износостойкость; - налипать и привариваться на резец, что влечет к изменению его геометрии, увеличению температуры в рабочей зоне, снижает его износостойкость и в итоге - к его преждевременному износу. ● Трудоёмкость механической обработки титановых сплавов в 3–4 раза больше, чем для углеродистых сталей, и в 5–7 раз выше, чем для алюминиевых сплавов. ● Для изделий из титановых сплавов существуют ограничения при финишном шлифовании по причине легкого образования прижогов, значительно снижающих усталостную прочность. ● В процессе мех.обработки необходимо использовать специальный режущий инструмент, специальную систему охлаждения из эмульсии, подаваемую под давлением. ● Из-за плохой теплопроводности титана, в процессе механической обработке основной процент тепла передаётся рабочему инструменту. |
АЛЮМИНИЙ Используется в следующих сферах: в авиационной и космической промышленностях, в строительстве, при изготовлении систем отопления и вентиляции, в электротехника (для изготовления проводов, экранирования и при напылении проводников на поверхности кристаллов микросхем), в пищевой отрасли и быту (для изготовления посуды, тары и упаковки для пищевых продуктов, деталей и корпусов мебели и бытового оборудования), в фармацевтической промышленности |
|
Преимущества ● Небольшой вес ● Хорошая штампуемость ● Коррозионная стойкость ● Невысокая цена Недостатки ● Склонность к окислению и разрушению в кислотных и щелочных средах ● Вследствие низкой твердости склонность к деформации ● Низкие антипригарные свойства |
● Из-за высокой теплопроводности алюминия в процессе механической обработки могут возникать деформация и прожоги заготовок. ● Образование длинной стружки (вследствие высокой вязкости алюминия), которая склонна наматываться на фрезу и забивать канавки, приводя к поломке инструмента. ● Склонность алюминиевой стружки наплавляться на режущую кромку резца, что приводит к его затуплению. ● При мех.обработке рекомендуется использовать смазочно-охлаждающие жидкости и выбирать режущие инструменты со специально геометрией. |
ЛАТУНЬ Применяется: При производстве авто-компонентов (валы, шестерни, подшипники), трубопроводной арматуры (фитинги, краны, заслонки и др), в электротехнической промышленности, в строительстве, дизайне и быту, в ювелирном производстве, при изготовлении осветительных приборов |
|
Преимущества ● Хорошие технологичность ● Высокая пластичность Недостатки ● Склонность к коррозионному растрескиванию |
● Для механической обработки латуни рекомендуется использовать специальные режущие инструменты с углом заточки 20–35°. ● Подбор оптимального режима обработки: в зависимости от габаритов заготовки скорость резания 600 – 1600 об/мин. Окончательная обработка осуществляется при пониженных скоростях. ● Использование системы охлаждения и смазки для предотвращения перегрева и износа инструмента. |
Мы подбираем для наших Клиентов оптимальные решения, исходя из экономической эффективности, характеристик и технических возможностей обрабатываемого материала.
Мы готовы выполнить заказ любого объема и сложности, обеспечив высокое качество и оптимальные сроки исполнения.
Оставьте заявку, а все остальные заботы мы возьмём на себя.
В ближайшее время с Вами свяжется наш специалист для уточнения деталей проекта.
После утверждения проекта, мы в согласованные сроки изготовим детали в полном соответствии с требованиями Заказчика и НТД.ФАКТОРЫ, ВЛИЯЮЩИЕ НА СТОИМОСТЬ МЕХАНИЧЕСКОЙ ОБРАБОТКИ
- Объём и сложность заказа;
- Габариты изделий;
- Материал изделий;
- Оборудование;
- Требования к механическим работам;
- Требования к точности и чистоте обработки;
- Наличие или отсутствие готового проекта;
- Сроки выполнения.
ПРОЦЕСС РАБОТЫ С КЛИЕНТОМ
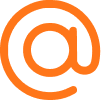
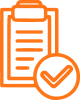
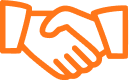
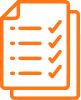
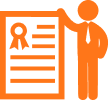
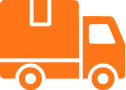
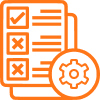
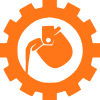
Фотогалерея
Наши преимущества
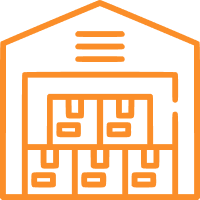
Постоянное складское наличие
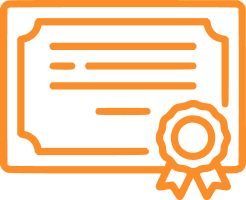
сертифицирована
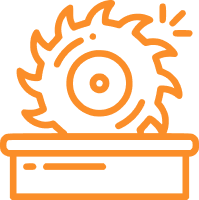
(резка, мех. обработка)

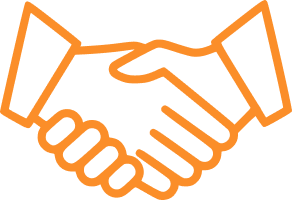
Персональный менеджер
Справочная информация
1.Изготовление деталей на станках с ЧПУ
Процесс механообработки с ЧПУ (с числовым программным управлением) является неотъемлемой составляющей в современной сфере промышленного производства, позволяя изготовлять высокоточные детали сложной формы с минимальными допусками, что в свою очередь повышает эффективность производства и качество продукции и сокращает расход материала.
Изготовление деталей на ЧПУ станках актуально для многих отраслей промышленности:
- в автомобильной отрасли: высокоточное исполнение деталей с низкими допусками на станках ЧПУ способствует увеличению производительности;
- в аэрокосмической отрасли: изготовление деталей на ЧПУ станках гарантирует необходимое строгое соответствие нормам и требованиям;
- в медицине протезы, имплантаты и хирургические инструменты изготовляются с применением ЧПУ станков что обеспечивает соответствие строгим стандартам повышенной точности, качества и биосовместимости;
- в электронной промышленности: для обеспечения точности, работоспособности и надежности деталей смартфонов, компьютеров и планшетов;
- в сельском хозяйстве: при изготовлении на ЧПУ станках деталей оборудования для ферм и сельхоз предприятий;
- в строительстве.
Использование ЧПУ позволяет:
- фиксировать показатели и формировать авто-отчёты, требуемые для контроля качества продукции (периодическая проверка позволяет выявить дефекты и избежать ошибок на начальных стадиях процесса);
- быстро создавать прототипы;
- масштабировать детали;
- организовывать крупносерийное производство;
- сократить ручной труд и повысить производительность;
- уменьшить количество дефектных изделий и повышение качества.
Все вышеперечисленное делает данную услугу востребованной и актуальной для компаний, стремящихся к оптимизации своих производственных процессов.
2. Изготовление конечных деталей
Технология Числового Программного Управления (ЧПУ) нацелена на автоматизацию процесса мех.обработки и заключается в программировании команд управления обрабатывающими инструментами ЧПУ станка, который выполняет эти команды, обеспечивая стабильность, точность и высокое качество.
Ключевые компоненты ЧПУ станков
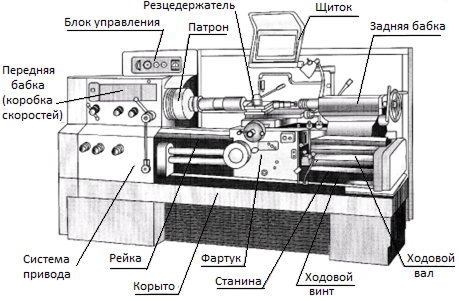
- Станок – осуществляет механическую обработку
- Блок управления - обрабатывает запрограммированные команды
- Система привода – выполняет команды обрабатывающими инструментами
Изготовление деталей на ЧПУ» является важнейшим достижением в технологии производства и имеет следующие преимущества:
- гарантия достижения высокоточных размеров, соблюдения жестких допусков и аккуратности;
- обеспечение стабильного качества и повышение надежности;
- снижение отходов сырья при мех.обработке;
- автоматизация процессов минимизирует ошибки и дефекты;
- снижение потребности в ручном труде;
- повышение общей эффективности производства;
- увеличение скорости обработки приводит к сокращению производственного цикла и увеличению производительности;
- оперативные выполнение заказов по механической обработке на ЧПУ станках повышает конкурентоспособность компании-производителя и выгодны клиентам;
- использование ЧПУ станков позволяет быстро масштабировать производство без ущерба для качества;
- большая гибкость при проектировании и создании изделий по заданным спецификациям, настройке, прототипирования и модифицировании конструкции продукции;
- возможность создания уникальных изделий высокой сложности;
- адаптируемость и универсальность ЧПУ станков обеспечивает возможность обработки разных материалов (металлов, пластмасс, керамику и композиты..) что дает возможность удовлетворить различные потребности клиентов.
Изготовление деталей на ЧПУ станках используется в следующих промышленных сферах:
1. Автомобильная промышленность:
- Высокая точность производства деталей на ЧПУ станках гарантирует соответствие каждой детали строгим допускам, что в свою очередь способствует увеличению производительности и надежности двигателей.
- Возможность изготовления нестандартных деталей и модификаций, возможность создания уникальных компонентов, нестандартных деталей и модификаций адаптированных под конкретные модели автомобилей. Это позволяет поддерживать производство автомобилей ограниченным тиражом и обеспечивает необходимую для индивидуальной настройки гибкость.
2. Аэрокосмическая промышленность:
- Высокоточное изготовление критически важных деталей аэрокосмической отрасли гарантирует соответствие строгим стандартам безопасности.
- Обеспечение высокоточной обработки легких материалов, имеющих критическое значение для снижения веса самолета (алюминия и титана), что способствует повышению топливной эффективности и производительности.
3. Медицинская промышленность:
- Критическая важность ЧПУ станков в данной отрасли объясняется возможностью изготовления высокоточных хирургических инструментов, которая жизненно важна для безопасности и эффективности хирургических процедур.
- Изготовление имплантатов с учетом индивидуальных особенностей пациентов на ЧПУ станках повышает удобство и функциональность.
4. Электронная промышленность:
- Высокоточное высверливание отверстий и вырезание рисунков сложной конфигурации на печатных платах (PCB) обеспечивает соответствие каждой платы точным спецификациям, функциональность и надежность электронных приборов.
- Способность ЧПУ станков легко обрабатывать детали со сложной конструкцией делает их незаменимыми в современном производстве электроники.
- Возможность создания корпусов для электронных компонентов, требующих соблюдения высокоточных размеров для обеспечения правильной посадки и функциональности электронных устройств.
- Возможность изготовления корпусов по индивидуальному заказу, адаптированных к конкретным устройствам, что позволяет создавать уникальные и инновационные продукты;
- Универсальность в обработке разных материалов позволяет удовлетворять различные требования при проектировании и гарантирует достижение высоких показателей точности и стабильности, требуемые для изготовления высококачественных электронных корпусов.
Типовые детали, изготавливаемые на ЧПУ станках
В машиностроительном производстве требуется производить множество разнообразных изделий разных форм массово, крупносерийно, среднесерийно или мелкосерийно:
- В массовом и крупносерийном производстве универсальность ЧПУ станков обеспечивает высокую производительность без необходимости переналадки (доля 20–25%).
- Бòльшая доля у среднесерийного и мелкосерийного производства.
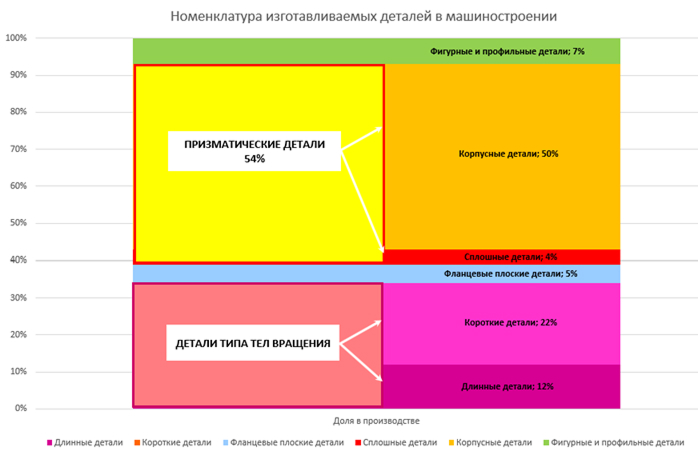
Изделия, имеющие форму тел вращения, могут иметь разную длину. При их производстве требуется использование на ЧПУ станках задней бабки (для поддержки концов детали), и люнета (для поддержки изделия посередине во избежание ее прогиба). Зачастую для мех.обработки подобных изделий достаточна только обработка на токарном станке (для обточки, точения канавок и фасок, подрезки торцов и др.).
При необходимости создания на длинномерных изделиях шпоночных пазов, сверления отверстий, фрезеровки поверхности, проводится механическая обработка на сверлильных и фрезерных станках.
Механическая обработка коротких деталей (валиков, фланцев, штуцеров и др.) часто осуществляется только на станках токарных.
При необходимости просверлить отверстия по окружности, поперечные отверстия, фрезировки шпоночных пазов применяется двухсторонняя механическая обработка, которая осущетсвляется:
- последовательно на разных станках (токарном, сверлильном, фрезерном),
- на одном токарном ЧПУ станке, имеющем поворотный шпиндель, противошпиндель и установленными в револьверной головке станка вращающихся инструментов (сверл, фрез).
Изготовлении фланцев и плоских деталей осуществляется с помощью сверлильных, фрезерных и координатно-расточных станков (имеющих вертикальную компоновку шпинделя), с одновременным обеспечением перемещения стола, салазок и шпиндельной бабки с инструментом по разным направлениям.
Объемные детали сложной формы с криволинейным профилем требуют одновременной координации в 3х координатах (в отдельных случаях по 4м или по 5ти) которое осуществляется на поворотном столе, обеспечивающим поворот шпинделя на нужный угол.
До создания ЧПУ станков процесс производства изделий сложной формы имел высокую трудозатратность и производился с применением оборудования разного типа.
Большую долю в машиностроении занимает изготовлении корпусных деталей, имеющих множество отверстий и плоскостей, для мех.обработке которых требуются различные режущие инструменты и возможность совместить черновую и чистовую обработки на одном станке.
Процесс изготовления конечных металлических деталей в машиностроении включает:
- Производство заготовок
- Механическая обработка
- Финишная обработка
- Контроль качества
Производство заготовок
Начальный этап: Резка и обработка исходного материала:
В соответствии с ГОСТ 14792-80 резка металла бывает следующих видов:
Методы резки и характеристики | Оборудование | |
Механическая резка металла при помощи лентопилочного станка | ||
Ленточнопильный станок – это высокотехнологичное оборудование, в котором используется бесконечная зубчатая лента, натянутая на два шкива. Лента движется с большой скоростью, совершая возвратно-поступательные движения, и, проходя по направляющим, осуществляет резку материала. Ленточнопильные станки применяются для:
|
![]() |
|
Рубкагильотинными ножницами | ||
Главным преимуществом гильотиной рубки металла является ровность отреза, отсутствие существенных дефектов и возможность резки металла большой толщины. Применяются для резки металла. В качестве основных режущих элементов используются нож подвижный и неподвижный, изготовленные из инструментальной или быстрорежущей стали, имеющих высокую твердость. |
![]() |
|
Гидроабразивная резка металла | ||
В качестве режущего элемента используется тонкая водная струя или струя водной суспензии абразивного материала, исходящая с высокой скоростью (≥ϑсвета в 3-4 р) и давлением (Р от 103-6*103 атм) из маленького отверстия (<1 мм). Гидроабразивная резка позволяет резать заготовки из стали, алюминиевых и титановых сплавов, имеющих толщину более 300 мм. Главным преимуществом данного метода резки является отсутствие дефектов и деформации. |
![]() |
|
Лазерная резка металла | ||
Резка металла сфокусированным лазерным лучом имеет следующие преимущества: - высокая точность - возможность резки любых сплавов: сталь (0,2-30 мм), коррозионностойкая сталь (0,2-40 мм), алюминиевые сплавы (0,2-25 мм) и сплавы других цветных металлов (латунные 0,2-12,5 мм; медные 0,2-16 мм) - высокий КПД - высокое качество поверхности реза - возможность изготовления объемных заготовок сложного контура |
![]() |
|
Плазменная резка металла | ||
Режущим инструментом выступает струя плазмы и ионизированного газа (аргон, азот, водород, кислород или воздух), которая генерируется плазмотроном прямого давления под действием электрической дуги. Плазменная резка имеет следующие характеристики:
Экономически оправдана резка:
|
![]() |
Механическая обработка
Механическая обработка включает следующие виды:
Фрезерная обработка металла |
Фрезерная обработка металла относится к основному виду механической обработки, которая позволяет изготавливать объемные металлические изделия различной сложности, формы и размеров. Процесс фрезерования выполняется на фрезерных станках и состоит из следующих этапов:
Завершение обработки или переход к следующей стадии.
При фрезеровании достигаются следующие показатели:
|
Токарная обработка металла |
Токарная обработка является одним из самых широко распространенных методов обработки металлов в промышленности, которая позволяет обрабатывать "тела вращения": валы, оси, диски, кольца, втулки, муфты, гайки и т.д. Процесс токарной обработки включает следующие этапы: 1) Закрепление заготовки в патроне, соединенном с двигателем станка ременной передачей; 2) Закрепление резца, с помощью которого будет происходить обработка, в полке, перемещаемой на винтовом штоке; 3) Сам токарный процесс происходит с помощью вращения металлической болванки в шпинделе и подачи резца к поверхности заготовки.
Виды токарных станков:
Современные токарные станки позволяют достигать высокой точности обработки деталей, однако абсолютно правильные размеры и формы остаются недостижимыми. Токарные станки позволяют достигать 4-3й класс точности, но при необходимости возможно достижение 1-го класса точности (при этом себестоимость мех.обработки ощутимо увеличится). |
Сверление металла |
Сверление металла – вид слесарной операции, использующийся для создания отверстий разной глубины и диаметра.
Процесс сверления включает следующие этапы:
Процесс сверления выполняется на станках следующих видов:
При сверлении достигается 9 - 13 квалитет точности и шероховатость Ra=±0,8÷25 мкм. |
Сборка и подгонка составных частей (если требуется):
1) Сборка деталей
Сборка деталей — это процесс соединения элементов в сборочные единицы, изделия.
Этапы сборочного процесса:
- Подготовка деталей к сборке: деконсервация, сортировка по размерам, укладка в тару.
- Установка элементов относительно друг друга;
- Узловая сборка: соединение элементов в комплекты, подузлы, агрегаты (механизмы).
- Общая сборка всего изделия.
- Регулирование и контроль: установка и выверка правильности взаимодействия частей и испытание машины.
2) Методы подгонки.
При сборке используются следующие методы подгонки:
Сборка методом подгонки по месту. Установленная точность замыкающего звена достигается уменьшением размера одного из составляющих звеньев на величину избыточной погрешности снятием стружки. Этот метод используется в единичном производстве.
Сборка методом подбора по месту. Установленная точность замыкающего звена достигается индивидуальным подбором одного или нескольких составляющих звеньев, действительные размеры которых позволяют компенсировать получившуюся погрешность. Этот метод имеет низкую степень взаимозаменяемости и может быть использован в условиях мелкосерийного производства.
Сборка с индивидуальной пригонкой деталей по месту. Установленный предел точности замыкающего звена в размерной цепи достигается изменением величины одного из заранее намеченных звеньев путём снятия дополнительного слоя материала. Этот метод применяется, когда размер замыкающего звена лежит за пределами допускаемых отклонений.
Финишная обработка
У любой стальной заготовки после производства есть различные дефекты (неровности, окалина, шероховатость...). С целью придания изделиям товарный вид, определенных свойств и приведения в пригодное для эксплуатации состояние, используют финишную обработку – определенные механические, термические, химико-термические методы.
Сборка и подгонка составных частей (если требуется):
Метод | Описание |
Шлифование | Проводится с целью удаления неровностей и поверхностных дефектов абразивным материалом. Приспособления для шлифовки: шлифовальная машина, абразивные бруски или наждачная бумага. |
Зеркальная полировка | Проводится с целью придания зеркального блеска поверхности заготовки путём снятия тонкого слоя материала с поверхности, что способствует ее выравниванию и устранению всех видимых царапин и неровностей. |
Сатинирование | Метод придания поверхности металла матового, немного шероховатого вида. Для создания нужной текстуры поверхность детали обрабатывается абразивными материалами. |
Гальваническое покрытие | Проводится для повышения коррозионной стойкости и улучшения внешнего вида. Заключается в покрытии поверхности слоем другого металла или металлоида при погружении заготовки в ванну с электролитом, через которых проходит электрический ток. |
Пескоструйная обработка | Применяется для очищения и выравнивания поверхности заготовки, для придания ей матовой поверхности, удаления старого слоя краски или ржавчины перед дальнейшей обработкой детали. Основывается на использовании высокой скорости абразивных частиц, направленных на поверхность металла. |
Оксидирование | Проводится с целью повышения коррозионной стойкости, долговечности и для покрытия декоративным цветом. |
Лазерная обработка | Основывается на применении лазерных лучей для мех.обработки поверхности металлической заготовки. |
Термическая обработка | Заключается в нагреве и последующим охлаждением заготовки по определенному режиму с целью изменения физико-механических свойств сплава (повышение прочности, жёсткости, коррозионной стойкости, уменьшение хрупкости и т.д.). |
Финишная обработка важна для долговечности и функциональности деталей, поскольку она позволяет:
- Избавиться от неровностей и дефектов. Например, шлифование создаёт ровную и чистую поверхность, а зеркальная полировка устраняет все видимые царапины и неровности.
- Снизить потери на трение. Это особенно важно для движущихся деталей, таких как трансмиссии, турбины, клапаны, подшипники, формовочные инструменты или шпиндели.
- Повысить коррозионную стойкость. Например, путем оксидирования увеличивается толщина природного оксидного слоя на поверхности металла, что способствует повышению долговечности и коррозионной стойкости.
- Придать деталям товарный вид. Финишная обработка проводится на завершающем этапе производства продукции с целью придания изделиям товарного вида.
4. Процесс выполнения включает в себя следующие этапы:
- Подготовка: Оценка требований к деталям, выбор технологии обработки и настройка оборудования.
- Обработка: Выполнение обработки детали с учетом заданных параметров.
- Контроль качества: Проверка размеров, формы и качества обработанных деталей.
5. Завершение: Очистка деталей от остатков и подготовка к дальнейшей обработке или сборке.